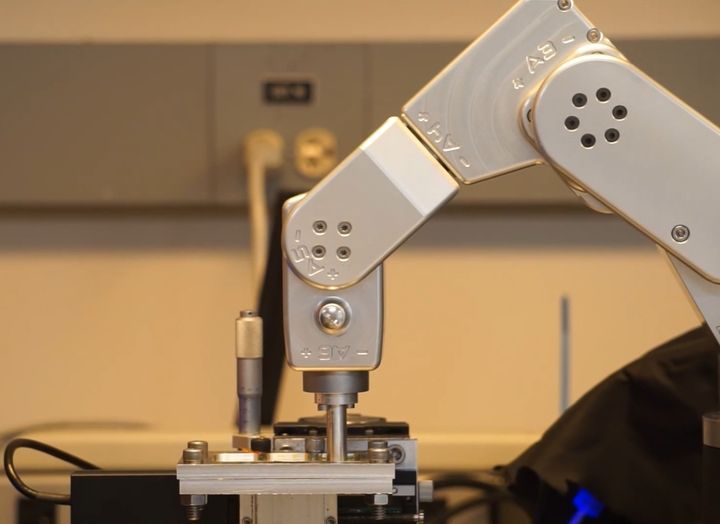
Researchers at Northwestern University have developed an incredible new approach for 3D printing with resin materials.
The new process is an adaptation of previous resin systems, which solidify a liquid photopolymer resin with light energy. Typically this is done by having a plate slowly rise and solidified material is added layer by layer. The process was first invented in the 1980s by Chuck Hull, who then parlayed the discovery into today’s 3D Systems corporation.
Resin 3D Printing
An entire industry erupted around this concept after 3D Systems’ patents expired, ranging from high-end commercial SLA systems to inexpensive desktop units costing only a couple hundred dollars. I think I have a few kicking around here, they are so common these days.
There have been some innovations in the resin process, perhaps most notably by Carbon, who invented a way to more rapidly 3D print the layers in resin by including a layer of oxygen between the tank and the resin. However, aside from that type of innovation there has been little more in the world of resin 3D printing.
Until now.
Northwestern 3D Printing Process
The Northwestern researchers did something incredible: they replaced the normally vertically operating resin platform with one controlled by a robotic arm.
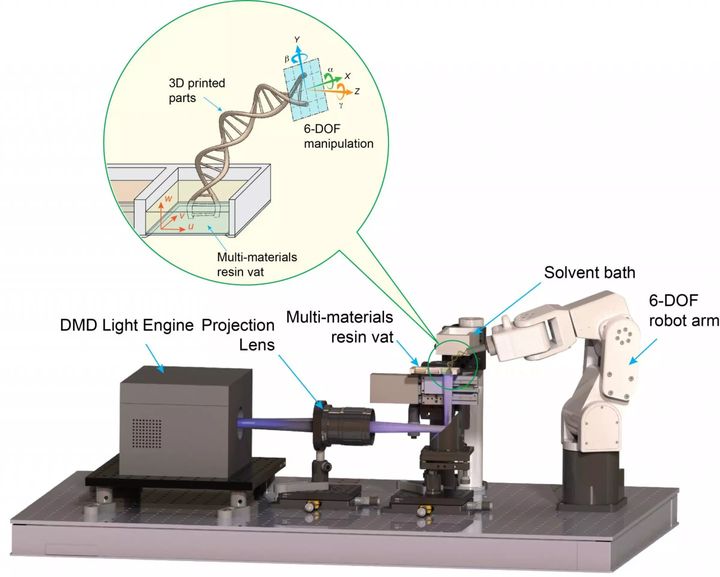
The robotic arm can raise the platform vertically, so that it moves exactly how a conventional resin printer might operate. However, it can also do this:
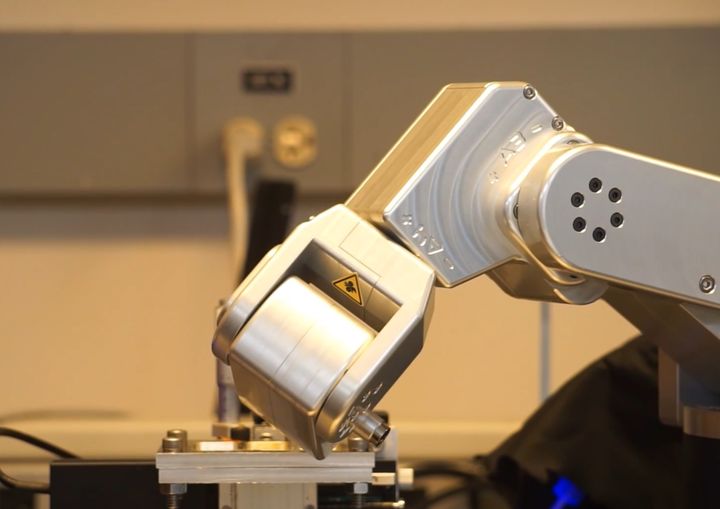
Suddenly the one-dimensional plate movement has now become three-dimensional!
Why do this? In the Northwestern material they show an example of a classic Eiffel Tower 3D print, but the neck of the tower is twisted. That’s due to the robotic arm moving non-vertically during the print. In other words the print’s geometry was changed DURING the the print job, not in CAD design or job setup.
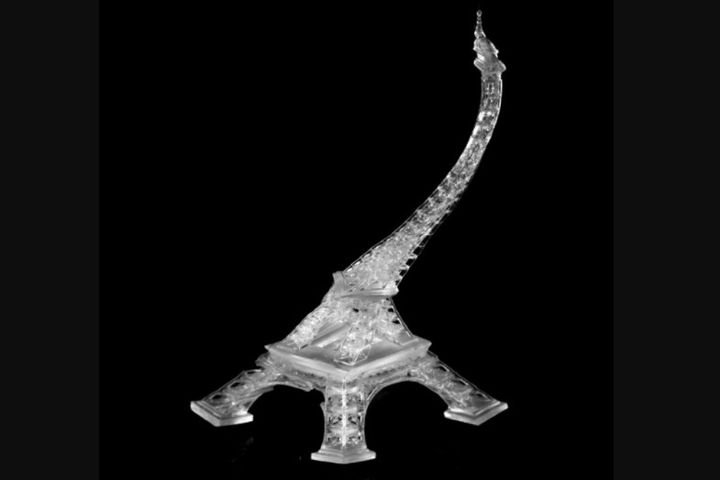
That’s an amusing print, and one might dismiss it as interesting but not particularly useful. However, there’s a lot more to the story.
Take a look at this video showing how a large object can be decomposed into a series of twist and turns by a moving print plate:
As you can see, there could be an incredible opportunity here to 3D print objects, for example, with less support material than would normally be required for resin 3D printers. That’s hugely beneficial, as picking off support from resin prints is an incredibly tedious manual effort.
But wait — there’s much more.
Imagine the print plate being twisted and turned during a print, gradually raising itself as the print appears.
Where does this stop?
In a normal resin 3D printer, the Z-axis has a limit. In a robotically controlled system like this, there is NO LIMIT other than the robotic arm’s reach.
In other words, you can 3D PRINT RESIN OBJECTS LARGER THAN THE MACHINE.
The robotic arm would simply have to support the print continuously as it emerges, and ensure that the “active” layer is securely presented to the build plane on the device. Try to visualize 3D printing a life-size sword on a resin 3D printer like this: the robotic arm would “pull” the sword out of the resin at a slight angle to its full length, twisting as required along the way.
Then you’d have a robotic arm wielding a sword, I suppose.
But you’d also have a resin 3D printer that is nearly the equivalent of today’s belt 3D printers that can print very large objects.
While Northwestern’s experiments seem to be at a rather small scale, there is no reason this concept could not be scaled up significantly in size. You would be limited only by the robotic arm’s size and lift capacity.
One more thing: apparently this process uses some form of continuous resin 3D printing, so that it does not have to stop moving the platform between layers like most resin printers must do. Apparently the process can 3D print up to “4,000 layers in approximately two minutes”, or 33 layers per second! This would significantly speed up printing operations, and would add to the value of this new process. I don’t know much about this part of the process, and will be looking into it further.
I’m stunned by this development. This is perhaps the most powerful 3D printing innovation I’ve seen in several years.
It’s a concept that could easily be made to work; there should be no technical barriers to making it a commercial process. The only stumbling block could be the cost of the robotic arm, but it’s possible there could be ways to reduce that effect.
Regardless, I have a suspicion this new approach could become a standard way of 3D printing in the near future.