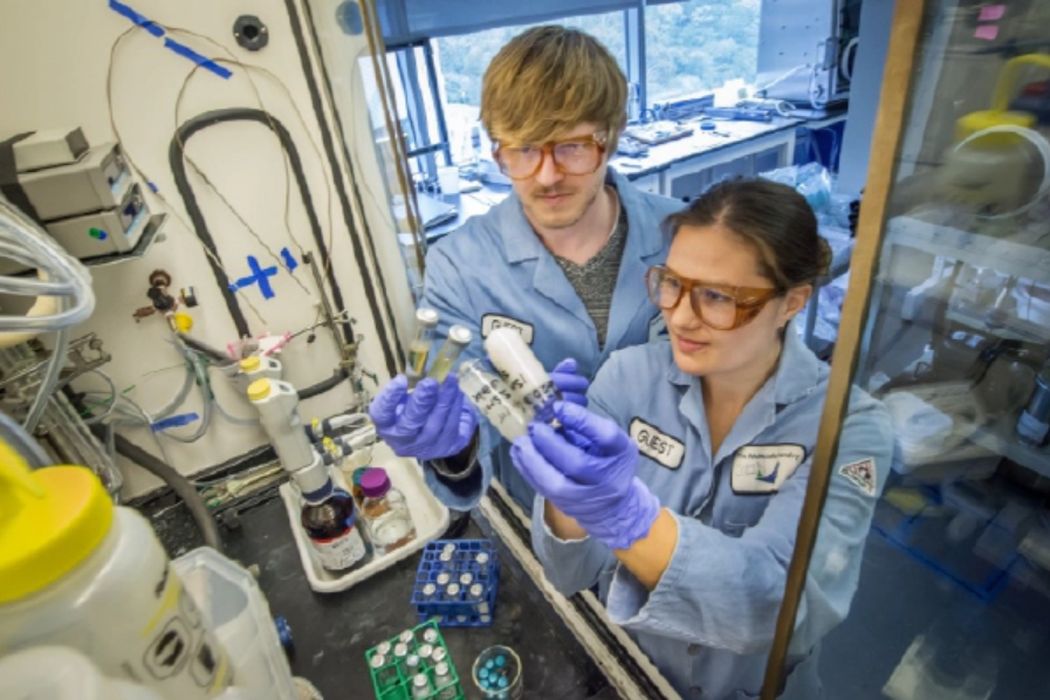
polySpectra founder and CEO shares his quest for the Holy Grail of additive materials.
“I was a hater about 3D printing,” confesses Raymond Weitekamp. “I was sitting there as a polymer chemistry PhD saying, ‘It’s a hot glue gun on a gantry. How could this be useful?’”
That’s not what you’d expect to hear from the founder of a company that produces resins for additive manufacturing. But in fact, Weitekamp didn’t hate the player—he hated the game.
“I realized that it ultimately boiled down to the fact that the material properties weren’t there for making end-use products,” explains Weitekamp, CEO of California-based polySpectra. “There was all this hype around 3D printing, but that’s not additive manufacturing, even though people like to use those words interchangeably. Additive manufacturing is making actual end-use products.”
Weitekamp resolved to help bridge this gap by developing 3D-printing materials that would be durable and safe enough to make the technology truly competitive with more traditional manufacturing processes, such as injection molding.
A New Class of Photopolymer
The chemistry underlying polySpectra’s Cyclic Olefin Resin (COR) was developed before Weitekamp had settled on 3D printing as his focus. Working under Nobel Prize winner Robert Grubbs at the California Institute of Technology, Weitekamp found a way to use light to activate Grubbs catalysts—transition metal carbene complexes that accelerate olefin metathesis.
“Basically, [COR] is a new class of photopolymer,” Weitekamp explains. Although the printing process for COR looks the same at the macroscopic level, the molecular mechanism underlying it is completely different.
Weitekamp started out using this technique to make photoresists, but he could see numerous potential applications, including stem-cell tissue scaffolds, nano-3D printing and optical metamaterials. A pair of meetings with two of the major players in additive manufacturing—Stratasys and Formlabs—led him back to the technology he’d initially dismissed.
“We were trying to figure out if these companies wanted better materials, and at this point we had no evidence that we could 3D print with this chemistry, but we knew what properties we could achieve,” says Weitekamp. “So, I told them we could get to 150 C working temperature and elongation at break of 15 percent at the same time, and both companies said, ‘If you can do that, it would be the Holy Grail of 3D printing.’ It took us many years and many millions of dollars after that to figure out how to massage our chemistry and adapt it from what I had figured out in grad school to be able to drop it into a 3D printer, but that’s the origin story of polySpectra.”
Today, polySpectra offers three resins: COR Alpha, COR Black and COR Bio. The first two are intended primarily for industrial applications, while the third is aimed specifically at the dental and medical device industries. All parts made from COR require a thermal post-curing process, either via a vacuum oven for high-throughput settings or using another polySpectra product called waveCure that works with consumer-grade microwave ovens.
The Balancing Act for 3D Printing Materials
If you’ve ever visited a booth for 3D printing (or additive manufacturing) at a trade show, you’ve probably noticed that the demo parts are often kept inside glass display cases. The reason is obvious: companies don’t want their precious demo parts damaged by butterfingered attendees. Of course, it also reveals something deeper about the 3D-printed parts themselves, i.e., that they’re delicate enough for damage from handling to be a concern.
“I had someone tell me that they always wanted to see a 3D-printed lattice that was strong enough to stand on,” Weitekamp recalls. “So, we actually did that, and we even encouraged people to jump on it!”
The point isn’t that parts made with polySpectra’s resins are the strongest 3D-printed parts you can find. Indeed, Weitekamp will be the first to admit that’s not the case. Nor do parts made with COR have the highest heat resistance. Instead, the goal is to strike a balance between the two, with the result being a material that’s much closer to conventional polymers.
“When people hold one of our parts in their hands, they tell us it doesn’t feel like SLA [stereolithography],” Weitekamp says. “There’s a kinesthetic experience that you can’t get from looking at pictures or watching videos.”
Of course, the mere fact that COR parts feel more like those produced via traditional manufacturing methods doesn’t mean additive manufacturing with COR can replace those methods for any given application. The same constraints that keep us from 3D-printing plastic cutlery and a host of other consumer goods—i.e., speed and cost—still apply. Nevertheless, more material options is good news for any engineer working with 3D printing polymers.
Read the rest of this story at ENGINEERING.com