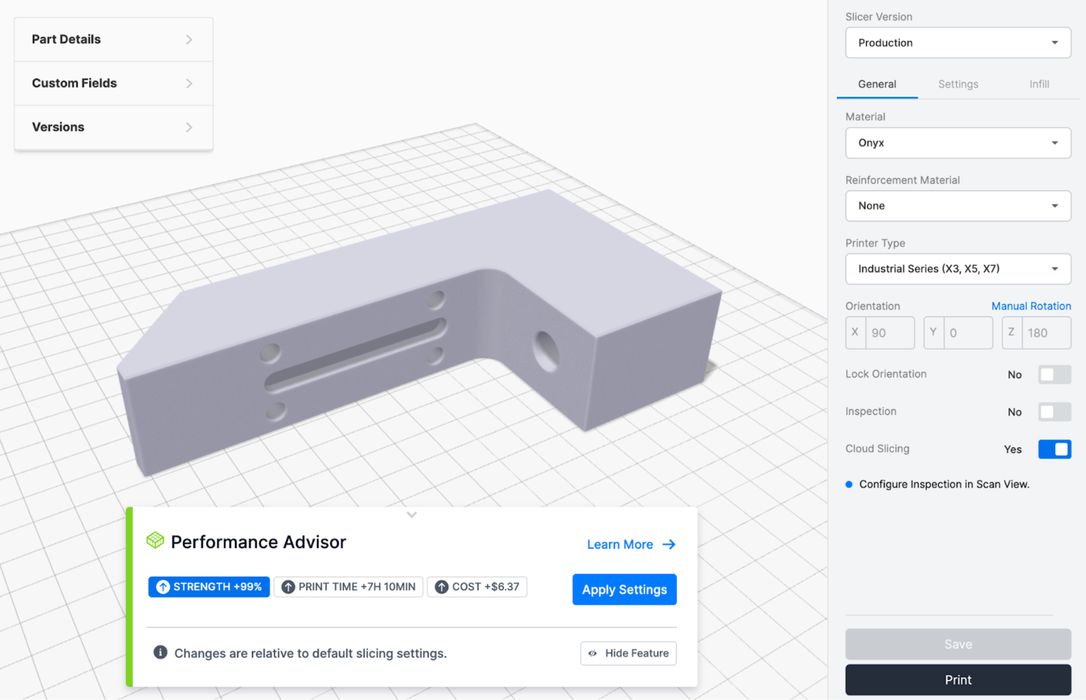
Markforged announced a new software tool that automatically makes parts stronger.
This is quite interesting, because Markforged’s equipment are known for already producing some of the strongest 3D printed parts. They accomplish this through the use of continuous carbon fiber, which is strung through parts to give them extra strength.
But that’s apparently not enough: now you can make them even stronger with something they call the “Performance Advisor”. It’s a new feature inside of their Eiger print management system.
Why make this an automatic feature? Aren’t the parts strong already? Markforged explains:
“The first step to manufacturing strong parts with Markforged printers is to configure print settings in Eiger. Several of these can influence the strength (performance) of a part, some more than others. For example, it is clear that adding continuous fiber reinforcement will make a part significantly stronger, but it is less clear what the impact will be when adding an extra wall layer or adjusting the fill density. Further, strong parts are desired but not at the expense of excessive increases in material cost and print time. Ultimately, the ideal print settings are those that result in a strong part that is manufactured efficiently – a part that balances strength improvements with minimal increases in cost and print time.”
So this feature is NOT simply pressing the pedal to the floor to make everything stronger. Instead it’s a more nuanced approach where the optimal print settings are automatically generated.
Hold on, how exactly do they do this? Normally the strength of an object is determined by running a simulation, and that requires someone to specify how the part will be used. How does Performance Advisor know this? Does it read minds?
The answer turns out to be quite interesting. The software uses “eigenmode” analysis. An eigenmode is a vibration mode of an oscillating system. The software identifies the lowest energy eigenmode of a part, and then examines which regions of the part that are “most susceptible to deformation”.
Having identified the weak regions of the part using this analysis, the software can then automatically beef up the print parameters to compensate. This is done using an AI procedure that balances strength, cost and print time.
Only the number of perimeters and roof/floor layers are adjusted during the process. The infill remains at default settings, as well as the infill pattern.
Performance Advisor would appear to be a pretty decent “one click” way to instantly strength 3D printed parts. However, that’s really for a generic situations. If you require specific strengths and attributes, then Markforged recommends using their simulation tool in the traditional manner.
Markforged provides Performance Advisor within their Digital Forge for subscribed users.
Via Markforged