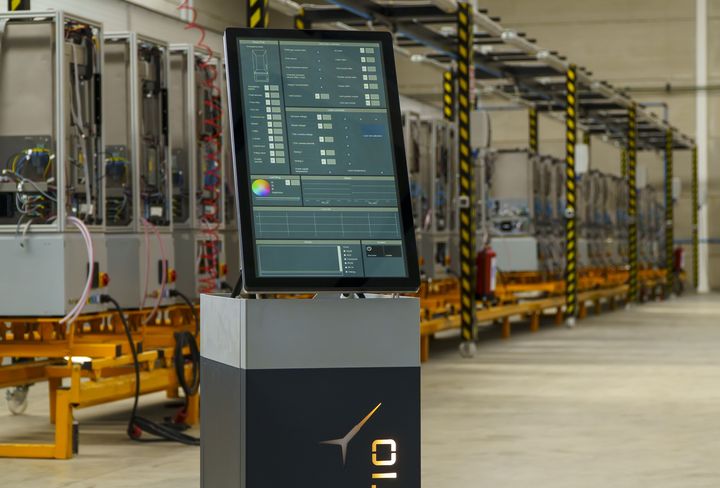
Meltio announced the “Meltio Engine”, a hardware upgrade for CNC equipment to combine additive and subtractive manufacturing capabilities.
Meltio, if you recall, is a joint venture additive company by Spain’s Grupo Sicnova and Las Vegas based-Additec. The new company leverages Sicnova’s knowledge of 3D printer manufacturing with Additec’s amazing metal deposition mechanism.
The Additec toolhead is a marvel, allowing use of both powder AND wire inputs. These materials travel through a channel, and when they emerge they are struck by a series of powerful lasers that immediately melt the metals. These then are deposited in place. By moving the toolhead around in 3D space one can build a fully dense metal object.
This technology can be used to 3D print metal objects, and also perform repairs, cladding or augment features on an existing metal object.
Meltio’s first metal 3D printer using this technology was the Meltio M450. This compact metal 3D printer offers an unusual vertically-oriented build chamber of 150 x 200 x 450 mm. The build chamber’s vertical shape is no doubt an effect of the Additec technology, but should be welcome for those building taller parts.
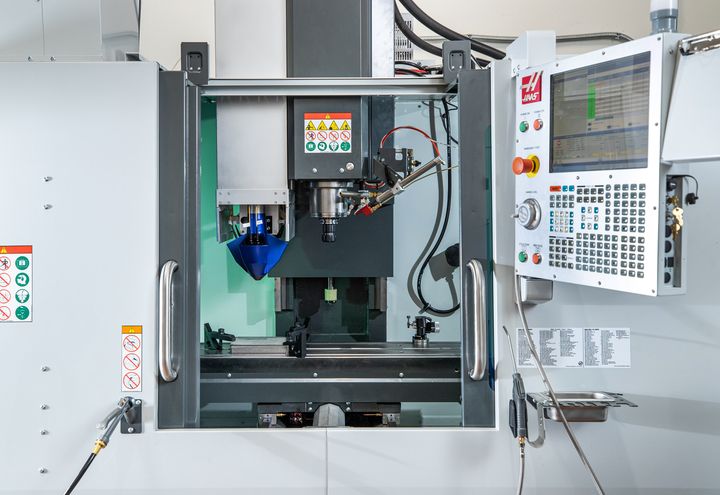
The new product is the Meltio Engine, which is a way to integrate the metal deposition technology into existing CNC equipment. The idea is that by performing this integration, a subtractive device can suddenly become capable of both subtractive AND additive processes within one box.
The reason for interest in this is because most 3D printed metal objects have a rough surface due to the resolution of different metal additive processes. Typically manufacturers take completed metal 3D prints and post-process them with 5-axis metal CNC machines to not only smooth surfaces, but create bolt holes and other necessary features.
But now with the Meltio Engine, a CNC operator could perform both of those steps within a single machine. This could increase manufacturing efficiency significantly, as there would be no need to transfer heavy made parts from machine to machine. In addition, there could be floor space savings that could translate into greater capacity expansion options.
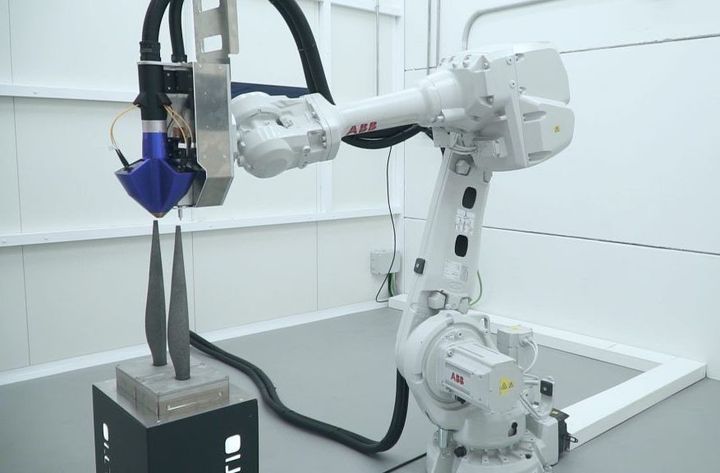
Meltio says the “engine” can be integrated with a variety of different CNC machines, including both robotic and gantry systems. They say it can be used to retrofit “almost any tooling machine”, and at an “affordable” price.
This capability implies something else: the additive process can be scaled as large as you need. Gantry systems in particular can be expanded to massive volumes, and the Meltio Engine can simply travel along the same paths.
The Meltio Engine can use either wire or powder as input, but it seems that Meltio is focusing more on wire applications at the moment, and can even switch wires on the fly during a build job. That said, they say they can switch to powder as well, and this offers a number of interesting options.
Powder allows the possibility of creating new alloys on the fly by mixing powders at input. In fact, Meltio says they are even able to create “alloy gradients” using this approach, which is quite interesting.
Meltio says prints typically don’t require post-processing heat treatments due to the nature of the deposition. The highly-dense metal prints are usually of sufficient strength and have “exceptional microstructures”.
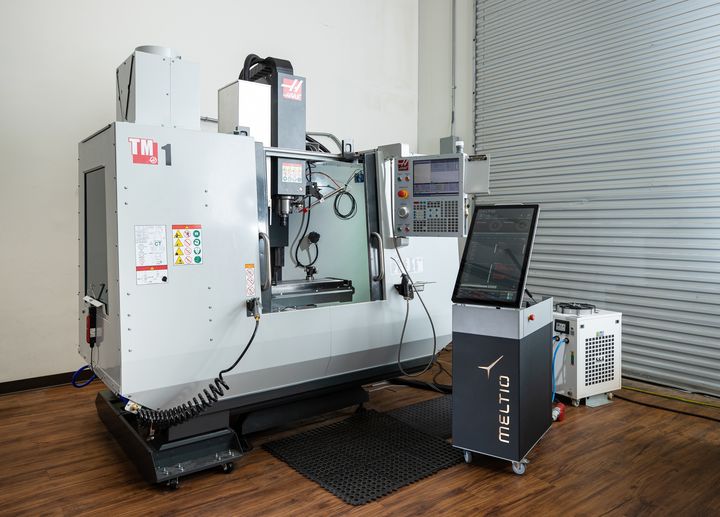
Pricing for the Meltio Engine depends on the configuration involved, obviously, but the company is offering a five percent discount for a short time if your company is interested.
But the price of the Meltio Engine is likely at a level that allows the savings from hybrid manufacturing to justify the purchase. However, every situation is different and analyses should be done.
Via Meltio