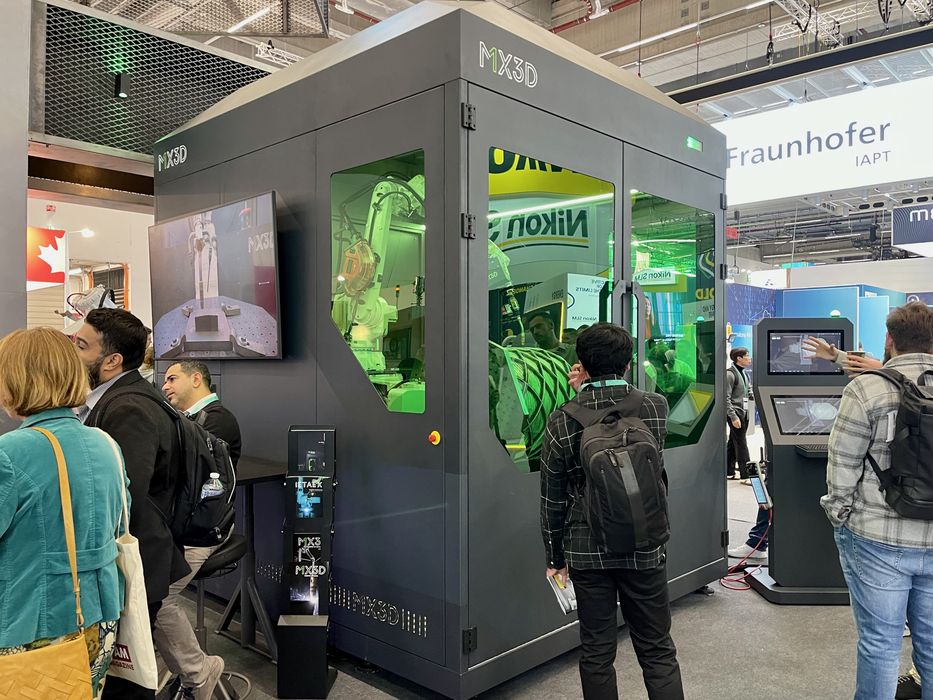
MX3D is making considerable progress with their latest product, the M1 METAL AM SYSTEM.
MX3D is a Netherlands-based company that started some years ago developing a wire-arc additive manufacturing system (WAAM). This technology involves feeding welding wire through an electrical arc at the end of a robotic arm. The arm moves and deposits metal to build up a 3D object.
Years ago their product was basically a robot arm and the toolhead, but these days their products are far more sophisticated. Their product line includes two turnkey METAL AM SYSTEMS that include all the necessary hardware and software to print large metal objects.
We had a look at the “mini” version of the two, the M1. As you can see in the top image, it’s quite large, but smaller than its enormous sibling, the MX.
Company representatives told us they have “sold quite a few” of these units. When asked what customers might be building with them, it turns out a popular application is the production of large metal pressure vessels. These can weigh typically 62kg, and are made from an aluminum alloy.
But MX3D’s current offering isn’t just hardware. The company has completed considerable software development as well, making these AM units much more practical in workshop environments.
Not only can metal 3D objects be created, but it’s also possible to weld on top of existing metal objects: the system can follow the curves of an object. This feature can also be used to repair metal objects in a fully automated manner.
One interesting feature is a “24/7 package”, which enables automatic changing of tips and other automations. With this optional feature operators are able to run the device literally all day long, enabling night shift 3D printing.
The system can also include an integrated scanner for quality control, and this is patched into the software that runs the M1, MetalXL.
MetalXL is able to control the robotic arms directly and is specially written to work robotic arms for additive manufacturing in an easy fashion. MX3D writes:
“Its streamlined end-to-end workflow allows users to easily manage the printing process from design to print. MetalXL is WAAM-dedicaztd, hardware independent and allows 3D metal printing at substantially lower CAPEX and OPEX.”
They say they’ve made a number of sales, including to the US Army and to a Swiss research firm. They also make use of the equipment in their own facilities, which makes them intimately aware of any issues that might require improvement.
Today the company has around 30 staff, and it sounds like they will be growing more in the future.
I did ask them about the famous 3D printed bridge in Amsterdam, which was recently removed. This structure was the first 3D printed bridge on the planet, and it made quite a few headlines when it was installed.
Unfortunately it turned out that MX3D had a permit for only two years, as the city wishes to maintain its historical character. It might have been possible to extend the permit, but apparently that would have been difficult to obtain as it requires local citizen input. Instead they’re hoping the bridge ends up in a museum to show everyone the world’s first 3D printed bridge.
Via MX3D