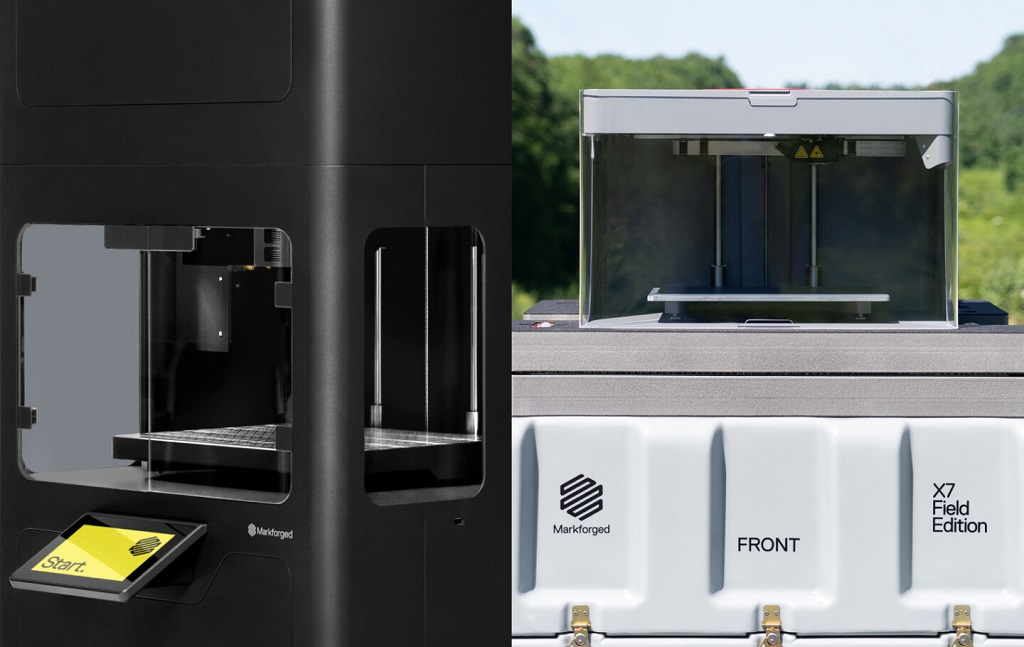
This week, Markforged announced new additions to its 3D printing platform.
Metal X Gen 2
Markforged introduced the Metal X 3D printer at CES 2017. While it’s been long enough now that that show’s no longer a go-to for major 3D printing introductions, it seems it’s also now time for a next generation of the company’s metal 3D printer.
That’s not to say there haven’t been notable updates along the way; the Metal X has seen significant milestones, including per Markforged:
- 2018:
- The first Metal X systems, comprised of the Metal X printer, Wash-1, and Sinter-1 came online. Metal X was capable of producing parts in 17-4PH stainless steel.
- Later in the year, H13 tool steel joined the materials lineup.
- Markforged University is chartered to teach DfAM for composites and metal.
- 2019:
- Inconel 625, A2 and D2 tool steels joined the materials lineup.
- Eiger gained options to print in solid fill and an ultrafine 50 micron layer height.Channeling the summer heat, we released the larger, faster Sinter-2 in July.
- As the weather gradually cooled in the fall, Sinter-1 also began gradually cool parts, as it learned to run an annealing cycle for H13, A2, and D2 tool steels.
- 2020:
- Pure Copper joins the materials lineup.
- New software features enabled leak resistance in 17-4PH, H13 and Copper. Print quality is improved through chamber temperature monitoring and gap-filling.
- Sinter-2 gained the Express Run capability, which shortened the cycle time for small parts to 17 hours.
- The print speed of rafts increase 2-3x, as a precursor to Next Day Metal.
With all of these updates, and notably the Sinter-2’s increased capacity, Markforged found that “the printer became the limiting factor on system productivity.” Early this year, the company introduced multi-printer bundles to address throughput.
To more fully address enhanced capabilities, though, and in tune with the new software update, the Metal X Gen 2 is now on the scene. New features include:
- An external seven-inch touchscreen, reducing hte risk of contact with moving or heated components
- Door position sensors that automatically pause active prints when the door is open
- Additional chamber insulation, shortening warm-up times and improving print consistency
The Metal X Gen 2 is available now.
Next Day Metal
The next generation of Markforged metal 3D printing is also made possible with Next Day Metal. This introduction is an over-the-air software update for the Digital Forge platform.
It is of course a combination of all elements of the additive manufacturing workflow coming together that unlocks potential, so it makes sense to see hardware and software rolling out together. Markforged says Next Day Metal, released across the full global fleet of metal 3D printer installations, will enable print speeds “up to twice as fast as before.” They also explain:
“Wash and dry times — an essential step in the metal 3D printing process — are now more accurate for smaller parts, shortening the required debind cycle time. These factors, combined with an approximately 17-hour small parts express run on the Sinter-2 post-processing oven, can give manufacturers the parts they need more quickly and — thanks to increased capacity on each printer — allows them to scale their additive manufacturing operation.”
Speed, accuracy, reliability: focus on critical factors that make real-world metal 3D printing not only possible but desirable is vital to the progress of tech adoption.
Bringing Next Day Metal into the real world already is Scottish service provider Angus 3D Solutions. The company requires tight clearances on parts and quick turnaround — making them a handy case study for the Next Day Metal introduction.
“The Metal X has been an important part of our business since we first began using it,” said Andy Simpson, Managing Director of Angus 3D Solutions. “Our customers rely on us to produce specialty parts that can be time-consuming to make and expensive to ship quickly. Our Markforged Metal X printer enables us to fulfill orders in a fast and timely fashion. Next Day Metal unlocks a new level of potential for us to scale our metal printing business and satisfy customer needs on even quicker turnarounds.”
Next Day Metal for both the Metal X Gen 1 and Gen 2 is available now.
X7 FE
Away from metals, Markforged is going rugged. With the X7 Field Edition, or X7 FE, 3D printer, the company is making in-the-field deployable 3D printing available.
The X7 3D printer, known as the model X until 2017, handles composite materials like Markforged’s Onyx material, as well as fiberglass and continuous carbon fiber. Now the X7 is going even tougher.
Ruggedized 3D printing has been seeing an increase in both interest and adoption as users such as in the military require specific parts in the field. Taking away the relatively clean convenience of a production facility certainly leads to issues in needing tough, all-in-one capabilities — and that’s what Markforged is addressing here. They explain:
“Moving beyond the factory floor, the X7 FE is a ruggedized, field-deployable industrial 3D printer for tactical response to inventory challenges in remote locations. Used by the U.S. Marine Corps XFAB program, the X7 FE is equipped with a rotomolded high-impact polyethylene Pelican case to protect it during transportation through harsh environments and contains all the tools, spare parts, and materials required for maintenance and repair operations in the field. Customers can drop the unit directly into harsh environments like combat zones and exploration sites and be printing in less than two minutes.”
The X7 FE is available for pre-order now, with shipping anticipated for this autumn.
Via Markforged