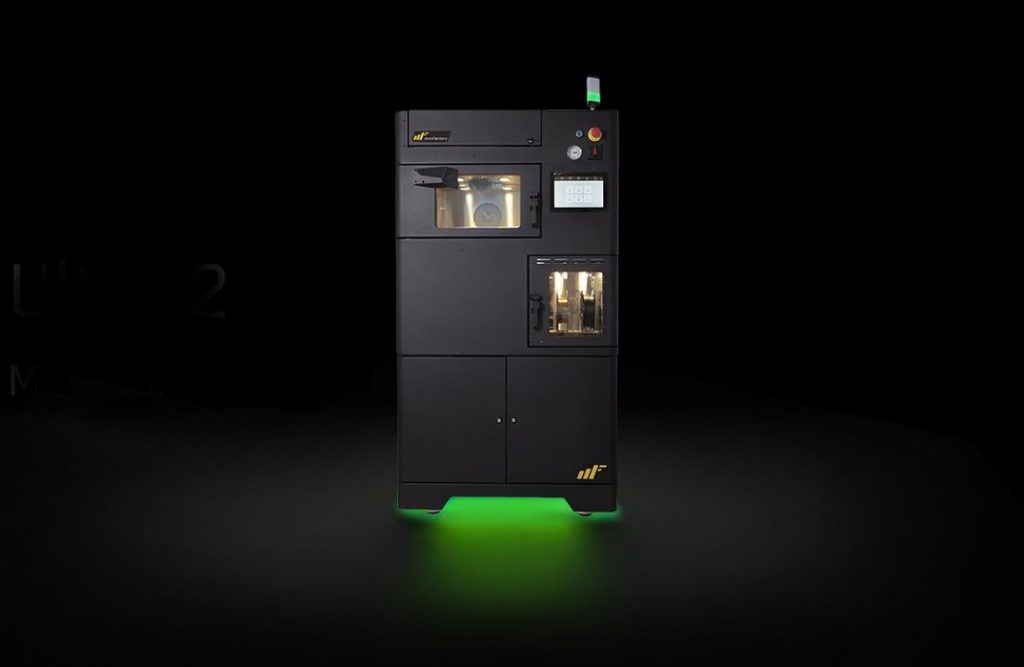
The Finnish company has long been developing 3D printers, with our first encounter with them being almost ten years ago. At the time they produced a single-head, open gantry style device. Now, years later, they have advanced significantly.
In recent years the company has focused on the issues related to additive manufacturing of polymer parts. While it’s possible to make parts with many machines, miniFactory’s concern was about proven and documented quality. They’ve produced several innovations in this area, one of which is the unique “Aarni”, which is a way to record and analyze each print layer of a build job. If the layers are all within required tolerances, then the part could be considered “certified”.
miniFactory also produces official certification documentation with their Technical Sheets, which can be extremely useful in production environments where critical parts are produced.
Their latest device, the Ultra 2, carries forward from their previous flagship device, the high-temperature capable Ultra. But it seems that miniFactory has done some very significant changes to their system in the Ultra 2.
The Ultra 2’s main feature seems to be a new “smart heated chamber” that can reach a blistering 250C. This enables the device to handle virtually all polymer filaments on the market today, including PEI, PPSU and PEEK. In all, miniFactory said the Ultra 2 can support over 50 different kinds of materials.
But what about the “smart” in this heated chamber? miniFactory explains:
“A completely new triple censoring and active temperature adjustment makes the heated chamber extremely stable and enables precise temperature control. Thus, the printed parts are now made with even better quality and precision.”
The Ultra 2 builds on the previous part quality and certification systems, but integrates it all together. miniFactory explains:
“For the first-time, monitoring of all important manufacturing steps, starting with material traceability, and ending with the quality report of the final parts, have been compiled together. As a whole, miniFactory quality control verifies several critical production steps, which is a prerequisite for reliable additive manufacturing.”
This feature should be extremely attractive to manufacturers, as a lot of their otherwise manual work could be taken up automatically by the Ultra 2’s new process.
miniFactory has included a production monitoring and control system that is capable of handling multiple Ultra 2s simultaneously. This should allow an operator to efficiently manage a group of Ultra 2s, while at the same time ensuring they each produce parts that meet required quality control standards.
miniFactory said the device is to be first shown to the public at Formnext next week, and should be available to customers before the end of the year.
Via miniFactory