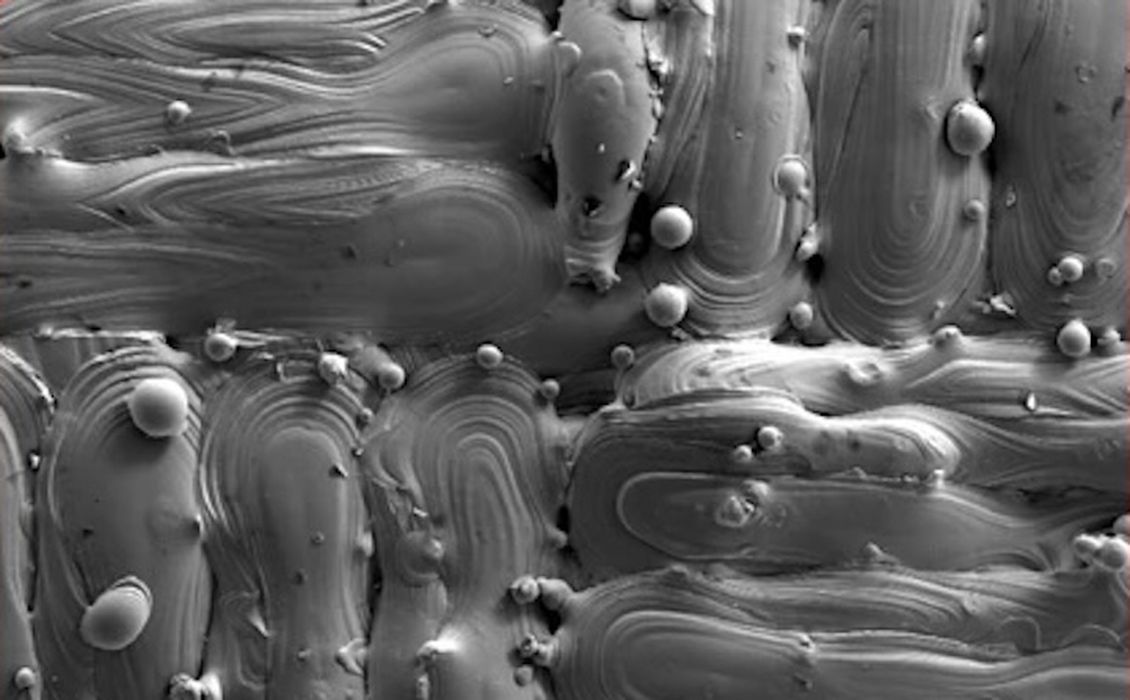
A breakthrough in corrosion prevention has been made by metal 3D printing researchers.
The problem being investigated is corrosion of 3D printed metal parts, specifically those made using the popular LBPF process. In this process, a flat bed of metal powder is fused layer by layer to form fully 3D metal objects.
There are many types of corrosion, and apparently corrosion generates an astonishing US$276B in damages annually in the USA. This indicates the importance of solving even a small piece of the corrosion puzzle.
Here the researchers were particularly interested in how seawater corrodes 316L stainless steel material. 316L is frequently used for a wide variety of marine applications, but corrosion may be limiting the potential.
They noted that conventionally produced 316L exhibits less corrosion if post processed (polished), but would the same effect be taking place with LPBF-produced objects?
They used a variety of high-power tools, including transmission electron microscopy to investigate the surface oxides on 3D printed metal samples.
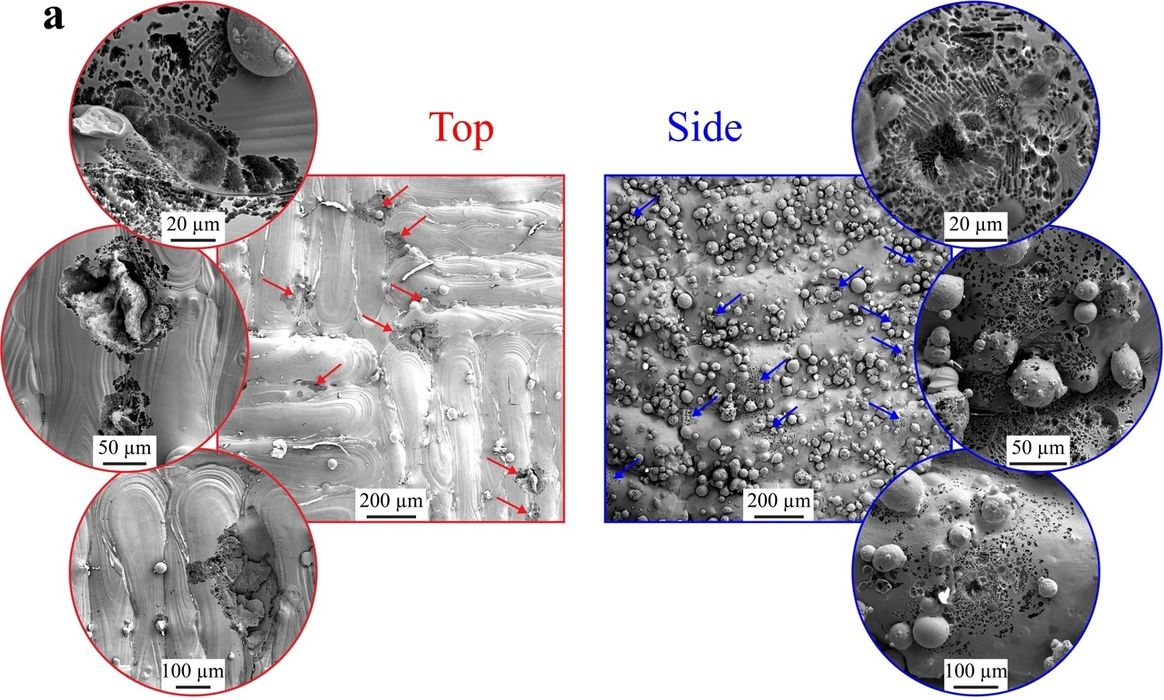
They determined that a large proportion of the seawater corrosion on LPBF-produced 316L parts was caused by slag.
Slag are tiny bits of metal that somehow appear on the surface. The researchers found there were two sources for slag: derived from the input powder media itself, and from spatter produced during the printing process.
These bits of slag were found to be rich in manganese sulfides, which is the chemical that reacts with seawater. This is the cause of the corrosion. They explain:
“Their dimensions, structure, location, and level of protection are all related to the temperature and environment in which Mn and Si reacted with oxygen. Note that Mn and Si are usually introduced in the 316L SS composition to limit the amount of oxygen in the metal during conventional casting or welding.”
Aha, this is the interesting part. It seems that the standard additives used for conventional 316L might be causing the problem in LPBF manufactured parts. They explain further:
“LPBF is a different process due to the nature of the feedstock and extreme local processing conditions. The merits of Mn and Si for LPBF 316L SS are therefore less clear and prompt further investigation. In particular, we propose that a new 316L SS composition could be adapted to LPBF by avoiding the addition of Mn and Si to prevent slag formations.”
In other words, LPBF requires a different formulation of 316L metal in order to prevent corrosion.
That sounds like a somewhat straightforward solution to a challenging problem — and also demonstrates the difficulties in simply adopting a conventional material for additive manufacturing.
Based on this research, it’s quite likely we will soon see some corrosion-resistant 316L materials appear in the marketplace soon.
Via Nature