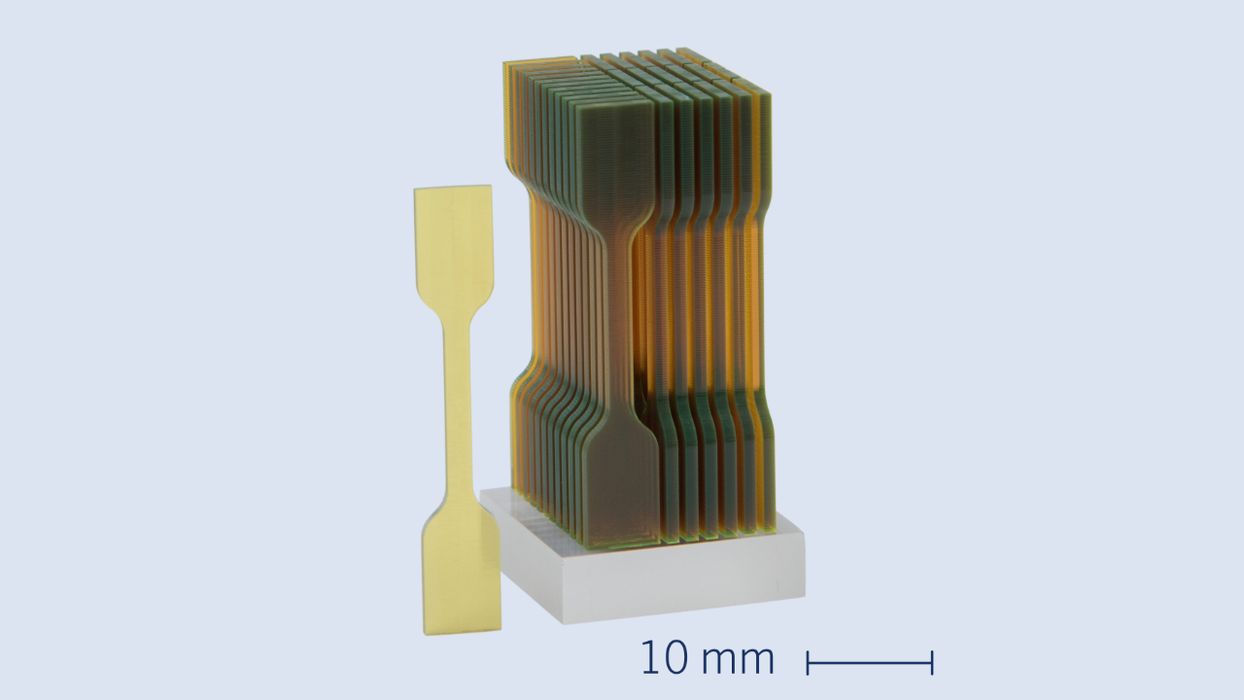
There’s been a breakthrough in the ability to properly measure the strength of microscopic 3D prints.
Normally the engineering properties of 3D print materials and processes are done in a very rigorous manner. Standard 3D model specimens are placed into precision measuring equipment that bends, breaks and stretches them until them break. By performing such testing over multiple samples, reliable data about the engineering properties can be obtained.
That works just fine for normal 3D printing, where the print specimens are 200mm long and able to fit into the equipment.
But what about far smaller 3D prints? What about the prints produced with the 2PP process?
Catch up: 2PP is a unique 3D printing process in which lasers are focused to an extraordinarily tiny point within a vat of transparent resin. This focal point has sufficient energy density to trigger polymerization. By moving this focal point around 3D space within the resin, complete objects can be produced.
The advantage of 2PP is that the focal point is so small that extremely tiny prints can be made in astonishing resolution.
The problem here is that these prints are too small to fit within normal testing equipment. So how strong are these parts, then? No one really knows.
Until now.
Researchers from TU Wien collaborated with UpNano and their ultra-fast 2PP 3D printer the NanoOne to make this happen.
UpNano explains:
“The team was able to test a wide range of mechanical properties of the 2PP 3D-printed material, including tensile, flexure and hardness, as well as creep and fracture behavior. The materials used were ETA/TTA – ethoxylated (20/3)-trimethylolpropane triacrylate (ETA) in combination with trimethylolpropane triacrylate (TTA) – and two commercially available materials from UpNano GmbH, UpPhoto and UpDraft. To achieve the production speed required for large samples, the team used 10x or 5x objectives mounted on a NanoOne printer from UpNano. This is currently the fastest commercially available 2PP 3D-printer on the market, capable of printing over 15 orders of magnitude with respect to print volume.”
This development will permit proper testing of 2PP prints, and that will allow some part/printer combinations to produce ISO-certified parts. This then opens the door for new applications where certifications are required.
Via UpNano