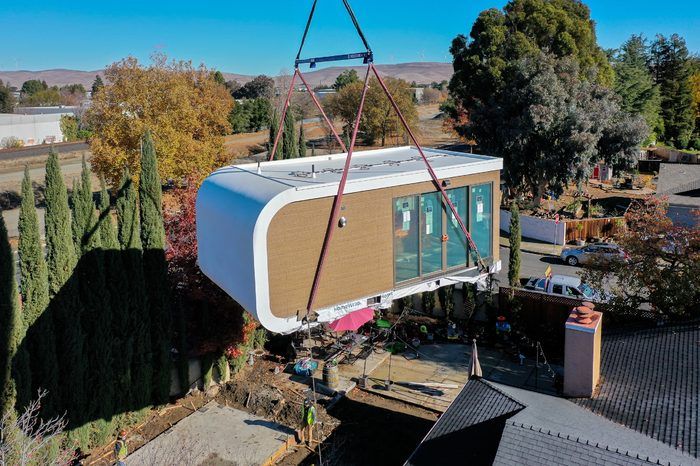
California-based Mighty Buildings announced a new investment round of US$22M.
Mighty Buildings has been developing a new form of construction 3D printing that, so far, has proven effective.
While some construction 3D printing companies print building structures on site using concrete extruders, Mighty Buildings takes a very different path.
Instead of using the equipment on site, they operate a factory at a centralized location, and then transport the completed 3D printed homes to their installation site.
The factory 3D prints structures using an undisclosed polymer material they call Light Stone Material, or LSM. Their process uses a photopolymer resin, and is cured using UV light. Apparently the printed parts resemble Corian, a common building material. I took a deeper dive into Mighty Buildings’ process earlier this year.
These 3D printed parts are matched with other building materials to effectively create a fully finished home. Mighty Buildings ensures the home design is relatively small, because the finished product is lifted onto a truck and whisked away to its installation destination. There, a crane lowers the new home onto its final position.
The system they’ve developed offers the possibility of high efficiency. For example, they don’t have to set up and tear down the 3D printing equipment, as is done on most on-site construction 3D print jobs. Their micro-factory can pump out as many homes as possible in a continuous fashion.
This allows the company to potentially operate in a profitable manner. However, as they are privately held, we don’t know whether they are profitable at this stage.
The concept is quite scalable, in two ways.
First, they can add more equipment to the centralized micro-factory. This enables them to create more buildings at a higher throughput rate.
The problem with a single micro-factory is that it is tied to a region for geographic reasons. The factory can serve an area proportional to its shipping and installation reach. So far, the company is working in a zone around its Oakland HQ.
However, this leads to the second scalability approach: make more micro-factories in other regions. Once they’ve figured out all the details in the process and can make it efficient, Mighty Buildings can then deploy similar operations in other regions. Eventually they could cover many areas around the world if the process is locally acceptable.
If this sounds like an attractive idea, you’re not alone. Many investors have put big cash into Mighty Buildings. According to TechCrunch, they’ve now raised US$101M, including the most recent US$22M, which is an extension of the US$40M Series B announced early this year. While the majority of the prior investment was from VC Kholsa Ventures, the most recent round included a number of VC firms.
Evidently they believe the Mighty Buildings concept will work and scale.
So do I.
Via TechCrunch and Mighty Buildings