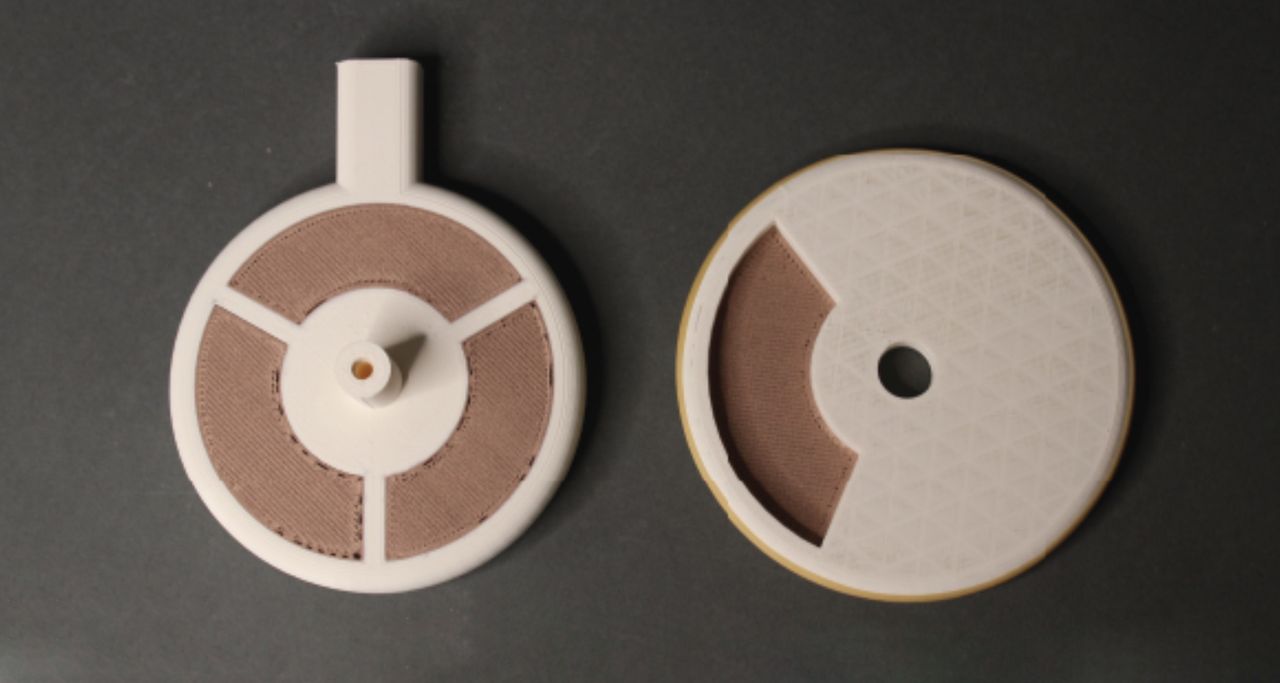
MIT has developed “MechSense”, a new way to integrate sensors into certain 3D prints.
Sensors are a critical part of most devices these days, and installation of them is usually an activity separate from building the core mechanical parts of the machine. That could change in the future with MIT’s new MechSense technology.
MIT explains the problem:
“Even though advances in 3D printing enable rapid fabrication of rotational mechanisms, integrating sensors into the designs is still notoriously difficult. Due to the complexity of the rotating parts, sensors are typically embedded manually, after the device has already been produced.
However, manually integrating sensors is no easy task. Embed them inside a device and wires might get tangled in the rotating parts or obstruct their rotations, but mounting external sensors would increase the size of a mechanism and potentially limit its motion.”
The idea is to 3D print the sensors embedded within the part itself, greatly simplifying the assembly and potentially increasing the reliability as well.
But how do you do that?
The researchers chose to use a capacitive solution, where conductive plates are adjacent, but separated by a non-conductive material. The electric field changes as the orientation and distance between the plates change. If they were able to embed plates on the rotating parts, they could measure the electric field changes to determine rotational speed, direction, position and more.
They were able to do so by 3D printing parts in both polymer and conductive material using a multimaterial 3D printer. MIT explains how it works:
”Rotational mechanisms typically consist of a rotational element located above, below, or next to a stationary element, like a gear spinning on a static shaft above a flat surface. The spinning gear is the rotational element and the flat surface beneath it is the stationary element.
The MechSense sensor includes three patches made from conductive material that are printed into the stationary plate, with each patch separated from its neighbors by nonconductive material. A fourth patch of conductive material, which has the same area as the other three patches, is printed into the rotating plate.”
This is a notable development because there are no wires involved — and no electronics assembly, either.
The result is a new approach to the design and printing of rotational mechanisms. It’s not clear whether this method can be used by everyone yet, as it may be under patent. Nevertheless, it shows a very practical approach for simplifying the production of functional devices using 3D printing.
Via MIT and Dropbox (the paper, PDF)