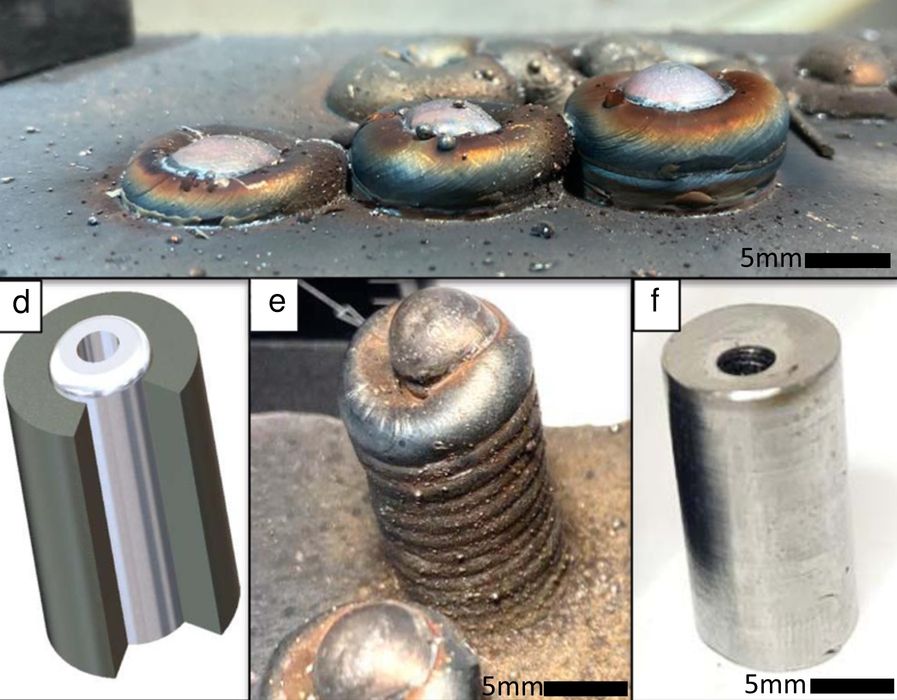
New research has developed an unusual and inexpensive way to dramatically strengthen metal 3D prints using a bimetallic radial approach.
Strong metal parts are always in demand, and not just for the strength: if a material can be stronger, you can use less of it to accomplish the same function. This is critically important in aerospace and automotive applications.
Most approaches to strengthen metals has been in the chemistry of the alloy. Mix in a bit of this and a bit of that, and voila, you have a slightly stronger resulting metal alloy.
The approach done by the researchers at Washington State University have taken a different approach: bimetallic, and they’ve done so in a very curious manner.
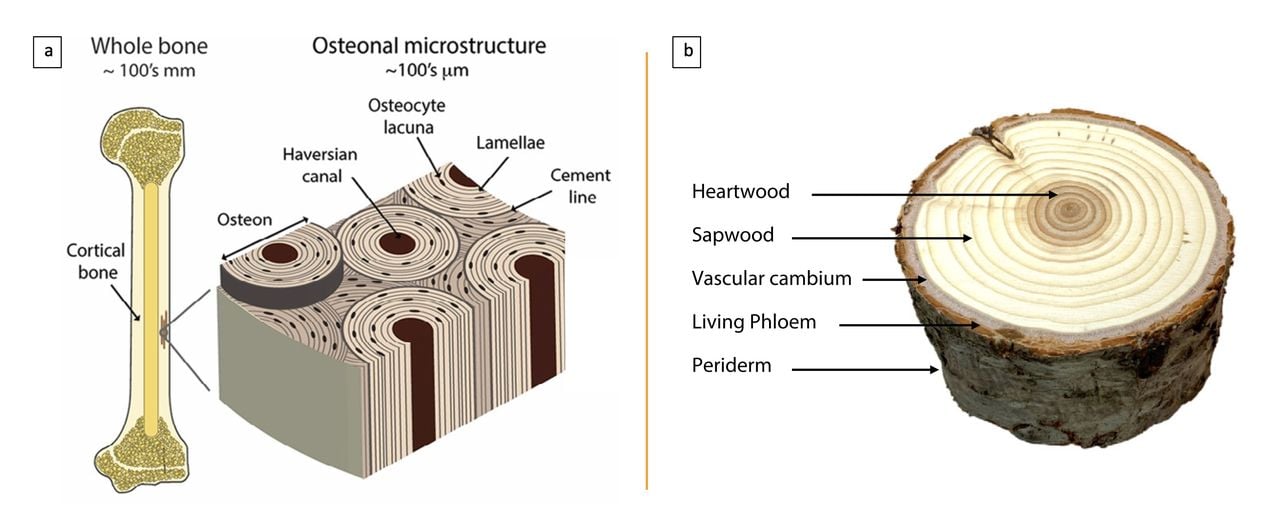
They took a strong cue from nature, where radial patterns are often used to create strong structures. For example, consider a typical tree: a cross section would show several layers of different properties arranged in a radial pattern.
Trees are not the end of this approach, either: your own bones use the same technique. It turns out to be a very common approach in the biological world, yet is rarely seen in engineering and certainly in additive manufacturing.
The experiment performed by the researchers involved printing objects with this type of internal structure. They chose to use two different steels: stainless steel and mild steel.
To 3D print objects, they developed a unique dual DED 3D printer that used one metal on each printhead. Software drove the dual system to print in the desired geometry, with one metal being used as the casing, and the other the core.
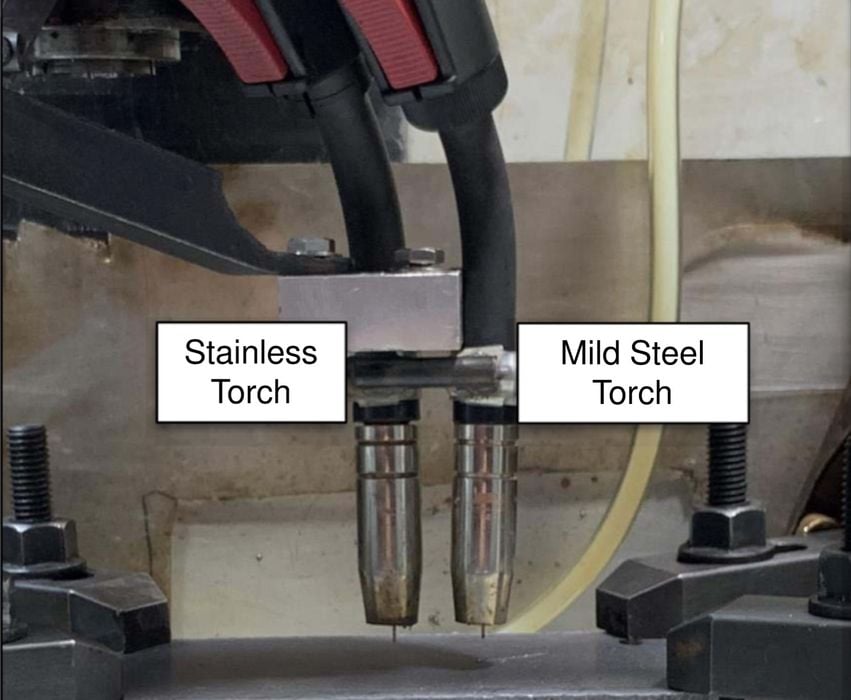
The completed metal prints were then subjected to standard tests, and the results were quite startling. Compression testing revealed a 33% relative increase in strength for radial bimetallic specimens over monolithic mild steel and a 42% relative increase in strength over monolithic stainless steel.
That is very significant, and an investigation of why this happened took place.
It turns out that the two metals have very slightly different cooling profiles. Here we have a “bimetal cooling” scenario, where the two metals are in contact during cooling, which produces some mechanical stress.
These forces remain in place after printing and cooling, and apparently creates a residual stress effect that resists crack propagation. That’s why it takes more energy to break these prints.
Even better, the implementation of this approach seems quite straightforward: add another toolhead and change up your tool paths. This could easily be set up by any of several existing DED equipment manufacturers, so it’s possible we could see this solution in the field soon — assuming licensing is worked out.
There’s one more twist to this: if this works for metal, could it also work for polymers? If it works with metal — and bone calcium & tree wood, it likely works with plastics, too.
Via Nature