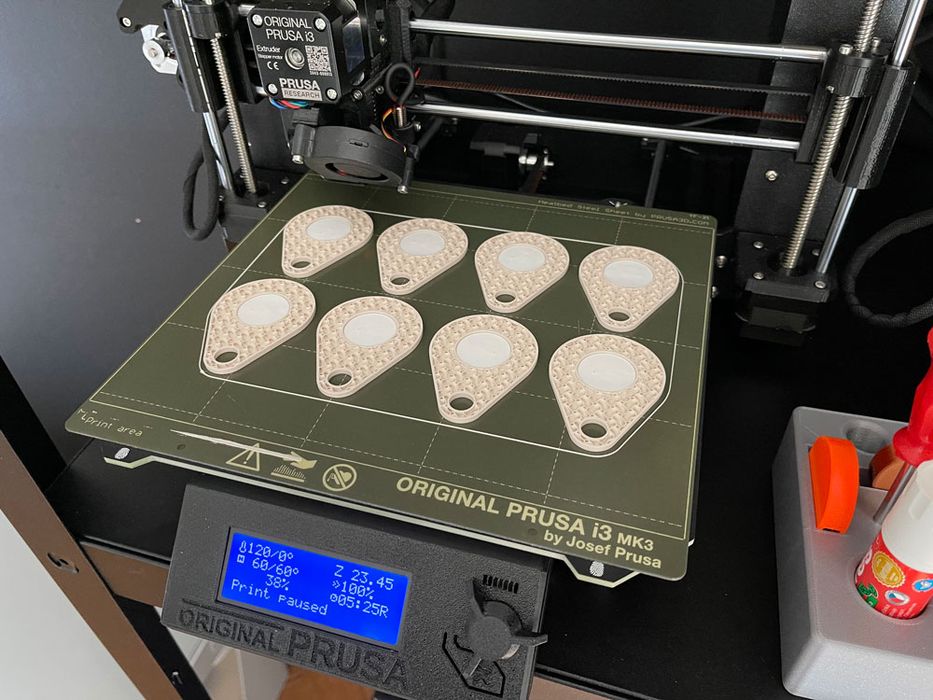
A new development program has been launched for 3D printing applications involving NFCs.
NFCs are tiny embedded radio frequency chips that are typically found in key fobs, credit cards and even mobile phones. They are unpowered electrical devices that activate when a signal from a “reader” is broadcast nearby. The NFC chip then simply responds with its code. The reader can then use that code for a variety of purposes. One example would be to complete a purchase with a credit card.
It’s always been possible to embed NFC chips inside of 3D prints. The process is technically straightforward: design a hollow inside a 3D model. Then, while printing it, pause the job and drop a thin NFC chip into the hollow. Complete the printing and you’ve made an object with an NFC chip inside.
However, that’s actually the easy part. The rest of the work to make that chip actually do something useful is much more challenging. It requires a database, logic, feedback and more.
That part of the work might be beyond teams that normally focus on the mechanical aspects of a 3D printed design, so the question is, how do you gain the necessary expertise and platforms to make the entire system?
A new program from Lostboyslab hopes to do so. They have a facility based on the “South Coast of Sweden” where they have been providing design and build services for some time. They’ve also built a cloud-based platform for NFC enablement called “whatt.io”, which can be used to power the application.
But what, exactly would you do with such a system? Lostboyslab explains:
“whatt.io is a cloud platform under development that enables a connection between the physical product and lifecycle product data from cradle to grave. NFC enabled parts using additive manufacturing connect the actual individual part to the whatt.io cloud platform, returning manufacturing, material, maintenance, assembly, recycling, spare parts and ownership information.”
The concept here is that a 3D printed part would have an NFC chip that could be used to identify the part and other associated information. This could be quite useful in a variety of situations that a part might experience over its lifetime.
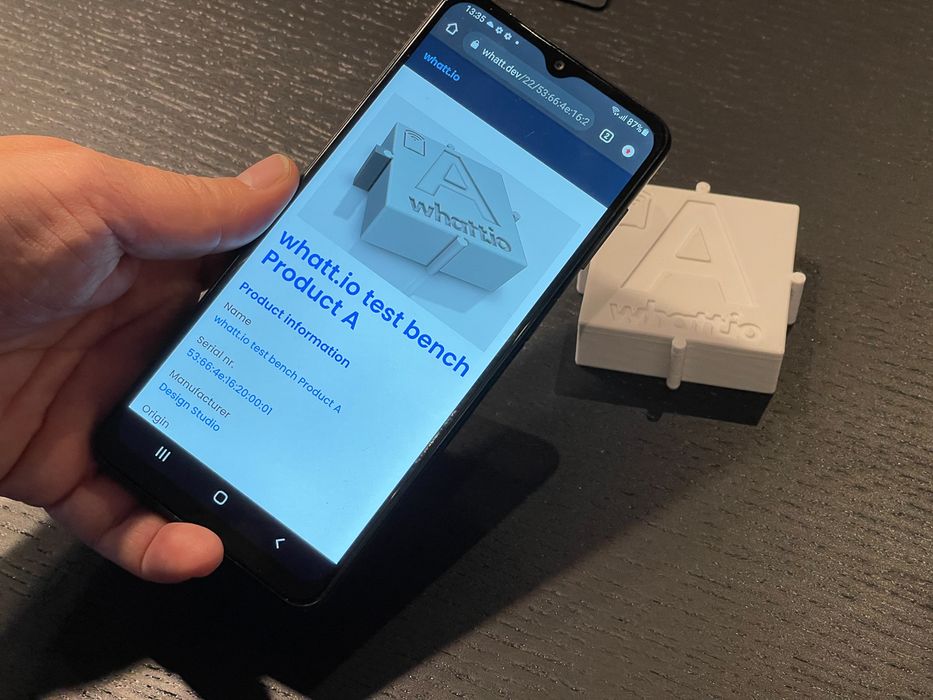
Use of the system is quite simple: an app on a mobile phone can drive the “reader” part of the system, and can receive the signals from the chip. The app would then display whatever information is relevant to the application.
For example, someone might want to know when the part was built, if it has an expected useful lifetime. Or, a spare part could be checked to ensure it is the correct version for a repair operation. Another use might be to identify the exact type of material used in the part during recycling.
There are countless ways this capability could be leveraged: a part identified is a better part.
Regarding the development program, Lostboyslab explained:
“The program will target 3D printing with FDM and FFF technology as these additive manufacturing techniques allow for integration of the NFC chip inside the material of the part. Participants in the program will be leaders in their industry with already or planned investment in FDM/FFF 3D printing to integrate traceability into their product information workflow.”
Lostboyslab expects the service would be of great value to 3D print farms, where parts are continually produced and require identification, as well as the ongoing machine repair activities. It might also be of interest to product designers that have complex collections of near-identical parts that require identification.
Lostboyslab is accepting applications for their development program. If you have some ideas about how this unusual capability could be used, you might want to check out their offer.
Via Lostboyslab