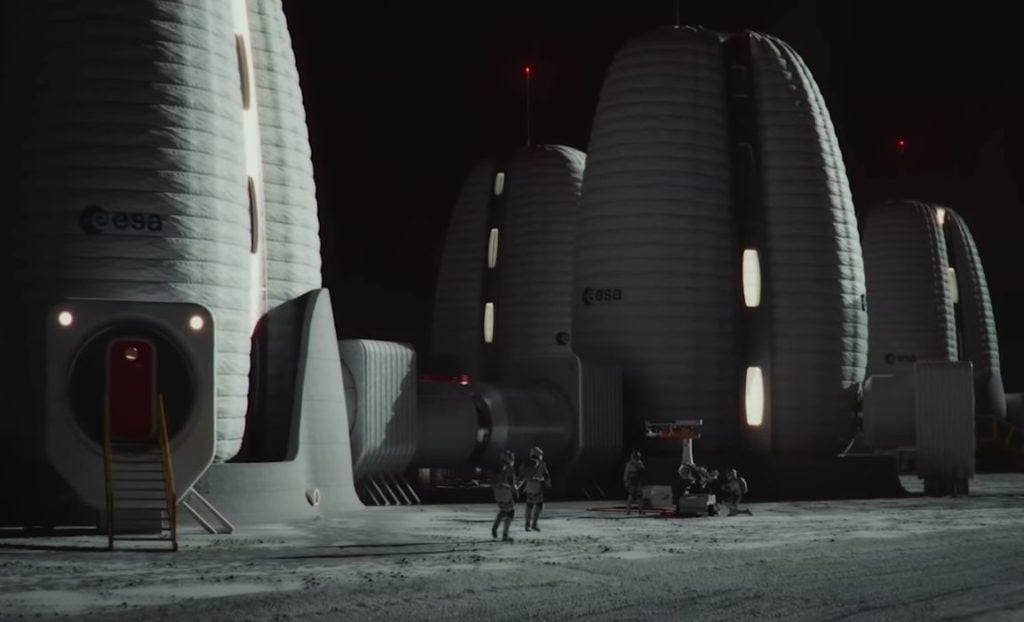
MX3D has 3D printed a prototype metal lunar habitat floor for ESA.
The work was part of a project to develop a conceptual lunar habitat, undertaken by designers Skidmore, Owings & Merrill, as advised by former US astronauts. The concept involves an inflatable structure placed on the Moon near the South Pole where it would receive continuous sunlight all day, every day.
EAS has published an inspirational video describing the habitat concept:
MX3D’s WAAM
MX3D is a Netherlands-based company that specializes in WAAM — Wire Arc Additive Manufacturing. WAAM involves pushing a metal wire to a toolhead, where it is instantly melted by an electrical arc. The “melt” is then added to a structure that grows as the toolhead is moved. MX3D uses a robotic arm system as the motion system in their WAAM implementation.
Previously, the company has produced a number of unusual metal 3D printed prototypes. Perhaps the most notable project is their temporary 3D printed metal bridge in Amsterdam, which gathered considerable media attention.
The company has also raised a significant amount of cash from new investors earlier this year, positioning them for expansion and further product development.
Life Beyond Earth Project
The latest project for MX3D is for ESA, where they are exhibiting a four-floor lunar habitat concept called “Life Beyond Earth” at the 17th International Architecture Exhibition of La Biennale di Venezia.
SOM Senior Designer Daniel Inocente said:
“’Life Beyond Earth’ represents a paradigm shift in space architecture and offers insights discovered through international cross-sector cooperation. The challenges confronted here inspired new solutions and enabled us to envision a future for humanity beyond Earth.”
MX3D’s role was to 3D print the metal base for the habitat. Six sections were 3D printed, and then manually welded together to form the final armature. MX3D used 308LSi stainless steel for the print, and the 395kg of total material required a whopping 246 hours of 3D printing to complete.
Here you can see the massive 4.5m diameter skeletal structure they produced:
This armature will be based on three support columns, and provide a base for a number of floor panels.
MX3D CEO Gijs van der Velden explained:
“This was a great opportunity to show the potential of our technology for the fabrication of lightweight metal structures together with ESA and SOM. It was a perfect project for MX3D to leverage its experience in printing topology optimised metal structures. Achieving an optimal use of material is a company goal at MX3D because – just as when designing space applications – every reduced kilo in a MX3D design is a direct win for a project’s feasibility.”
The concept, if transformed into reality, could offer a way for lunar explorers to locally produce this and other key elements of a lunar habitat without having to make room on cargo ships to carry the huge structure. By sending a 3D printer and materials for it, the objects could be produced on site.
This project was simply a demonstration, however, and it is highly unlikely MX3D’s technology — as is — could be used in a lunar environment. Their robotic system is almost certainly not certified for use in a vacuum, with temperatures ranging from +127C to -173C and gritty particles constantly fouling any mechanism they encounter. To use MX3D’s WAAM on the lunar surface would undoubtedly require a significant redesign of their delivery system.