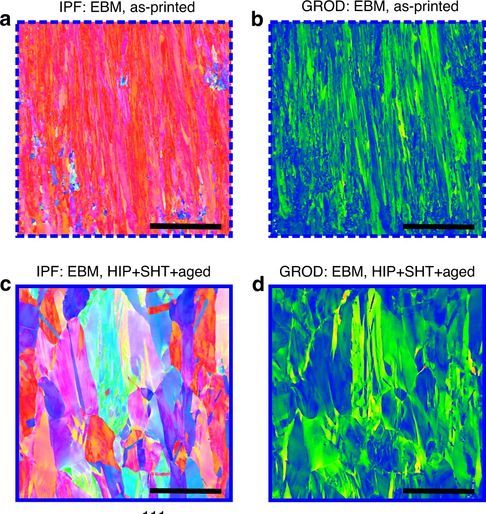
Research may have identified a new class of 3D printable metals that can overcome current limitations.
The limitations are caused by thermal effects. In most metal 3D printing processes, the metal powder or material is heated to the extreme temperatures necessary for them to melt. These temperatures are far higher than ambient temperatures, much greater than those required for polymer materials.
Because of that there are highly extreme thermal gradients occurring during the metal 3D printing process. While the active layer is hitting temperatures of 1000C, the rest of the chamber will be at a far lower temperature, and that includes the portions of the print that have previously been completed.
The print will be subjected to massive temperature differences throughout the print job, and this causes all kinds of issues. The mechanical stresses generated by the thermal gradient can cause the print to crack.
To overcome this effect, some metal 3D printer operators will devise complex support structures that, hopefully, can channel away some of that heat before things go wrong. However, the entire print undergoes stress that is abruptly relieved when it is cut off the build plate after printing.
In those cases the print can spring into its final shape, and that might not be the desired shape. It’s just very difficult to 3D print in metal.
But now researchers may have solved some of these issues. Researchers at UC Santa Barbara have developed a new class of metal materials that can overcome some of these stressful 3D printing conditions.
They’ve prepared a series of metal alloys that mix a target material with smaller, but equal amounts of cobalt and nickel. They say:
“These alloys are amenable to crack-free 3D printing via electron beam melting (EBM) with preheat as well as selective laser melting (SLM) with limited preheat.”
This is quite important as some applications require advanced materials that have not been easily 3D printable. With these new materials available, it will eventually be possible to 3D print more parts for advanced systems.
A typical application of this type would be for the blades used in aircraft engines and natural gas turbines. We’ve seen these parts 3D printed previously, but in order to build the highest-performing turbines more advanced materials must be used. That hasn’t been possible due to the cracking problem with metal 3D printing.
The researchers explain:
“The cracking susceptibility of high-performance engineering alloys including high 𝛾′ volume fraction Ni-base superalloys, high strength aluminum alloys and refractory alloys represents the major barrier to the use of these alloys for AM components in critical applications. For alloys that operate at relatively low temperature, such as high strength aluminum alloys, control of grain nucleation in the melt pool via functionalization of powder surfaces can mitigate the cracking problem21. However, this results in a small grain size, which is unfavorable for high-temperature operation. Thus, innovative alloy designs are needed for AM, especially for more severe environments.”
The researchers performed extensive testing on samples 3D printed in different processes to verify the results, suggesting there is a possibility the new materials could eventually make their way into commercial use.
Their introduction would certainly be welcomed by metal 3D printer manufacturers, as they would no doubt see an uptick in product take-up as more applications could be attempted.
Via Nature