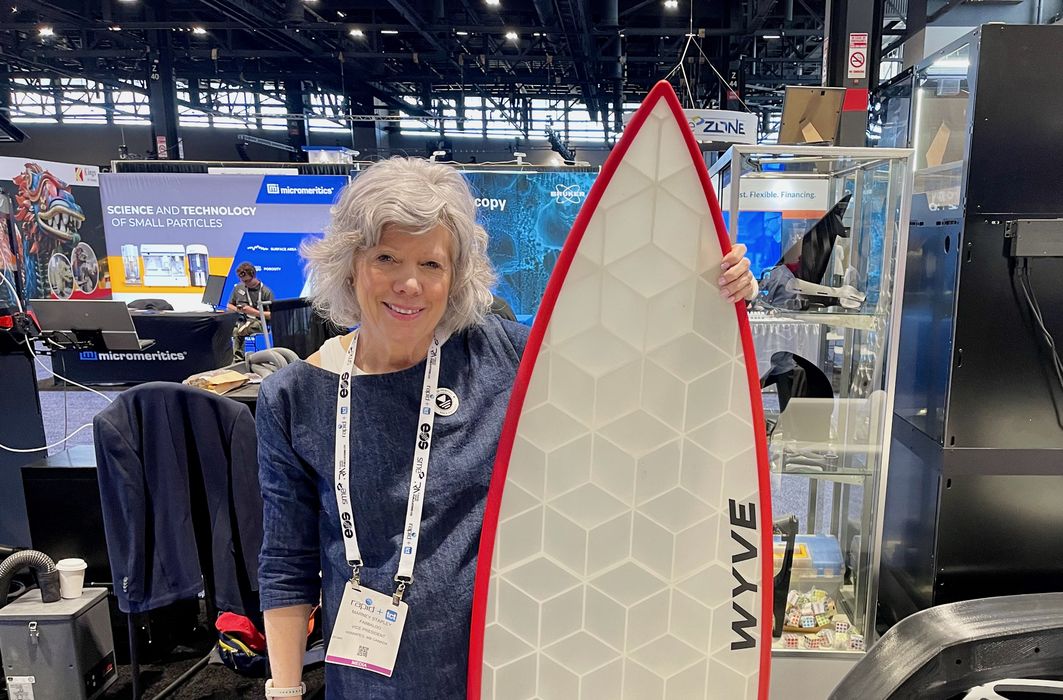
Modix has developed an intriguing strategy to connect with 3D printer buyers.
The company has been producing large-format FFF devices for many years, and we’ve covered several of their machines in the past. Their largest current device is the BIG-180X, which happens to have a massive build volume of 1800 x 600 x 600, one of the largest FFF devices on the market.
Recently the company released a new CoreXY design with their recent CORE-60, which suggests the company could switch to that style for more devices. The CoreXY motion system is compatible with high speed printing firmware, which would be highly desirable for large-format print jobs.
Like every 3D printer manufacturer, Modix must find ways to persuade customers to purchase their products. Some companies do so by touting their machine specifications. Others do so by lowering their price points. Modix is taking a different approach by appealing to the application needs of users.
An example of which is shown at top. The large item is in fact a custom surfboard. If you’re not aware, surfboards can be quite complex with a number of different dimensional parameters. It’s possible to design a custom surfboard for an individual that would best fit their surfing style and body geometry.
Custom surfboards have been made for many years, but it’s a tedious process and quite expensive for buyers due to the labor involved. However, Modix has a new approach: 3D print the surfboard with a parametric design that can be easily customized for the individual buyer.
Large surfboards can be printed in Modix’s enormous 3D printers, while smaller devices might struggle to accommodate them.
The print actually uses a special “foamy filament” that “weighs nothing”. This makes the resulting surfboards incredibly lightweight, a highly desirable property.
Now for the really interesting part: the system to produce these custom boards can be packaged up to form a “Tailor made surfboard business in a box”. This makes it very easy for an entrepreneur to almost instantly set up a custom board business from scratch, or an existing board manufacturing to add custom capabilities.
You can see how this approach not only makes it easy for the customer to buy the solution, but it also makes them want the solution.
Another example Modix has been working on is custom musical instruments, specifically cellos. The sound from these instruments is derived from the geometry of their structure, and guess what, this can also be captured in a parametric design. Now you have a “custom cello business in a box”.
You get the idea: Modix can keep identifying these use cases and develop customized solutions for quite a variety of industries and applications. They’re also reportedly working on automobile restoration applications, which have similar properties.
New applications can be developed as these customized scenarios are found. Along the way, however, Modix could be selling a great many 3D printers.
Via Modix