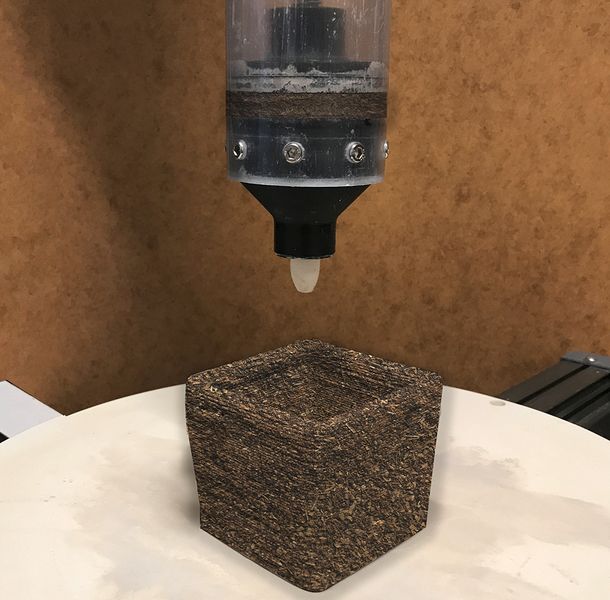
Researchers have developed a unique and eco-friendly material for 3D printing: fungus!
You’ve likely heard of all manner of crazy materials being used for 3D printing, including coffee, bamboo, algae, but these novelty products have mostly been shifted aside to make room for true engineering materials. This change strongly aligns with the 3D print market shift from targeting consumers to targeting professionals.
So why would we have fungus as a 3D print material? And especially have it produced by the prestigious Fraunhofer Institute in Germany?
It turns out there is a very valid reason for doing so, one that will certainly fit into today’s professional 3D printing market.
Soundproofing Rooms
The researchers were focused on materials for soundproofing.
Soundproofing is an essential element of modern offices and residences, although it’s often overlooked. That attitude changes when one is forced to work in a glass office, where sounds echo endlessly off walls, usually driving the inhabitant insane.
The remedy is to install soundproofing panels on the walls and ceilings. In many offices the combination of carpet and ceiling tiles is sufficient to bring down the echoes, but in some cases it’s necessary to put purpose-built soundproofing panels on walls.
These panels are designed with porous materials that are especially good at trapping sound vibrations. However, they are also typically made from unsustainable materials and are not always recyclable.
3D Printed Fungus For Sound Absorption
That scenario provides an opening for a new solution. Here the researchers decided to investigate the possibility of using fungus material as a soundproofing agent, as fungus has complex structures that might absorb sound.
Fraunhofer explains:
“Mycelium consists of a fine network of filament-like hyphae. In its natural habitat, mycelium grows underground, where it may span more than a square kilometer.”
But how could one 3D print this material? It doesn’t seem to be something that could be made into a filament, and there’s also the problem that it is a living organism that will grow. No one has to worry about 3D prints “growing” after printing, where they might require trimming.
The researchers grew mycelium in the lab and then mixed with a combination of “straw, wood and waste from food production”, to create an entirely organic composite material. This was then 3D printed.
They don’t explicitly say how the material was 3D printed, but it’s evident from their press image that it was extruded using a paste cylinder. This is similar to how ceramics are typically 3D printed, so that part of the experiment was well understood.
Using this setup, they were able to 3D print sound-stopping objects in arbitrary geometries. They demonstrated that due to the complex nature of the mycelium, the thickness required was substantially smaller than that normally used in commercial sound proofing panels.
But will these objects continue to grow? No, they won’t, due to a heat treatment after 3D printing. This heat kills the fungus and dries the entire structure to a rigid and permanent form.
Future Fungus 3D Print Applications
If this process can be commercialized, we could see some very intriguing products.
Soundproofing is a bit of a science, as it’s not simply a matter of pasting up some panels on a wall. The optimal solution is to perform an audio analysis of the room to determine where soundproofing should be applied, how much should be applied, and what kind of soundproofing should be applied.
I don’t know about you, but that sounds to me like a custom-developed solution, and that happens to be the sweet spot for 3D printed objects. It’s easy to create one-off products using 3D printing, but very hard for traditional mass production techniques.
I could see an advanced audio software analysis system literally generate custom 3D models for a sound proofing job. Custom fungal prints would then be applied to strategic surfaces in the target room to provide the best possible sound.
There’s a couple of reasons this could be successful: first, the ability to customize the product might result in fewer solution pieces for a given space, whereas the traditional approach might require plastering the walls with too many panels. Secondly, the cost of a customized solution might be less than traditional approaches simply because there are fewer bits to the solution.
I’m quite interested to see where this goes.
Via Fraunhofer