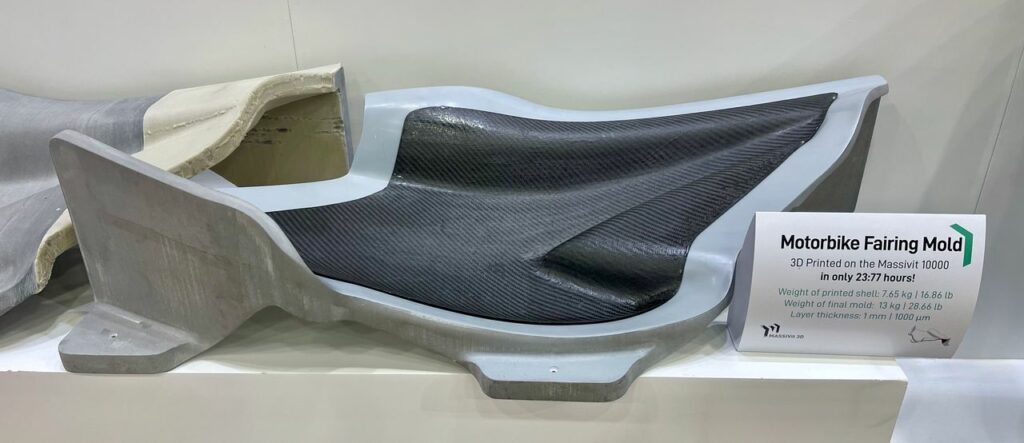
We recently had a chance to talk with Massivit directly.
Massivit is an Israeli firm that specializes in developing 3D printers that are, well, massive. They use a very unusual 3D printing process that is ideal for producing larger objects.
GDP, or “gel dispensing process”, involves extruding a photopolymer gel in thick strands into a UV-bathed chamber where it solidifies instantly. This process can easily stack up layers quickly to form very large objects.
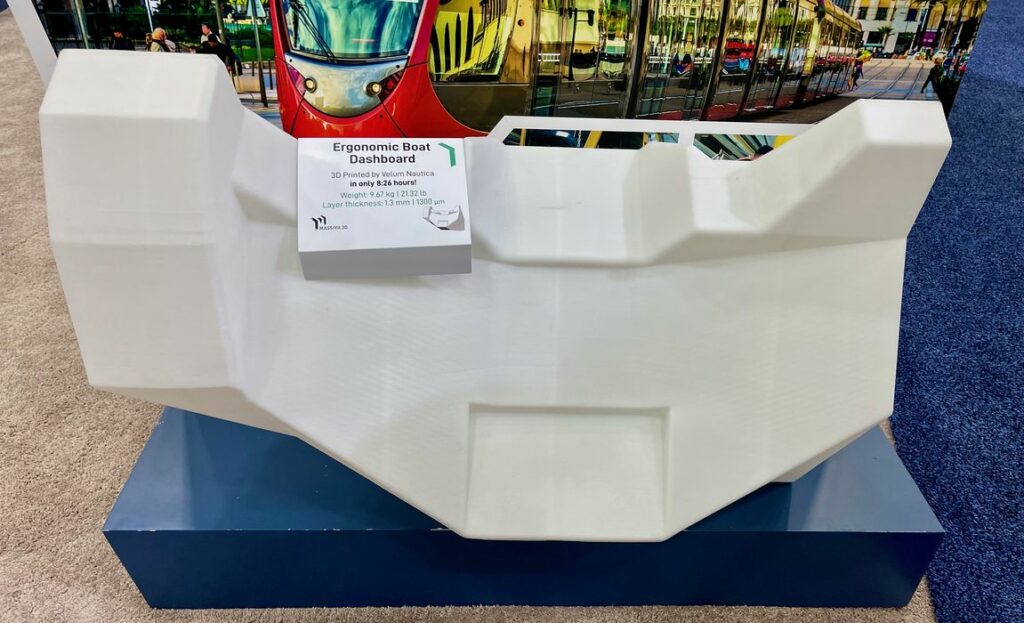
I had not encountered Massivit in person as they have not been attending 3D print industry tradeshows, instead focusing on print advertising tradeshows. This was the result of the company’s original focus on trade show signage as the key application for their large 3D printing process, and the fact that some of the company founders came from 2D print backgrounds.
This year they decided to appear at Rapid+TCT, where I spoke with the company’s President for North America, Kevin Sykes.
Sykes verified that while Massivit’s original market was advertising, things are now shifting towards industrial. Evidently their customers “began to invent things” with the large-format 3D printing capabilities of Massivit technology.
More recently things have shifted even more, mainly as a result of their recent announcement of CIM technology — “Cast In Motion”.
CIM is a unique technology and quite a bit different. The idea is to use the company’s gel extrusion tech to quickly print molds. Mold models for objects can be easily created through tools provided by Massivit, and then printed with CIM. As the mold is printed by one extruder, a second extruder fills the gap in the mold layer with a durable material. When complete, the mold can be dissolved with water as it is soluble, to reveal the molded object inside.
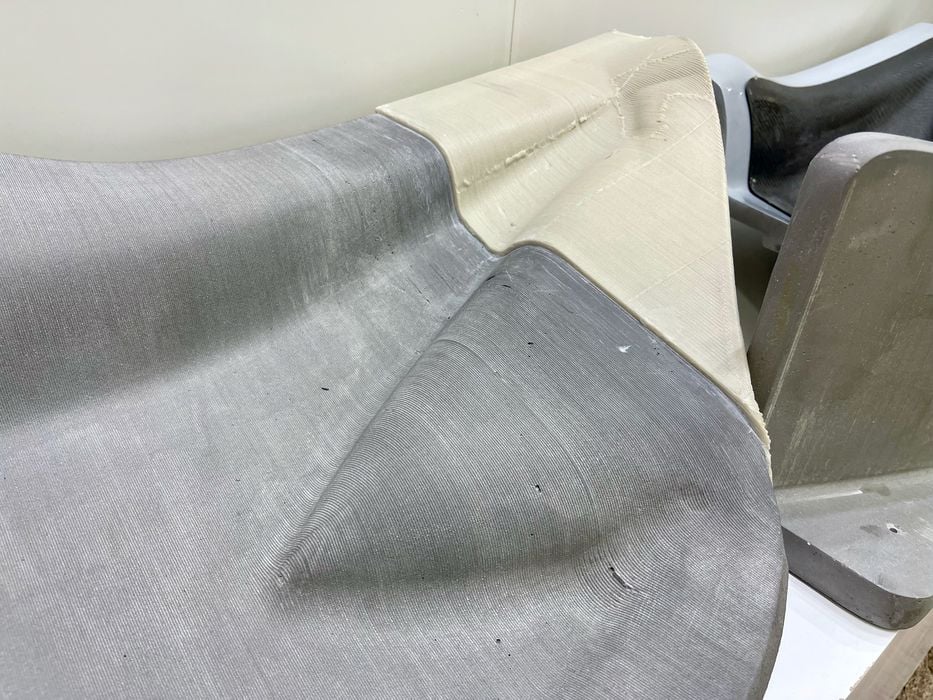
Sykes told us that they’ve seen “huge interest in the auto and marine markets”, where larger components are typical. Evidently the CIM process is quite a bit simpler than the typical 19 step process traditionally used to make such parts, and is therefore quite attractive to manufacturers.
Some statistics might persuade you of the incredible power of CIM. Skyes showed us a one meter base that was printed in only four hours.
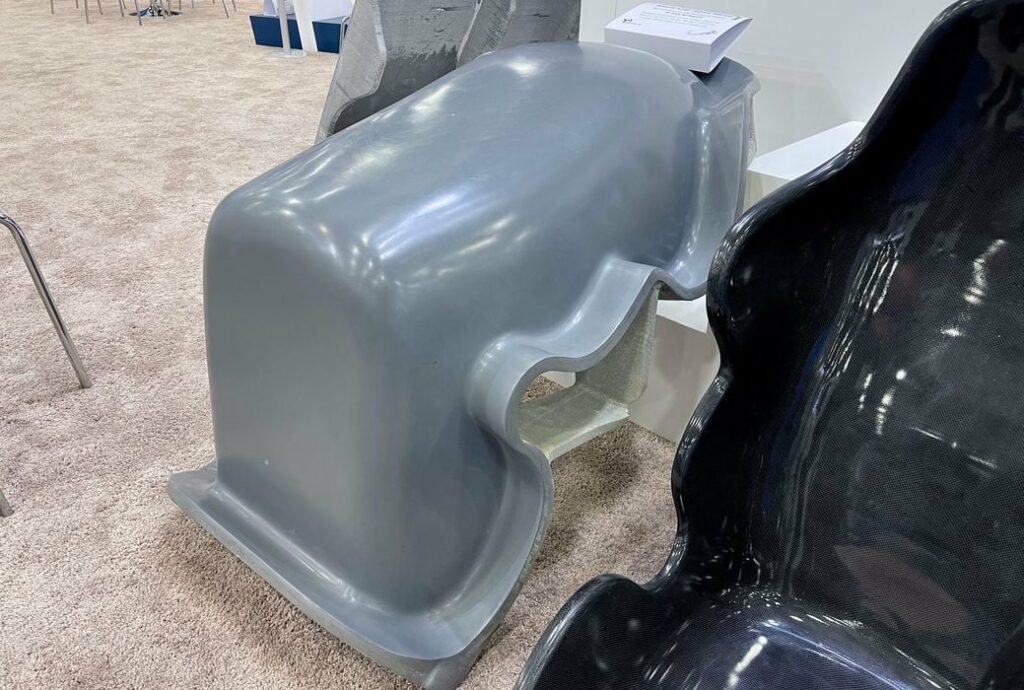
Or a full sized car seat that can be printed in only twelve hours. These are parts that on typical extrusion equipment could take days or even weeks to complete.
One question I had was regarding the surface quality of the prints, as CIM does produce layer lines on printed objects.
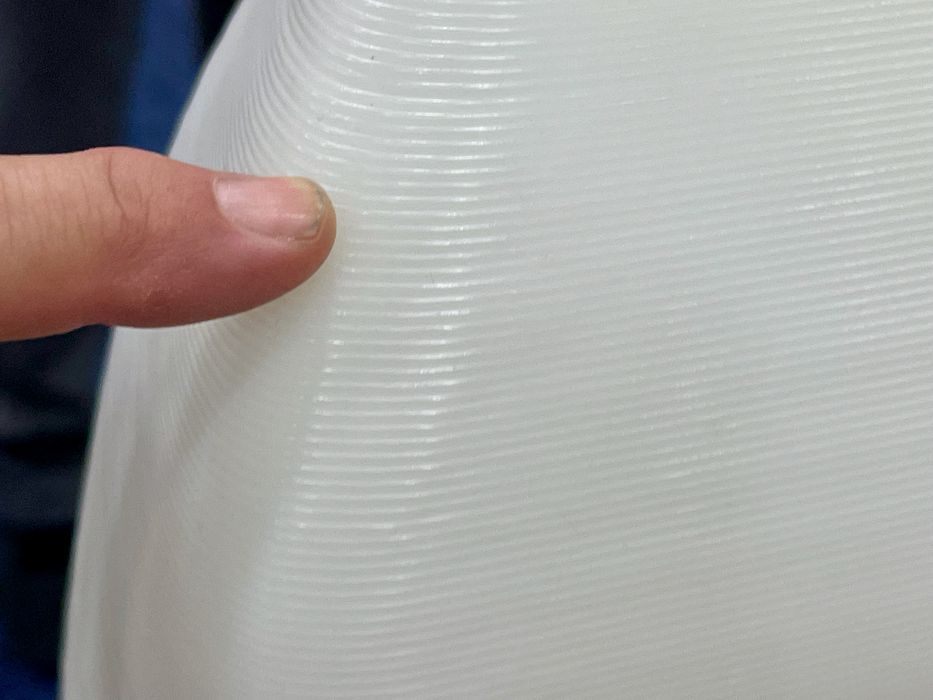
Skyes explained that CIM typically uses a 1.3mm layer size, and that they can go down as low as 0.5mm layers, but that could increase print duration.
Molded objects, once removed from the mold, do need to be sanded in a post processing step. However, even with that it is still possible to handily beat traditional molding processes.
Skyes said that currently the technology is being beta tested in both France and Michigan, so it’s likely we will see CIM technology gain broad access by customers in coming months.
CIM is an impressive technology, but will it catch on? Sykes thinks so, saying:
“The people in the molding space get it.”
Via Massivit