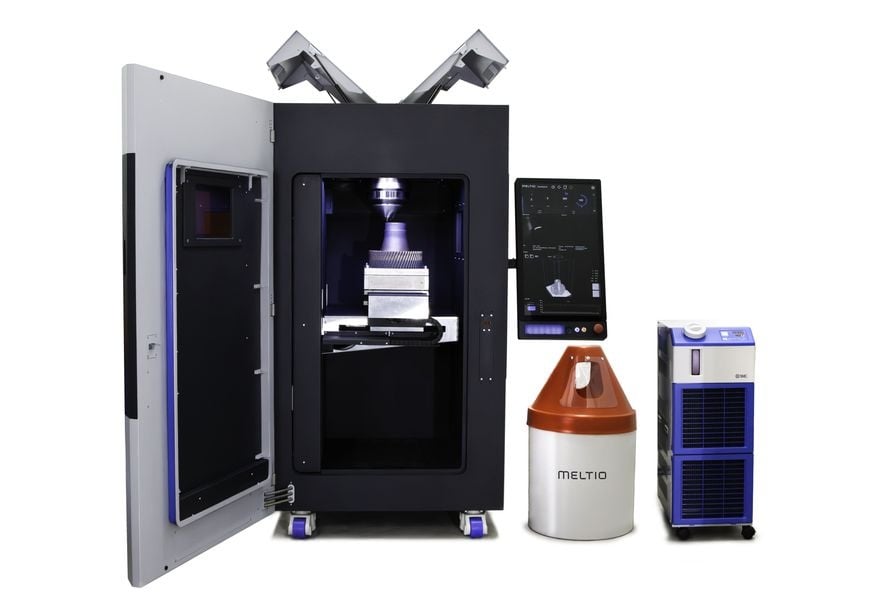
Meltio released a new and interesting metal 3D printer, the M600.
The company has previously released a series of wire-laser deposition additive manufacturing solutions that produce metal objects without the need for expensive metal powder. Powder systems are difficult and expensive to operate due to safety and handling concerns.
The new M600 is also a wire-laser deposition system, but the key difference is that it uses a blue laser. That’s very different from the typical near-infrared lasers used in most other laser-based metal 3D printers.
What’s the big deal with a blue laser? The light has a different frequency that offers two major advantages.
First, the tighter wavelengths are able to transfer more energy to the target. This means that less power is required to melt the same amount of metal. That will provide cost savings, and possible lengthen the lifetime of the equipment. It’s also possible to print at a faster rate due to the increased energy absorption.
Secondly, the wavelengths are better able to transfer energy to usually difficult metals, such as copper or aluminum. Whereas other systems cannot or only with difficulty handle these metals, the M600 is able to handle them routinely.
The M600’s motion system uses a closed loop
approach, with servo motors and linear axes. There are considerable sensors included in the system that help maintain operational consistency.
Here you can see a print sample from Meltio, showing good detail. While the prints are somewhat coarse in resolution as compared to LPBF systems, the M600 will be far less expensive to operate and produce models that are quite suitable for many applications.
The build chamber is said to be “fully inert”, and the system manages both oxygen and humidity levels, which should encourage good quality prints.
Finally, Meltio has packaged the entire system in a compact format that’s ready for use. At top you can see an image of the system, and it’s easily installed in many possible locations.
The build volume on the M600 is quite substantial at 300 x 400 x 600 mm. This will be ideal for many applications, and yet the size of the printer itself is quite compact.
The M600 is also capable of repairing metal objects, as its robotic system can apply metal to existing surfaces. This is normally quite challenging to do, but Meltio has included several features to make this process easier. One is a zero point clamping system that will help locate the part in 3D space, and also a three axis touch probe.
Meltio has also spent time to refine the user interface to be more user friendly, and the systems is designed for continuous production, even autonomously.
The M600 looks to be a very attractive machine for specific metal production applications.
Via Meltio