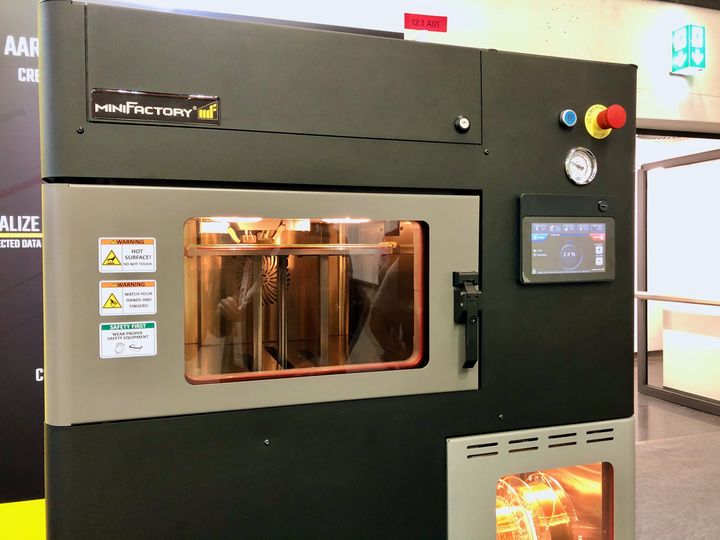
MiniFactory detailed their process for obtaining high-quality 3D prints with PEKK material.
Finnish company miniFactory has specialized in high-temperature 3D printing, specifically for the production of industrial parts. While there are several high-temperature 3D printers now on the market, miniFactory’s Ultra machine includes an integrated quality control system they call “Aarni”. Aarni is able to produce quality reports for each and every part produced.
Now they’ve described their work with chemical supplier Arkema to 3D print their Kepstan PEKK-SC material with great precision.
High-temperature 3D printing is a challenging task because the huge temperature gradients can cause all kinds of issues.
One issue is warping, as the extreme differences in temperature can see portions of the print varying wildly, and thus distortion occurs. MiniFactory’s Ultra machine overcomes this problem by heating the build chamber to a whopping 250C.
But there’s another issue: crystallization. MiniFactory explains the problem:
“Semi-crystalline polymers are more challenging to print as crystallization competes with interlayer diffusion. These high-performance materials are used in demanding applications, and there cannot be any compromise on the performance of additively manufactured parts.”
The goal is to have the proper crystallization occur when the part is finalized, but that’s quite challenging. The solution is to cool the printed part in a very specific sequence. MiniFactory explains how they accomplish this on the Ultra:
“The printing process was done using miniFactory’s custom process that automatically produces high crystallinity O-rings without any manual actions from the operator after the initial start of the print. The process uses conditions where the PEKK-SC remains mostly amorphous until the print is completed. Afterwards, the printer automatically adjusts the chamber temperature to induce a slow, controlled crystallization. This is possible due to the miniFactory Ultra 3D printer 250°C build chamber.”
In other words, they’ve developed a specific temperature cooling profile for this material, and can implement it in the fully controlled heated build chamber. If the build chamber can reach 250C, it can be set to any other lower temperature as required over a period of time.
They’ve combined this process with the Aarni system to ensure the PEKK parts not only achieve the desired quality, but also to ensure the process can be reliably repeated if serial production is required.
The application for this experiment was to 3D print O-ring seals to be used in extreme environments. These would obviously require high quality to ensure they performed without failure. MiniFactory explained the results of their test:
“The finished rings maintain their shape extremely well. Optical microscopy shows incredibly low porosity. There are only a few small pores where the perimeters meet the infill. The compressive properties of the printed PEKK seals closely match an extruded or compression molded reference. The density of the printed rings is >99% of the typical value for injection moulded semi-crystalline PEKK. These properties are particularly important as it is the main operating mode of a seal. These technical results firmly establish PEKK additive manufacturing as a serious option to produce high performance parts.”
This demonstration clearly illustrates some of the challenges and solutions when attempting to produce high-performance parts using 3D printing. It’s likely miniFactory will develop further temperature profiles for other materials to achieve similar results.
Via miniFactory