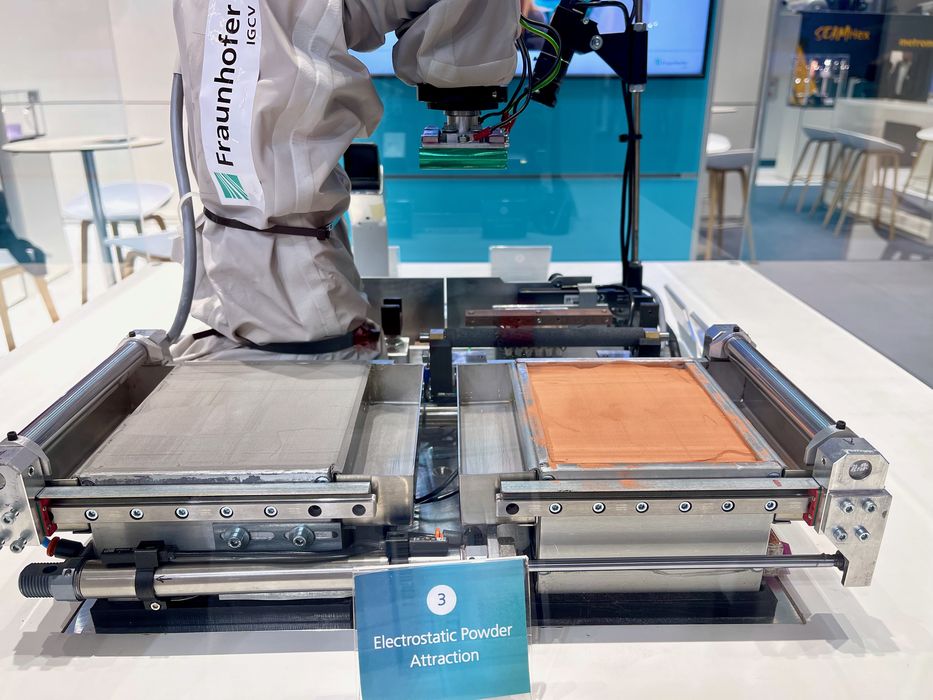
One of the most interesting technologies we observed at Formnext 2022 was a new way to 3D print multiple materials in powder.
Powder 3D printing isn’t new; it’s been around for decades and has evolved into many forms. However, there is one persistent attribute of powder-based 3D printing: only one type of powder is used.
This is true whether it’s metal or thermoplastic powder. The recoating system that places a fresh layer of powder on the bed for fusion almost always lays one material down. Typically, this is done with a blade the bulldozes a pile of powder across.
There is one technology on the market today that allows use of multiple powders in a 3D printing system. Aerosint, now part of the growing Desktop Metal empire, uses a sequence of metal drums to grab different powders and deposit them on the print surface.
However, Aerosint doesn’t make a 3D printer that does this. Instead they produce the recoating system that can be integrated into another party’s 3D printer, which has been done with Aconity.
At Formnext 2022 we spoke with Fraunhofer IGCV’s Julia Förster MSc, whose PhD thesis involves a new method of performing multi-material powder 3D printing. It’s somewhat reminiscent of Aerosint’s approach, but quite different and potentially much more scalable.
Förster’s approach — which at this point doesn’t have a brand name, it’s a PhD thesis — involves electrostatic forces.
The idea is to have a plate that is selectively charged through an imaging process. Basically, you project a pattern on the plate, leaving the illuminated portions charged.
The selectively charged plate then is dipped in a powder reservoir, where the statically-charged areas pick up some powder. A robot arm moves the plate over the print surface and aligns its position. The powder bed just happens to hold the opposite charge, which causes the powder to drop on to appropriate positions on the print surface.
The empty plate can then be re-charged with another image and then pick up more powder. But get this — the next powder could be from a different reservoir with a different powder.
This process can repeat with as many images and powders as you can reach with the robot arm.
Förster explained that the system is suitable for use in typical AM equipment conditions: cramped space, high temperatures, smoke & spatter, etc.
The robotic motion system can be quite accurate, with a positioning accuracy of less than 0.1mm, which should be sufficient for almost all applications.
Most interestingly, this electrostatic recoating system can be used for not only metal powders, but also for ceramics and thermoplastic powders with diameters between 0.02-0.06mm, non-flowable powders with larger diameters and it even works with non-spherical powders.
One could imagine a 3D printer equipped with this system along with an automated set of powder trays. This could enable multi-material 3D printing with perhaps dozens of different materials in the same powder print job.
This system, if integrated into a 3D printer, could produce multi-material powder-based objects. However, I do have one concern. The speed of a powder 3D printer is largely related to the speed of recoating. Many powder-based 3D printer manufacturers have taken various steps to reduce the recoat time, by recoating from both sides, for example.
The electrostatic approach could be quite time consuming. Imagine a complex 3D print with four different powders. Recoating a layer would require four separate imaging, collecting and deposition sequences. That could take considerable time to execute, leading to longer print times.
But you’ll get amazing 3D objects made from multiple materials.
Via Fraunhofer IGCV