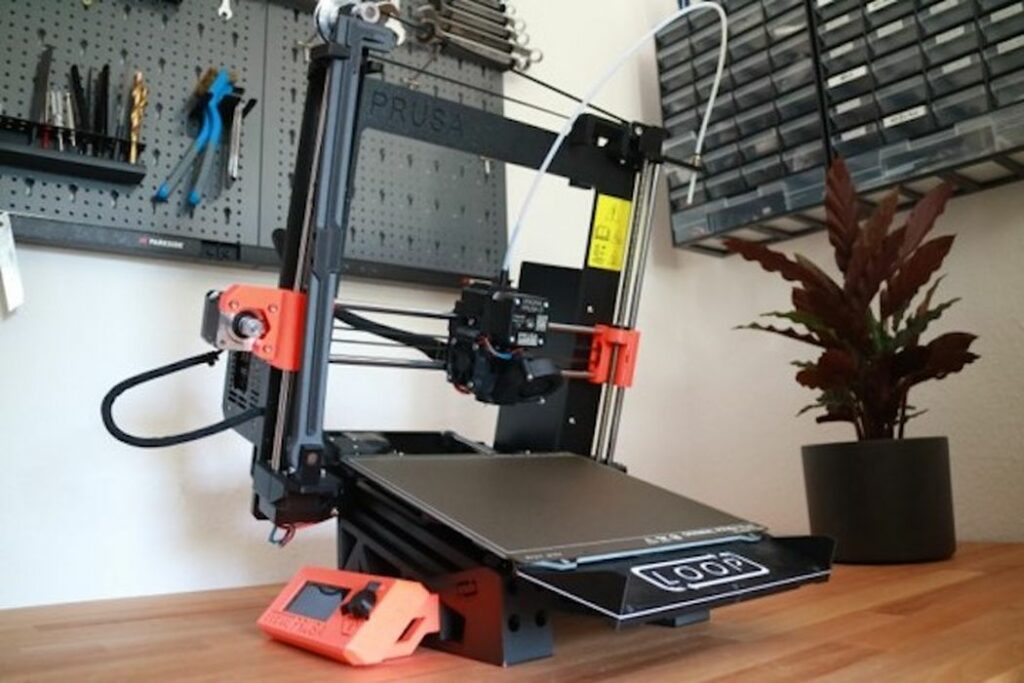
A new method of continuous 3D printing has been developed.
Freelance mechanical engineer Pierre Trappe has created a new open source project, “Loop”, which enables a Prusa MK3S+ 3D printer to operate continuously.
There have been multiple approaches to this problem attempted by startup companies on a series of different platforms. One of them was Loop 3D — ironically with a near-identical name — that used an unusual print bed that pushed off prints when done. Another is 3DQue, which apparently inspired Trappe to develop Loop.
Loop requires some modifications to the Prusa MK3S+ design, most notably to mount the 3D printer at a slight angle to help encourage removal of completed prints.
The approach used by Loop is to drop an arm onto the print plate after printing completes, and then move the plate’s Y-axis to cause the arm to push off everything off the print surface. Objects then fall down the slope, presumably into a catch basket. Note that because the arm takes up some space, the available build volume becomes slightly smaller.
Here’s how it looks in action:
Unlike the 3DQue approach, which replaces the print surface with a specially designed material that ensures reliable release, the Loop system re-uses the original Prusa MK3S+ print surface as-is. However, you have to properly clean the surface, have precise first layer adhesion temperatures and proper z-gap settings. You must also wait until the bed is less than 30C to proceed with the automated print removal.
Trappe has created an online document where operators can store their print parameters publicly, as there will be questions about how to print particular materials.
There are some special practices required. For example, if you use a skirt (a circular path around a print to ensure material is flowing properly), then it must be at least six layers tall. This is because the arm might miss it if it is any shorter. This also implies that Loop might not be able to handle very thin prints.
The arm is just an arm, it’s not a scraper.
If you look carefully in the video, you can see that Trappe’s design uses the X-axis motor to power the arm. There is an extra belt that transfers power to the lift and drop the arm, but the X-axis does move slightly during this procedure. This is a good way to avoid the requirement of an extra stepper motor in the design.
Special GCODE is added to the beginning and end of each print job to manage arm positioning and more.
The instructions to build the Loop are relatively straightforward, although you likely should have some experience building a 3D printer beforehand. Certainly there will be many who would feel this project is beyond their skills, but plenty who would find it interesting.
One thing to remember, however, is that continuous 3D printing requires not only removal of completed prints, but also repeated delivery of new print jobs. This is accomplished by Loop through the use of Octoprint. This software runs on a separate Raspberry Pi and can implement a print queue. Thus, when one job completes, a second can be launched automatically. In theory you should be able to come back to the printer and discover a basket full of parts.
Finally, this is an open source project. It’s entirely free to use, but you’ll have to provide the parts, tools and labor yourself.
This is a pretty interesting project and could be of interest to anyone handy with electronics and tools that has a Prusa MK3S+ available for modification.
Via GitHub