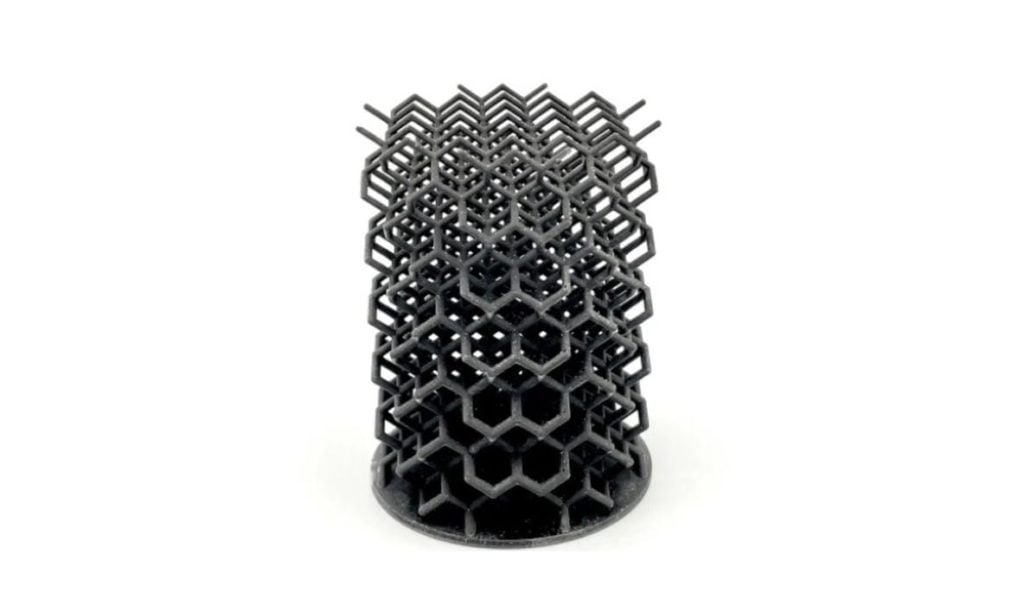
Materials companies have been hard at work developing improved resins for 3D printing, creating new opportunities across industries.
Resin-based 3D printing has long been known for its benefits. Along with better resolution and faster printing, using resins results in strong, functional parts. Historically, those pluses came with some negatives, including higher costs, potential safety concerns, complex post-processing, inability for composite printing and lack of availability. This past year has seen a surge in materials companies taking on those negatives to make resins a more viable option across industries.
A Busy Year for Tethon 3D
Founded in 2014, Tethon 3D, based in Omaha, Neb., has steadily been on the forefront of developing new ceramic resins. In December 2020, the company launched three UV-curable resins. Used with the Bison 1000 DLP printer, Graphenite, Cordierite and Mullite resins are ideal for geometrically complex parts, including those for industrial uses. Graphenite, based on graphene, makes one of the strongest materials now a viable 3D printing option. Lightweight and conductive, it was once a challenging material to use with 3D printers. Tethon 3D met that challenge with its resin, which adds mechanical strength, can increase energy storage in batteries, and is anti-corrosive and scratch resistant. The ceramic-based Cordierite and Mullite are ideal for parts needing a high thermal shock tolerance, low thermal expansion and chemical stability.
Continuing its focus on innovation, Tethon 3D has been working with Mechnano Mech T to create high-temperature-resistant carbon nanotube material, C-Lite, which can be used with stereolithography (SLA), digital light processing (DLP) and liquid crystal display (LCD) additive manufacturing printers. C-Lite resin is ideal for parts at risk of electrostatic discharge, such as electronic manufacturing, automotive and defense, and can withstand temperatures up to 225°C.
Tethon 3D also recently partnered with Boston-based Fortify, which developed the Digital Composite Manufacturing (DCM) 3D printing platform. The two companies have developed two ceramic resins for high-volume production for multiple industries. At the September 2021 RAPID + TCT event in Chicago, the companies revealed Fortify High Purity Alumina (HP-A 99.8) and Low Shrink Aluminum Silicate (LS-AS). HP-A 99.8, an alumina-filled photoresin, reduces sintering shrinkage by 12 percent, while LS-AS is a general-use ceramic with 5 percent shrinkage.
Advances in Medical, Dental Materials
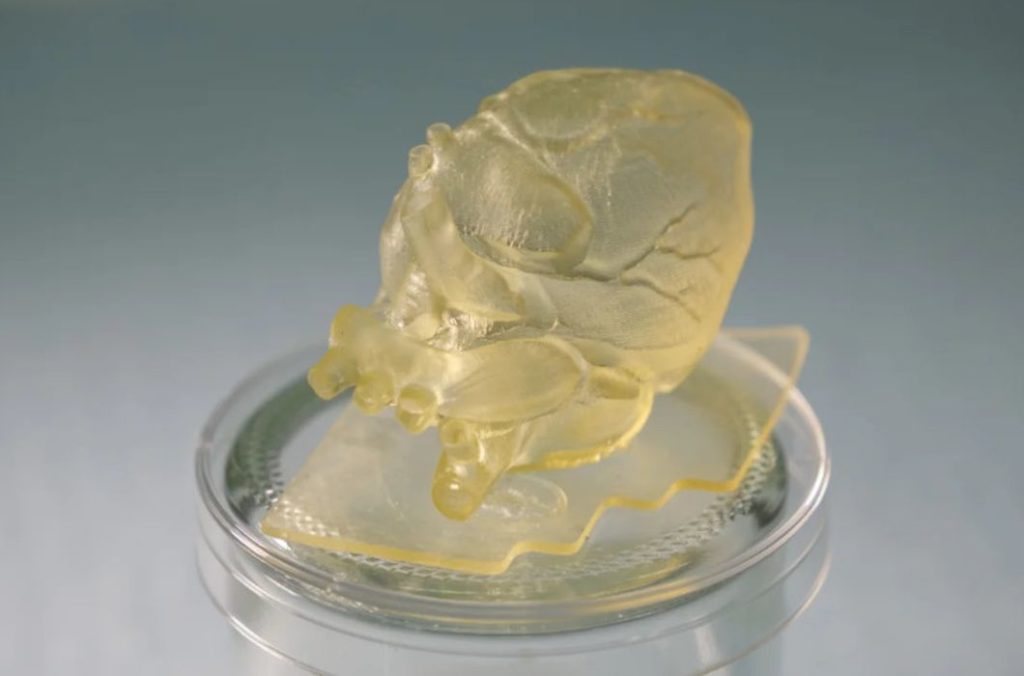
With 3D printing in the health care market set to have a 20.10 percent compound annual growth rate by 2030 —potentially reaching $5,846.74 million—materials developers, both businesses and research organizations, are steadily keeping up the pace with new innovations from optical to medical and dental.
The Commonwealth Scientific and Industrial Research Organization ( CSIRO ) has developed silicone resins suitable for 3D printing medical parts. Most current silicone resins come with challenges, including low resolution and speed, as well as require specialized printers. The CSIRO team has focused on solving those issues with a new family of silicone products, which can be used with off-the-shelf DLP printers. Designed to be biocompatible, the resins are non-cytotoxic and highly transparent. They feature tunable mechanical properties and allow for creating high-resolution designs that are complex, such as thin walls, hollow structures or irregular shapes. The finished parts are soft and have compressive elasticity. The resin can also affix glass and metal, making it an innovative construction adhesive. This allows for customizability from printing hearing aids to prosthetics and other devices. While the resin was designed for DLP printers, work continues to modify it for SLA printers.
When it comes to optical options, UpNano has launched two new resins that clear the black and clear barrier—the need for both absorptive and translucent components—once a significant challenge for optical assemblies. Created to work with the company’s NanoOne 3D printer, UpBlack and UpOpto are photopolymer materials that allow for printing non-transmitting black and translucent parts, respectively. The NanoOne uses 2-photon polymerization printing technology to produce parts with nano- or micrometer resolutions.
The dental industry has long been a leader in adopting 3D printing technologies. Along with Desktop Health launching two new materials, other key developers are making strides in resin availability. SprintRay, a leader in digital dentistry, developed a NightGuard Flex resin. Approved by the FDA, the resin enables the creation of flexible nightguards, mouthguards and splints.
Liqcreate, which is known for its array of resins from general purpose to creative purposes, recently launched Liqcreate Gingiva Mask, a dental-oriented photopolymer resin suitable for use in various dental applications. The pink photopolymer is flexible and soft, making it ideal for models, bridges, gum parts, soft tissue and implants. It can be made with masked stereolithography (MSLA), SLA, LCD or DLP printers with a range of 385 to 420 nanometers.
Read more at ENGINEERING.com