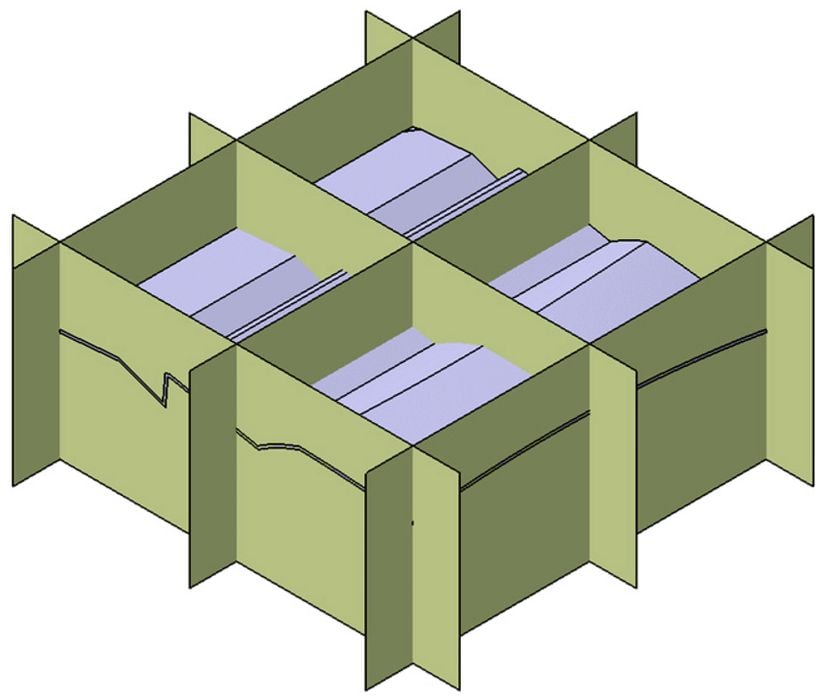
A paper released last month describes an efficient method for splitting 3D models, enabling 3D printing of large objects on smaller machines.
Researchers at Technische Universität München considered the problem of small build volumes in most contemporary 3D printers, and that many parts cannot fit within them.
I always say the build volume doesn’t matter so much because 3D models can always be segmented into different parts that do fit within the build volume. Print and assemble, that’s how you get large objects made.
But how, exactly, do you segment a 3D model into different parts? You could simply do a series of manual plane cuts, but then you have the issue of part alignment during assembly: how do you make certain the parts are in precisely the correct location? You would then have to create holes and pins, but then the whole process becomes massive if there are more than a few segments involved.
The only software I’ve seen that’s able to do something like this is LuBan, a little-known 3D print utility program that, among many other features, can assist in the segmentation process. However, very few people use it due to a US$400 license fee. That’s more cash than the cost of some very good 3D printers these days!
There’s more trouble when segmenting: you want the assembled structure to have sufficient strength for its intended purpose. For example, you wouldn’t want your spindly 3 meter sculpture to collapse because the segments were not engineered to be in the optimal locations, would you?
What if you happened to segment a 3D model in such a way that you could not actually assemble it after printing because the pin directions conflict?
The more you think about it, the more complex this problem becomes. Now imagine trying to automate it with a software algorithm.
That’s the problem space of this research. The paper describes their approach:
“This paper presents a universal design method to overcome this limitation while preserving the economic advantages of rapid prototyping over conventional processes. It segments large, thin-walled parts and joins the segments. The method aims to produce an assembly with minimal loss to the performance and characteristics of a solid part. Based on a set of requirements, a universal segmentation approach and a novel hybrid joint design combining adhesive bonding and press fitting are developed. This design allows for the force transmission, positioning, and assembly of the segments adaptive to their individual geometry.”
In other words, INTELLIGENT segmentation, something that doesn’t exist on the market today.
You can immediately see their approach is different because it recognizes six different methods of joining parts together, including: compounding, pressing, forming, shaping, welding, and gluing. The overall problem is related to puzzle theory, as they explain:
“The challenges of segmentation are related to those of a puzzle game, except that it poses a three-dimensional instead of a two-dimensional problem. This increases the complexity and relativizes questions regarding the uniform design and assembly of three-dimensional segments.”
Their approach is quite complex and you’ll have to read the paper to see the details, but the implications of it are profound.
This system allows a large object to be segmented in a way that allows for practical and effective assembly after printing. No other system known does this.
Imagine if one of the 3D printer manufacturers put this algorithm into their slicing software. That would change how desktop 3D printers are used in a very direct way. This could be a typical workflow:
- Design very large object, ignoring build volume constraints
- Segment the 3D model in the slicing software to fit piece within the build model
- Slice all the pieces and generate separate GCODE files for each
- Successively print each GCODE file
- Assemble the prints
The first point is the most important: Ignore The Build Volume. This is something that has never, ever been heard in the 3D Printing Universe.
Software developers of Ultimaker Cura, PrusaSlicer, Simplify3D, IdeaMaker and others: are you ready to take this on?
Via Research Gate