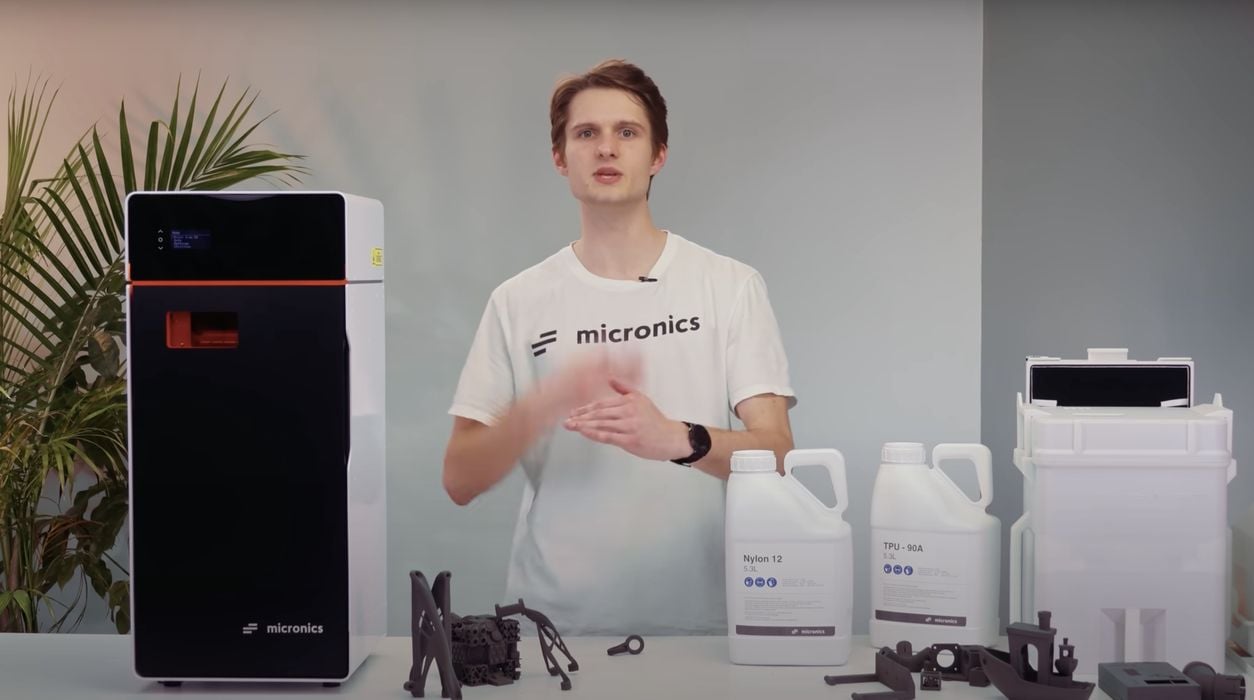
Micronics seems to have developed a very inexpensive desktop SLS 3D printer.
SLS is a very powerful 3D printing process. It involves blasting a laser at a flat bed of thermoplastic powder. This fuses some of the plastic together, and this repeats layer by layer to form complete 3D objects. SLS is able to produce 3D objects in a variety of strong thermoplastics.
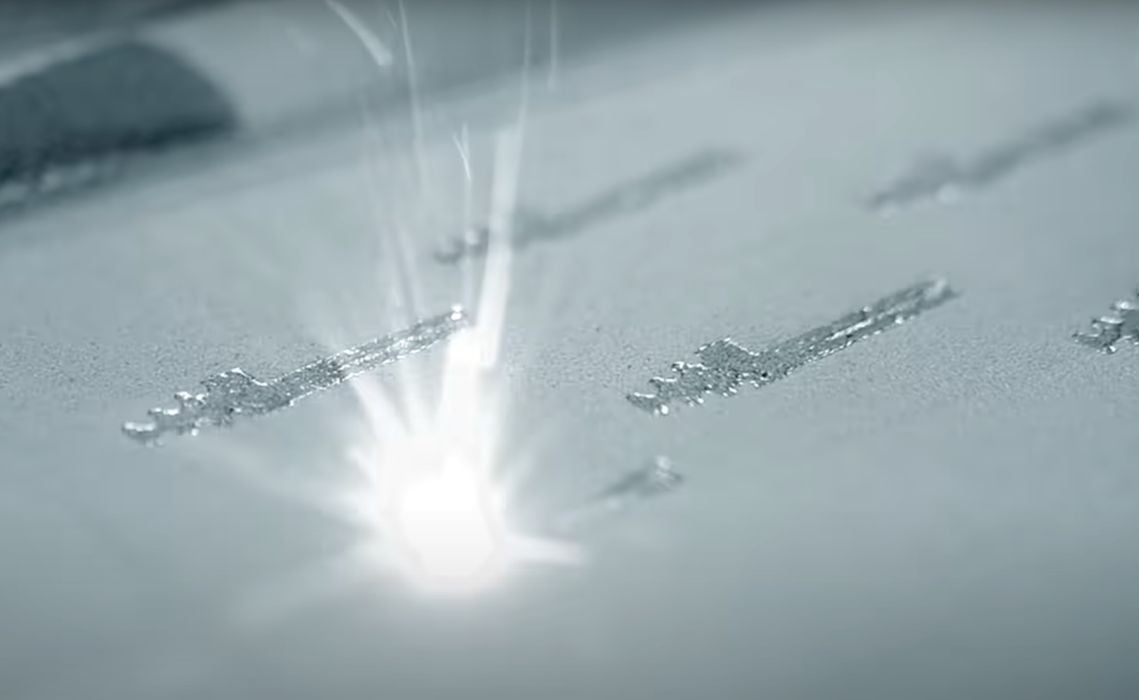
There are multiple advantages of SLS, but the main one is that because the print takes place within a block of powder, there is no need for support structures: you simply lift the printed objects out of the powder and they’re done!
Why isn’t everyone using SLS 3D printers? It’s because there are multiple practical challenges to making it work properly, and making a system inevitably costs a considerable amount of money.
Industrial SLS systems tend to cost as much as US$100,000 or more, and there are few inexpensive systems. Two lower cost options are available from Sinterit and Sintratec, both of which initially offered SLS systems costing around €5,000. Since then, Sinterit has moved on and their lowest cost system is around €12,000 (US$13,000). Sintratec still offers their original “Sintratec Kit” for €5898 (US$6400).
Those systems are less expensive than big commercial systems, but hardly affordable by all.
Now that scenario could change with Micronic’s upcoming (and apparently unnamed) device is touted to be a desktop SLS 3D printer that will cost only US$2999 — less than half the price of the Sintratec Kit!
The inability to bring costs down has long been due to challenges with laser costs, heating for quality and the mechanics of powder handling. Most attempts at low cost SLS machines echoed the expensive designs, limiting the cost reduction.
However, Micronics has created several very innovative approaches to the problem, and apparently has been able to significantly reduce the price of the 3D printer.
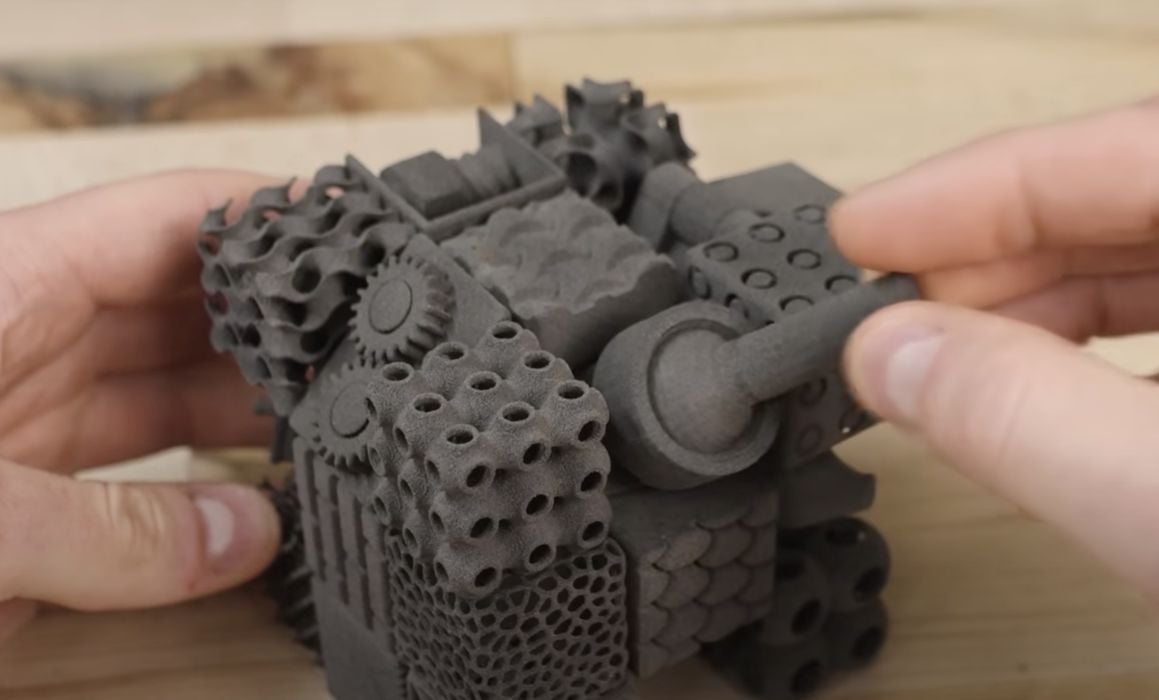
What did they do? The main approach seems to be in how they handle powder. Rather than having two pistons push powder around, their single-unit is able to recoat layers of powder in a much simpler manner. That reduces the cost of the mechanical systems considerably.
Another unique approach is to apply a layer of glass above the print surface. This insulates the printer from the build chamber, allowing for easy material changes. In typical SLS 3D printers this is basically impossible without disassembling the machine to clean out all the previous powder.
The glass also provides an interesting way to optimize heating. Heating is required to reduce the amount of energy required by the laser to fuse the thermoplastic particles. Normally SLS systems heat up the entire build chamber to something just short of the melting point. Then the laser pushes it just over as required.
The glass layer creates a much smaller zone that would require heating, and that significantly reduces the energy required for heating, as well as significantly reducing the warm-up time.
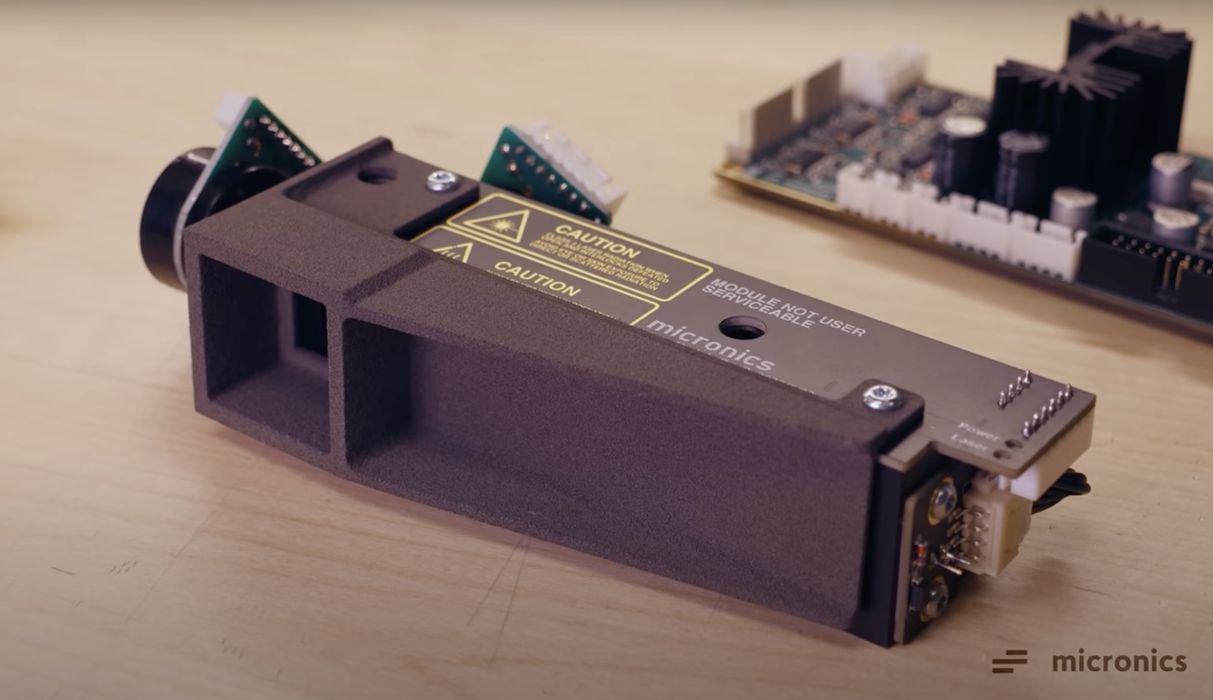
Micronics has also devised their own low-cost galvanometric mirror system, which should also reduce the expense to build the machine.
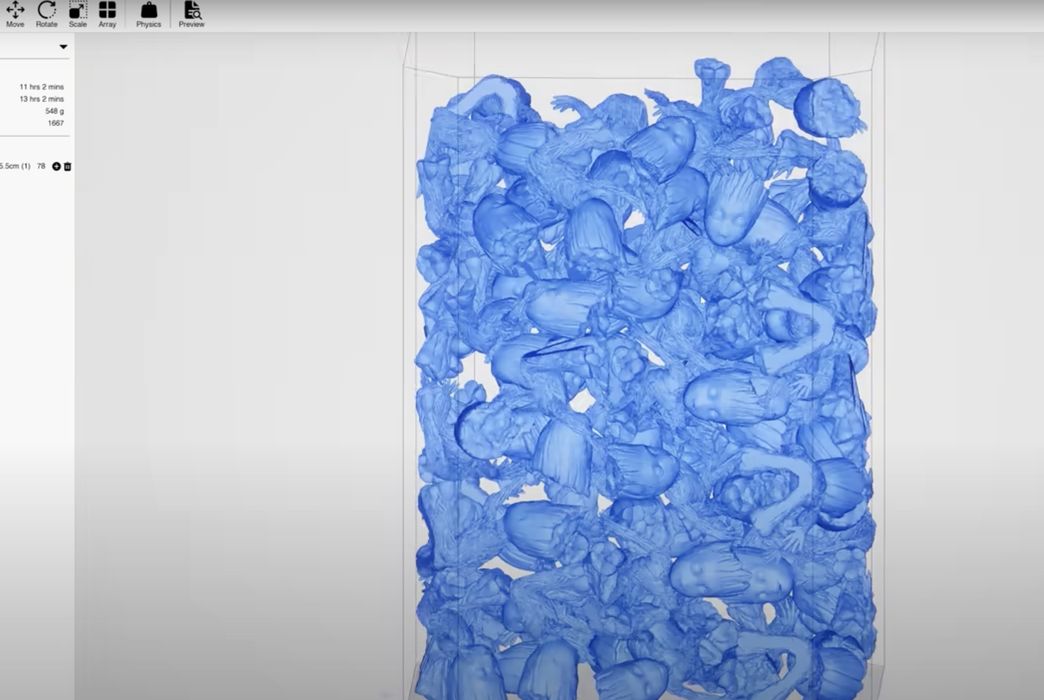
Micronics has also developed their own slicing software for the system, as you cannot use typical FFF slicers: SLS can print objects in three dimensions, stacking them up within the powder cake. A very interesting aspect of their slicer is that it’s built using Unreal engine. I’ve never heard of a slicer built using the popular 3D gaming engine, and wondered why one would do so. It turns out that they use Unreal Engine’s physics engine to help “Tetris” the parts into the 3D build volume.
This video provides a good overview of the system:
Note that SLS does require some post processing to remove stray powder from the prints, and that will require some special equipment, at the very least a dust extractor.
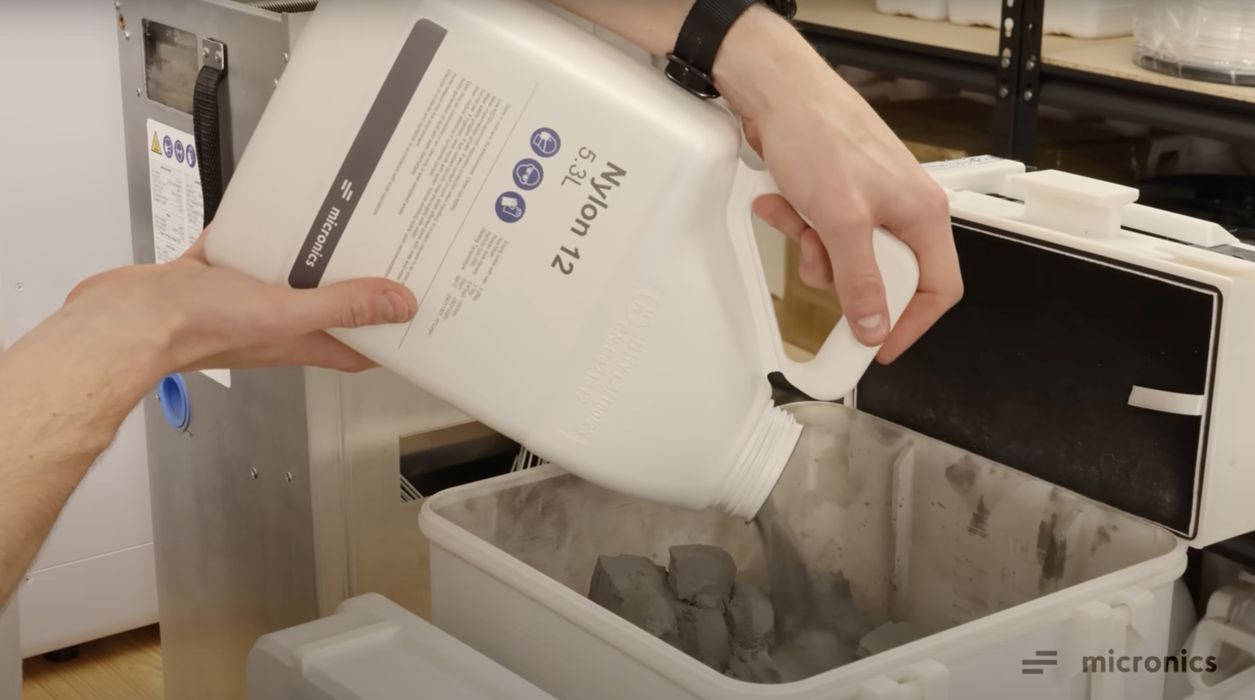
Another challenge with SLS is that the powder must be kept away from oxygen and humidity as much as possible to ensure proper quality. Micronics has taken some steps to reduce exposure, and even simplify the need for extensive PPE during post processing. Used powder can only be used in a certain ratio with fresh powder because of this, so operators may use somewhat more material than required by the objects themselves.
One important specification is the build volume: 160 x 160 x 200 mm. That’s not particularly large, but should be sufficient for the production of many parts. Remember that the entire 3D build volume can be used to stack up parts for a single job run.
Nevertheless, the result from Micronics is a very interesting desktop SLS 3D printer that will apparently be available at low cost in the near future. The system already handles PA12 and TPU 90A, and they have plans to certify PA12-GF, PA12-CF, PA11, PA6-GF, and PP in the future.
For now, it seems that Micronics is providing a print service: upload a 3D model and they will print it on their equipment before release. That would allow users to inspect part quality and help determine whether this machine is for them.
The cost of the unnamed system is within the range of affordability for far more people, and even consumers and hobbyists may begin using SLS.
Via Micronics