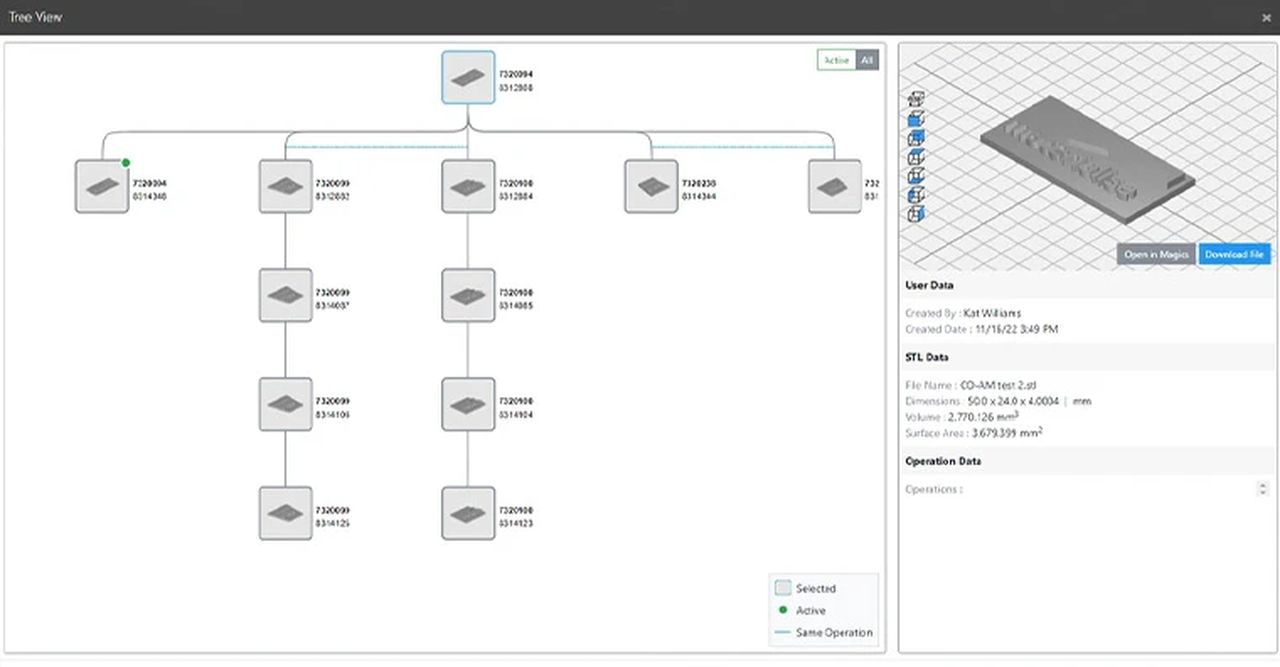
I had a brief discussion with the folks from Materialise to learn more about their latest developments.
The Belgian company is one of the oldest in the space, and while they don’t sell their own 3D printers, they do dominate the software side of the additive equation. Their flagship product, Magics, is one of the prime choices for job preparation and management by the industry.
Their latest release of Magics, version 3.7, focuses on traceability. This is the ability to figure out exactly how a given part was produced. This includes tracking the machine it was made on, the specific materials used, and the print parameters.
Traceability is a strong requirement in many industries because it enables the diagnosis of issues that may surface later. For example, if there’s an aerospace accident, it’s possible one could trace the fault down to a bad batch of materials used on a machine months earlier. This would also allow identification of other parts made from the same bad batch for replacement.
Materialise explains how Magics addresses these requirements:
“From product design to part and build preparation to printing, the digital thread connects the entire manufacturing process. To facilitate this, connectivity and traceability are crucial; that’s why the most recent update of Magics prioritizes connections with other software solutions.”
Using their CO-AM platform, their software is able to develop a “revision tree” that “logs every action applied to a part or build.” It also records who specifically undertook the action.
This approach links previously separate activities in the production chain and provides a high-level overview of what’s actually taking place. Without this traceability, it could be enormously challenging to diagnose issues down the line.
Materialise is also “cloudifying” many of these services—although it’s important to note that this is not a requirement because many of their customers must use locally operating software.
The result is an ability to dispatch work “evenly” across a network of 3D printers.
We were told of an ability to create further automation via scripts. I got the impression that a customer would work with Materialise’s professional services group to develop scripts, but they can be incredibly useful. One example would be labeling, where the script generates unique labels for each part. That would also aid in traceability.
Apparently, CO-AM now has an “App Store” where one might find scripts that can add functionality and streamline workflows. Like all app stores, the CO-AM version is sure to provoke interest in the platform as more scripts are added.
Materialise told us their plan is to help customers “get it right the first time,” which isn’t surprising. However, it turns out that there’s a reason for this strategy: their surveys of 600 customers indicated that one of the biggest issues was how to train staff quickly.
You could train staff quickly using new teaching approaches, I suppose, but another solution would be to simplify the environment—reduce the amount of training required. That seems to be what Materialise is doing with these latest software developments.
It seems that Materialise’s approach is to understand the customers’ needs and attempt to resolve them using advanced software techniques. That sounds like a winning strategy to me.
Via Materialise