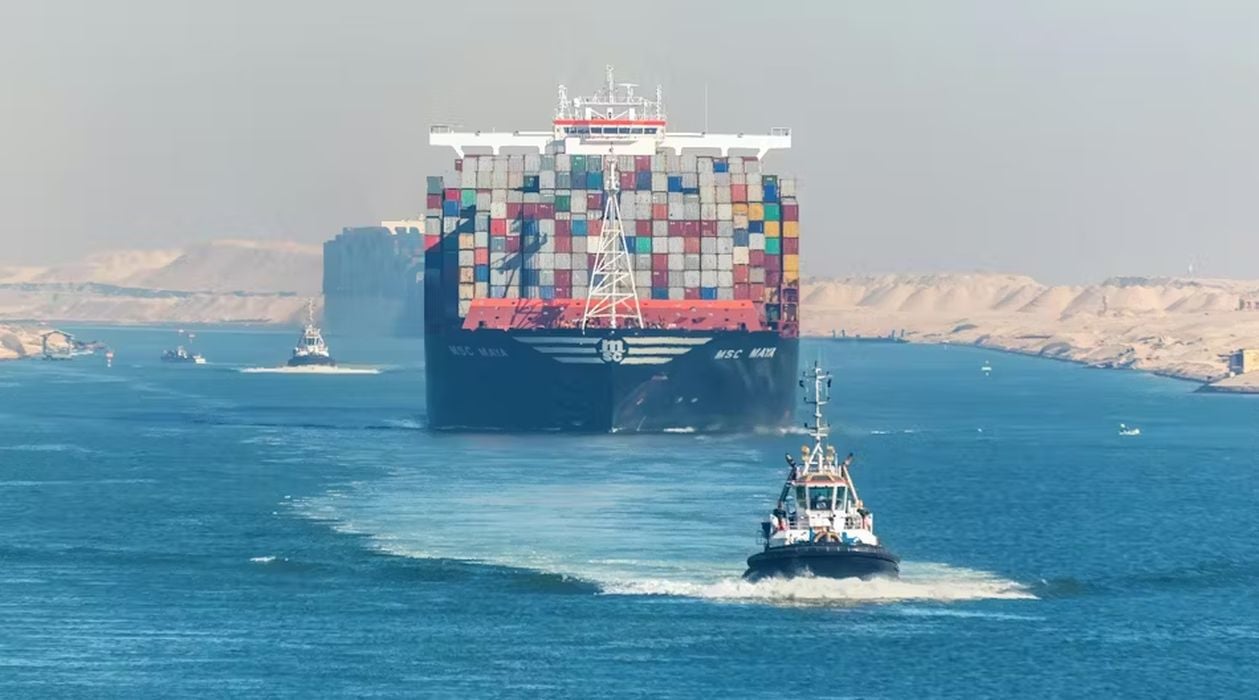
Charles R. Goulding and Preeti Sulibhavi consider 3D printing as a potential solution amid ongoing global supply chain disruptions.
Supply chain disruptions have become an unfortunate reality in recent years. As a result, supply chain planning experts at leading companies continuously model alternative scenarios to mitigate risk. The recent Houthi rebel attacks on ships in the Red Sea are the latest challenge forcing companies to explore options.
In normal times, supply chain planners model standard trade cost inputs like product pricing, freight, insurance, duties, taxes and delivery times. With the Red Sea instability, companies must weigh additional alternatives.
Traversing the Red Sea
One option is traversing the Red Sea despite the attacks. Companies would factor in the liability, pay war risk insurance premiums if available, and account for potential delays. Given recent events like the attack on a Russian oil tanker, the probability of an incident seems high. Still, some ships continue crossing by implementing security measures. Companies will have to decide if the potential savings outweigh the risks.
Using Alternate Carriers
Rather than using Western carriers, companies could book shipments through Chinese or other carriers theoretically less prone to attacks. However, immunity cannot be guaranteed as evidenced by the aforementioned Russian tanker incident. If tensions rise, these carriers would likely face similar risks. Nonetheless, some companies may accept the uncertainty to avoid longer routes.
Going Around Africa
Circumnavigating Africa adds over 3,000 miles versus traversing the Suez Canal. Apart from significantly higher fuel costs, the longer journey ties up ships and containers longer. Industry estimates suggest an around Africa routing costs between US$300,000 to US$400,000 more per voyage. Supply chains would experience over 45 days longer transits if ships sail around Africa. For time-sensitive goods like electronics and perishables, companies will avoid this option if feasible.
Air Freight
While faster, air freight costs on average over five times more than ocean shipping. Air makes economic sense mostly for small, lightweight, high-value items. However, capacity constraints especially out of Asia may limit air shipping’s viability currently. Congestion at European hubs compounds the situation. Still, some companies may use air selectively until maritime risks subside.
Sourcing Closer to Demand
For companies selling regionally, sourcing finished goods from geographies not reliant on the Suez Canal is an option. However, reorienting supply chains takes significant effort and may not work for industries lacking regional suppliers. If companies can find capable nearby vendors, shorter supply lines could offset somewhat higher local costs.
Insource Production and Utilize 3D Printing Resources
When faced with supply uncertainty, manufacturers often consider insourcing production using internal capacity or contracted providers. Relative to ocean freight, this shortens and simplifies the supply chain. Technologies like 3D printing and automation enable economically inhousing small volume production.
While many associate 3D printing with prototypes, materials and equipment improvements now facilitate short run production. 3D printing shines where customization matters more than scale economics. As printers and materials advance, more applications suit 3D production. The pandemic showed 3D’s potential by enabling agile production of spare parts otherwise hindered by shutdowns.
Wilhelmsen and the Ivaldi Group
Wilhelmsen partnered with Ivaldi Group in 2017 to disrupt the supply chain for marine parts by replacing the traditional supply chain process with a customized, on-demand, and more efficient process of 3D printing. Their early adopters include Carnival, Thome Group, OSM Maritime Group, Executive Ship Management and Berge Bulk.
From local micro-factories, Wilhelmsen 3D prints and delivers spare parts within hours, lowering the carbon footprint and reducing costs.
The Green Ship of the Future Consortium
Funded by the Danish Maritime Fund, the “Green Ship of the Future Consortium” is an independent nonprofit organization driven and funded by its members. They’re working towards emission-free maritime transport using new technologies and innovation.
With partners that include Maersk, MAN Diesel & Turbo, DNV GL, one of their projects explored 3D printing in the maritime industry, including on-board printing, large-scale 3D printing, 4D printing or repair, and reconditioning with 3D printing.
The Research & Development Tax Credit
The now permanent Research and Development (R&D) Tax Credit is available for companies developing new or improved products, processes and/or software.
3D printing can help boost a company’s R&D Tax Credits. Wages for technical employees creating, testing and revising 3D printed prototypes can be included as a percentage of eligible time spent for the R&D Tax Credit. Similarly, when used as a method of improving a process, time spent integrating 3D printing hardware and software counts as an eligible activity. Lastly, when used for modeling and preproduction, the costs of filaments consumed during the development process may also be recovered.
Whether it is used for creating and testing prototypes or for final production, 3D printing is a great indicator that R&D Credit eligible activities are taking place. Companies implementing this technology at any point should consider taking advantage of R&D Tax Credits.
Conclusion
For companies struggling with supply chain turbulence, relying solely on traditional shipping has risks. Widening the perspective to include technology-influenced options like 3D printing merits consideration. The analysis may reveal insourcing production using 3D printing and automation favors over importing for some goods.
Business leaders should challenge teams to explore 3D printing’s potentials as one problem-solving tool when supply chains falter. With innovative thinking, companies can turn supply risks into opportunities.