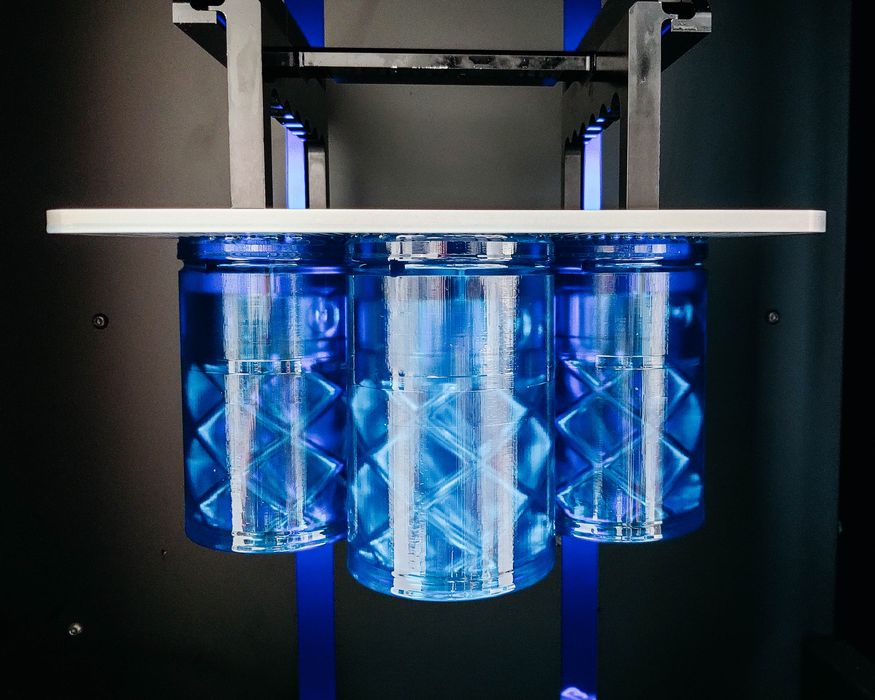
Nexa3D announced a very interesting partnership with Addifab that should supercharge the injection molding industry.
Hold on, isn’t this about 3D printing? What’s all this about injection molding?
Let me explain.
Addifab Freeform Injection Molding
Addifab is a Danish company offering a very unusual capability: 3D printed injection molds. But why would you want to do this?
Normal injection molding is typically done with metal molds that can be quite expensive to produce, not only because metal is used, but also because a milling process is required. The geometry of the mold must be very carefully designed to ensure that molded parts aren’t trapped inside the mold.
These requirements mean that typical injection molds are geometrically constrained, and much design effort is usually expended to ensure molds are usable. The result is parts that are not particularly radical in design, as they are in the 3D print world, where few if any geometric constraints are present.
Addifab’s technology overcomes this barrier by 3D printing complex molds that are then suitable for use as an injection mold. The secret is a unique resin that is capable of withstanding the tremendous forces and temperatures present during the injection process, where hot thermoplastic is shot into the mold.
The idea for using Addifab’s “Freeform Injection Molding Process” is to create a mold with a very complex geometry and then dissolve it after injection. This allows easy creation of very complex geometries for injection molded parts. In fact, almost any common material used for conventional injection molding can be used in the Addifab process.
Of course, these are one-time-use molds, but as printed they are far less expensive than a metal mold. This makes Freeform Injection Molding quite useful for small or low volume production runs, although the economics can work in many situations.
Back to Nexa3D. Why would these two parties connect?
Nexa3D Resin 3D Printing
Nexa3D manufactures a slick, high speed resin 3D printer, the NXE 400, that’s used by industry for production purposes. The partnership allows for the Addifab resin to be used in the Nexa3D equipment to produce molds — but at a faster production-level speed. Nexa3D said the NXE 400 has a print speed approximately 6.5X as fast as other typical resin 3D printers.
The arrangement allows use of Addifab resins in Nexa3D equipment, which can be provided to Addifab clients. In addition, Addifab will supply their post processing systems and consumables to Nexa3D customers using the Freeform Injection Molding process.
Addifab CEO Lasse Staal said:
“Injection molding is a complex process, and the tool building is the most complex part of the process. With Freeform Injection Molding, we provide injection molders with a fully transparent set of tools (no pun intended) that will allow them to fast-track tool designs and validations while raising the bar on tool innovation. Now we can take these capabilities to the next level by partnering with Nexa3D to broaden access and superpower performance.”
For Addifab, this deal provides a huge boost to their market, as every Nexa3D customer is now a potential client for their process and materials.
Production 3D Printed Injection Molds
For Nexa3D, this provides yet another powerful capability for their advanced resin 3D printing system, and can potentially unlock injection molding clients that might not have considered Nexa3D in the past.
Customers likely get the best outcome here, as the faster speeds of the NXE 400 will allow much more rapid production of one-time-use injection molds. The device also has a large build volume of 275 x 160 x 400 mm, allowing for a large number of molds to produced in each job run.
For an operation attempting to produce a large number of injection molded parts, the ability to make one-time-use molds more quickly could dramatically increase their throughput.
Nexa3D said the new system is available immediately to NXE 400 customers.
It’s fascinating to see how a very powerful capability can emerge when the resources of two 3D print companies are connected. I am hoping this partnership inspires a few more in the industry to produce additional functionality for operators.