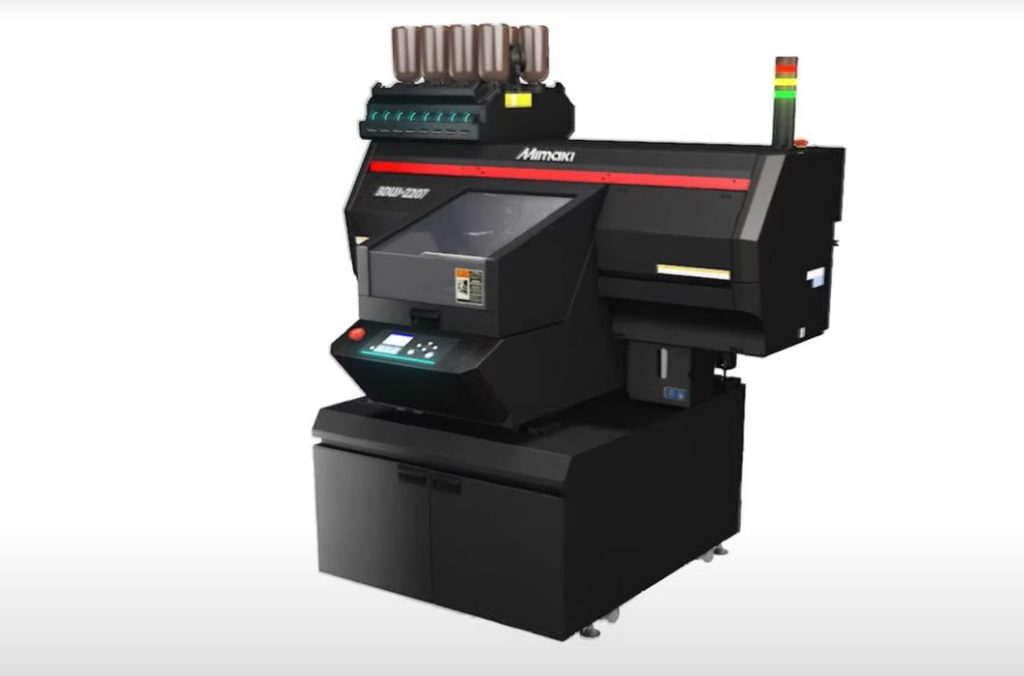
I had a chat with the folks from Mimaki, makers of a line full color 3D printers.
When I say “full color”, I’m not talking about typical multi-color 3D printers that can switch colors now and then during a print job. No, here I mean actual, full, photorealistic color textures.
That capability has been the claim to fame by Mimaki for several years since they entered the 3D print market.
Mimaki is actually one of the older companies we cover, having been founded way back in 1975. Of course back then they didn’t market 3D printers because they hadn’t yet been invented. They began, and still to this day, make all manner of advanced 2D printers, including inkjet, textile, roll-to-roll, as well as other related equipment, including plotters, cutters, laminators, etc.
But only a few short years ago they entered the 3D print business with the 3DUJ-553, a resin-based full color 3D printer. Their process involves selectively depositing layers of photopolymer resin, and then having a UV lamp cure each layer. This repeats, layer-by-layer, until the print is completed. After removing the disposable support material, you’re left an incredibly photorealistic 3D printed object.
I spoke with Mimaki’s Arjen Evertse to find out what’s happening this year with the company.
Evertse told me that Mimaki has been leveraging much of their long-developed 2D printing technology for the 3D world. They deeply understand colors and high speed production, and were able to bring that to the 3D world four years ago.
“The 3DUJ-553 is a big machine, famous for its print quality, with a big build volume and a big price tag. There is a lot of interest, but the price is too high for some customers. New this year is the 3DU-J2207. We use the same tech from the big 3D printer in a smaller, desktop, full color version.”
The 3DU-J2207’s build volume is indeed smaller than the 3DUJ-553’s huge 508 x 508 x 305 mm, at “only” 203 x 203 x 76mm. The new machine’s weight is also tremendously lower, at only 140kg, whereas it’s larger sibling is a massive 600kg.
Both machines offer similar color capability, with a resolution of 1200dpi. However, the larger machine can handle slightly thinner layers at 0.020mm, while the new desktop device can go down to 0.028mm. However, in practice this shouldn’t make much difference to the eye.
The big difference with the new machine is the price. Evertse said the price of the larger machine is near €200K (US$226K), while the smaller unit is a far more affordable €35K (US$40K).
Evertse said:
“The 3DU-J2207 is a bit slower, but all other capabilities have been brought to a more affordable machine. It brings full color 3D printing to a much larger audience.”
This is very likely true, as the only other option to obtain similar color quality might be Stratasys, but they have no machine at this new low price point.
Full color 3D printing is still relatively rare in industry, as most engineers focus on the mechanical aspects of parts. Use of full color is really for different types of applications, and my suspicion is that many manufacturers simply don’t yet know how or what to do with a full color 3D printer. I asked Evertse about this, and he said:
“Exploring the 3D printing world — it’s a different world for many companies. Besides the initial investment, the learning curve is an issue, and full color 3D printing is even more complicated.”
Apparently those companies that currently operate 3D printers had some knowledge, but for full color 3D printing applications, new customers don’t have any background in 3D, making a transition tricky. Evertse said this is becoming a “really big issue”, because they’re aiming for a much larger audience. This is something that Mimaki will no doubt be addressing in the future.
One problem cited by Evertse is that of support removal, which is a bit different in full color 3D printing versus “normal” resin 3D printing. Typically support materials are removed using a solvent to dissolve the material to reveal the final object.
However, in full color 3D printing a common problem is that the solvent gets polluted with support material, and ends up sticking onto the print as a thin layer. This can spoil the visual appearance, which is the goal of full color 3D printing.
To mitigate this issue, Mimaki has partnered with a German firm to develop an unusual support structure removal system that uses a unique “sink float” principle.
The forthcoming intelligent cleaning system will use a propeller to create solvent flow, and the support material will sink to the bottom, while the printed object will float to the surface. This should avoid the support pollution problem entirely.
That new system will also provide Mimaki clients with a complete end-to-end manufacturing solution that will be reliable and have consistent throughput.
To make it all work, the company has also introduced a cloud system, 3DPrintPrepPro, “3DP3” which will provide operators with easy ways to prepare jobs, detect errors and repair 3D models. Evertse said:
“We’re trying to make the process of 3D printing easier.”
I asked Evertse what kind of applications for full color 3D printing they are seeing these days, and he explained:
“There could be quite diverse use on the small printer. The figurine printing business is continually growing. It’s not always human figurine, it’s also game collectables. This is a very big market, where in online games people spend a year building their character and want a print of it.
Medical models also have surprising interest, especially for educational objects due to the photorealism possible on Mimaki equipment. Product prototyping is more in reach, where it is now feasible to do this in house. Prototyping could be anything — a razor, for example, or an electronic device where the color must be tested.
Packaging is another application: Glass packaging for cosmetics is very hard to do with mockups, but we can make them perfectly. A mockup of a perfume bottle is almost like the real thing.”
It seems that full color 3D printing may finally be taking off, after many years of development.
Via Mimaki