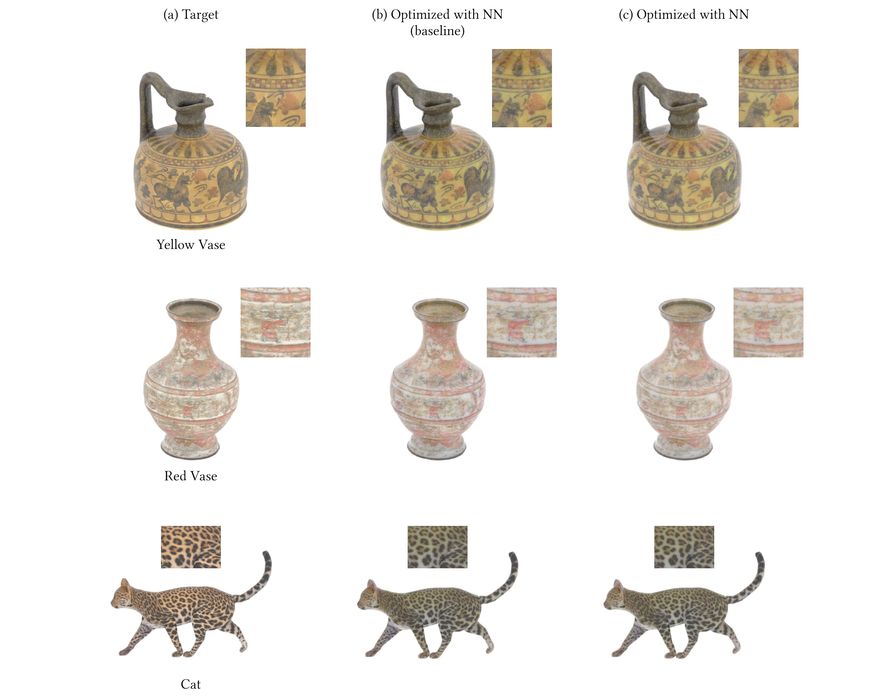
Researchers have developed a way for software to help improve the appearance of full-color 3D prints.
Full-color 3D printing is not a widespread technology, and only a few manufacturers offer this type of equipment these days. This is likely because there are relatively few applications as compared to general-purpose 3D printing, where mechanical parts abound.
The few applications that exist for full-color 3D printing tend to require the most accurate colors possible. This is because the applications are testing not the physical capabilities of a part, as is done with 3D printing of mechanical parts, but instead they’re testing the visual appeal of a full-color part.
In other words, the part has to appear the closest it possibly can to the production part’s visual appearance.
You’d think this would be straightforward with today’s most advanced full-color 3D printers. The most accurate colors are obtained these days from material jetting processes, such as used by Stratasys or Mimaki. The full-color prints made by these machines are truly astonishing, as they have vivid colors and perfectly transparent segments.
However, are these parts truly accurate in terms of color?
Both companies offer some form of color certification, like Pantone. But that’s not the entire story.
While a single voxel of the print might carry the correct Pantone color, there’s more at play. The color could bleed slightly into neighboring voxels. The opaqueness of the voxel might allow light to penetrate and reflect, again changing the visual appearance in a subtle manner.
Those faults might seem minor, but to color perfectionists — in other words the folks who typically use full-color 3D printing — they are a big deal.
Until now they haven’t truly been solved. However, that could change with the announcement of new research from the Faculty of Mathematics and Physics at Charles University in Prague. They’re explain the issue:
“Similar to 2D printing, a wide range of color shades are produced by placing multiple base materials (CMYK+W) next to each other. The materials consist of a semi-transparent resin that allows for light to travel slightly below the surface. This translucency enables precise subtractive mixing of color shades through different ratios of absorbing base materials.
Despite the flexibility in color reproduction, the color-bleeding also poses a physical limitation for the reproduction of fine detail: Texture details are blurred and hard edges lose contrast from the light scattering laterally underneath the surface. Adding to this problem, the blur is three-dimensional meaning that it also affects colors on opposing sides of thin object parts.”
They’ve been able to develop a sophisticated software system that can through simulation determine with high accuracy the color and light properties of a proposed full-color 3D print.
The simulation uses a neural network trained on countless lighting examples and runs 300X faster than previous simulations on GPU hardware. A simulation can thus take place in only a few minutes.
The idea is to use the simulation to “see what you’ll get” before you commit to 3D printing. This allows the 3D printer operator to tweak settings to iteratively find the optimal solution. They explain:
“The team’s previous work has proven that it is possible to recover the sharpness and contrast by carefully optimizing the material placement. Using a virtual simulation of the printed appearance one can iteratively find an arrangement of materials that reproduces the input object most faithfully.”
The project’s code has been released in open source format here. Because this is open source, it is possible this approach might be quickly incorporated into control software provided by full color 3D printer manufacturers.
We might be seeing even more realistic 3D prints in the near future.