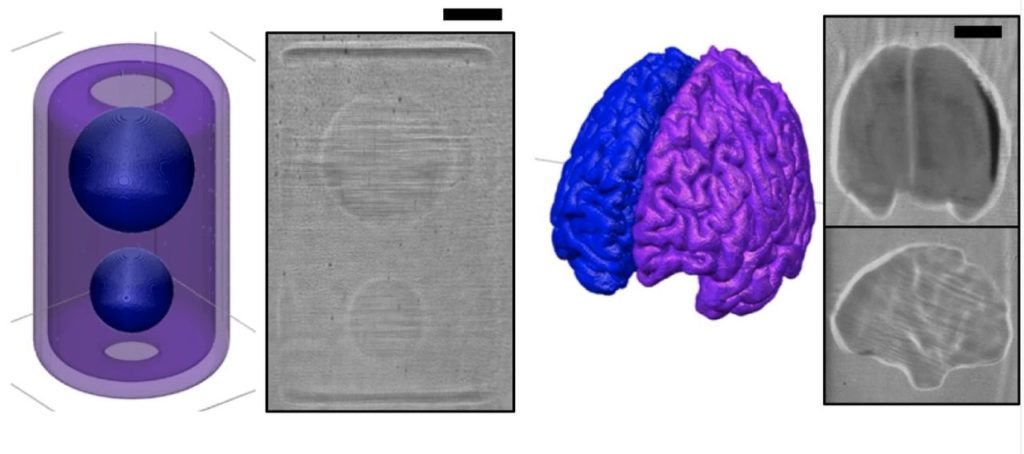
Researchers at the Technical University of Denmark announced the development of a new volumetric 3D printing process they call “TVP”.
“Volumetric” 3D printing is a relatively new technique that involves continuous and varying light projections into a rotating tank of clear photopolymer resin. The idea is like a reverse CT scan: instead of capturing images from a subject, the images are projected backwards to form the subject.
This technique is incredibly powerful, as it enables the printing of complete objects in only minutes or even seconds: the vat spins and the object grows as you watch. It is literally orders of magnitude faster than conventional additive processes.
Over the past couple of years I’ve posted several pieces on this fascinating technology, including:
- A look at the complexities of volumetric 3D printing
- A volumetric patent by Southern Methodist University
- Speeding up volumetric 3D printing
- The first commercial volumetric 3D printer by Xolo
- Thoughts, Questions and Implications of Volumetric 3D printing
- Adrian Bowyer’s “electric 3D printing” concept
- A list of which companies are currently working on Volumetric 3D printing
It is my opinion that once volumetric technology is perfected, it could very likely take over the market for much of the resin equipment due to its incredibly speedy results.
TVP Volumetric 3D Printing
What is the new development?
TVP, or “Tomographic volumetric 3D printing” uses dual wavelength light sources. The researchers were able to cure the photopolymer resin using a combination of visible (455nm) and UV (365nm) light simultaneously.
This “two color” approach allowed the researchers to create solid materials with not only high precision, but also internal mechanical property gradients. This is enabled due to the nature of the resin, which responds differently to each wavelength. This allowed them some control over the polymerization but moderating the strength of each wavelength.
They wrote:
“Our result presents a strategy for controlling the stiffness of material spatially in light-based volumetric additive manufacturing.”
And:
”The authors used visible light and 365 nm UV to realize spatially controlled microscopic chemical heterogeneity and macroscopic mechanical anisotropy.”
In other words, their dual-color approach allowed them to directly control the nature of the polymerization at points in 3D space. They explain a bit more:
“Here we show that a mixed solution of acrylate and epoxy monomers can be cured in a dual-color TVP setup to realize high precision control of internal mechanical properties. TVP excels at delivering predefined light doses to specific points in 3D. When operating in multicolor mode, TVP specifies the dose ratio between different wavelengths for each voxel, which translates to voxel-by-voxel chemical and mechanical property-customization when the aforementioned orthogonal polymerization is employed.”
This is a notable development in the still-nascent field of volumetric 3D printing. While there is at least one volumetric 3D printer coming (Xolo’s Xube), there clearly is a lot more to the technology yet to be explored.
Via Nature