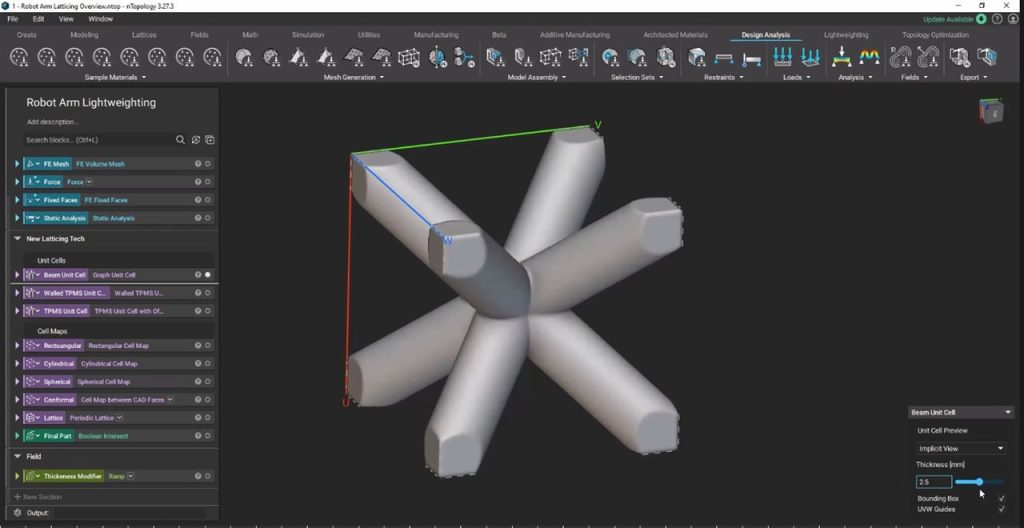
Generative design applications are famous for making strange looking, often unpractical parts. You’ve seen them because every publication shows them, always accompanied with boasts of how much weight was saved.
But engineers know that making spindly parts is not how lightweighting works. The spindly parts paraded before them, the result of topology optimization, will never hold up in design review – much less in real life. A more realistic approach would be to use lighter material, carefully reduce volume and maybe make it hollow. Like a round tube that is perfect in tension. Or monocoque. If you hollow a part, you can’t make it so thin that the walls collapse. So, you fill the void with something, anything… structural foam, perhaps, or a cellular structure. A honeycomb would work if it was a flat shape, like a floor panel, but your part is not like that. You need a cellular structure that can conform to a shape, that can vary according to a loads or restraints. Where have I seen that? Was it a dream?
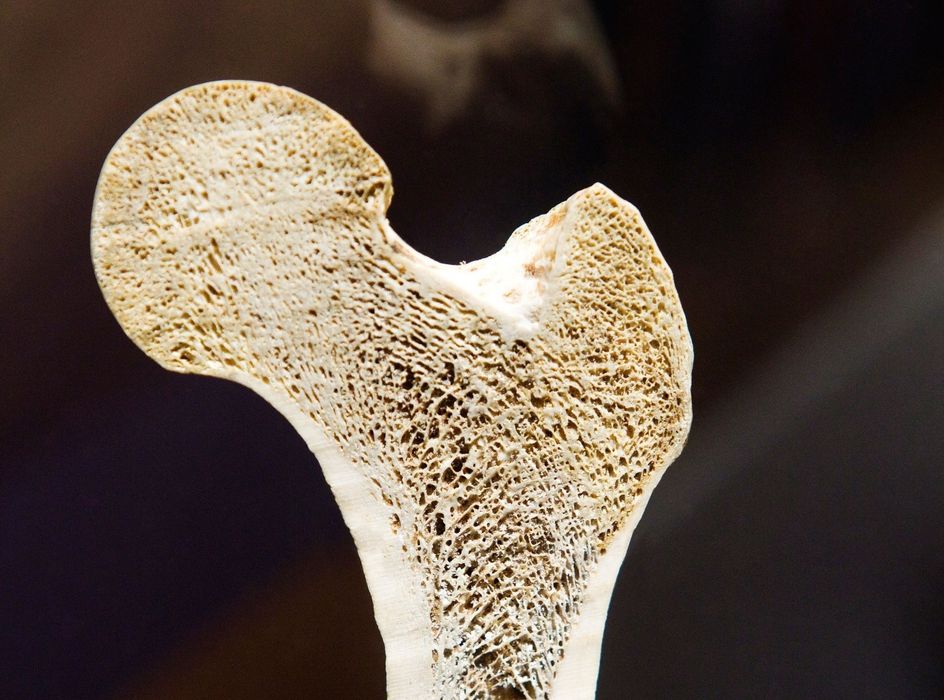
It’s not a dream for orthopedic surgeons, zoologists, naturalists… or any others who have studied bones where the irregular cell structure you were dreaming of can be found. The head of a femur, for example, is smooth and solid on the outside and remains solid for a few millimeters into the bone but gives way to microscopic cells at first then cells large enough to see in the middle. An engineer seeing a section of a femur for the first time will have these thoughts in quick succession: 1) God is an engineer and 2) why can’t my design software do this?
CAD software vendors and most generative design vendors, too, give lots of reasons why design software cannot do what Nature (or God, if you prefer) has done for so long and done so well. CAD software, almost all of them, built on standard geometry kernels, cannot handle the fractal-like detail of cells and lattices. There are simply too many faces for the software to generate and display. It’s a capacity problem.
But one company, nTopology, has found a way to handle the complexity. They have their own geometry kernel. They don’t rely on Parasolid, ACIS or one of the other B-rep (boundary rep) geometry kernels.
nTopology, arguably the most advanced generative design software, just increased its lead with its latest release with its “3 rd generation” of lattices.
nTopology now creates lattices with speed – lots of it. The company says that in one benchmark a lattice that took 45 to 60 seconds was rebuilt in 1-2 seconds. Lattices are created ten to one hundred times faster, they say. For a model with as many elements as lattice patterns create, speed to create and display all of them comes from harnessing the power of the graphical processing units, or GPUs, found in most workstations.
Indeed, the improvements in lattice generation are most intriguing. nTopology looks like it can lightweight a part like nothing else on the strength of its lattices. We requested a demo to see the new latticing for ourselves.
Todd McDevitt, nTopology head of product development, was kind enough to accommodate us. Todd, a mechanical engineer (PhD, University of Michigan) has worked at Ansys and MSC. He knows his way around simulation, the hidden engine of nTopology.
Read the rest at ENGINEERING.com