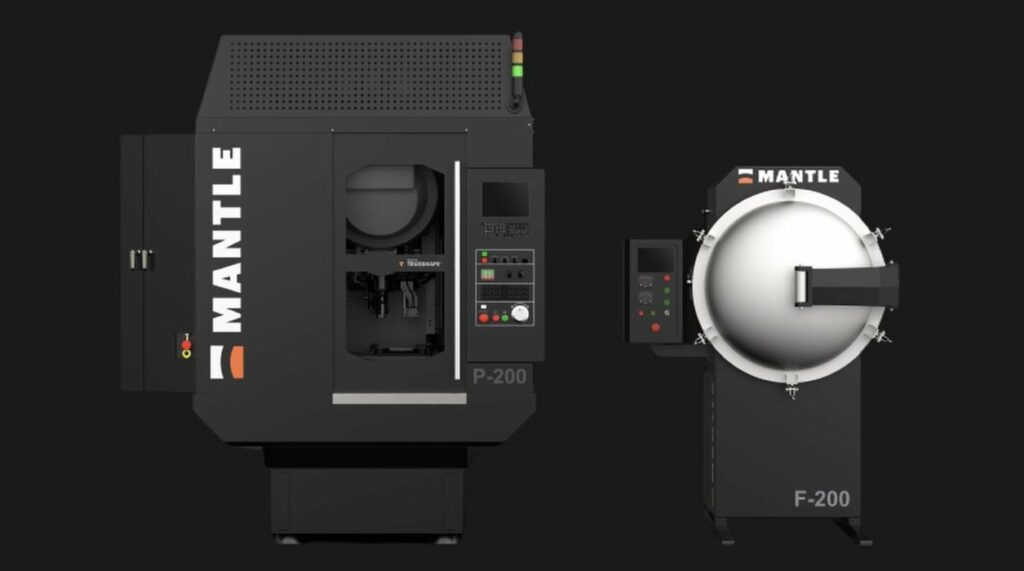
Mantle announced the availability of their first 3D printers.
The startup company only last year revealed their existence and hinted at their unusual printing process. Later, we learned more about their 3D printing process, which they call “TrueShape”.
In short, Mantle uses a paste extruder to precisely deposit a metal-rich layer. This is heated to remove binder and sinter the metal particles together, followed by a CNC milling action to smooth the surface. This repeats layer by layer until the object is built.
There are multiple benefits to this approach, but the most notable is that it completely negates the expensive requirements that come with the use of metal powder as seen in traditional LPBF systems. Those include air-tight rooms, powder handling systems, nitrogen or argon purging of build chambers, etc. In some cases the cost of the facility exceeds the cost of the LPBF machine!
None of that happens with paste as a material, as the metal cannot become airborne and is not exposed to oxygen. The paste system also permits high accuracy and precision, with the CNC component ensuring smooth surfaces.
Prints made with TrueShape are not complete and must undergo a sintering process to remove the binder used during printing to hold everything together. The sintering process also fuses the metal particles together to form the final object.
The news is that the first TrueShape 3D printer has been released, along with an accessory sintering furnace. The printer is the P-200, and (obviously) the F-200 is the furnace.
The P-200 has a respectable build volume of 200 x 200 x 150 mm, which should be sufficient to address a large part of the company’s target market: tool makers.
Manufacturing tools are currently an underserved market, as the iterative and rapid use of tools in manufacturing is not particularly compatible with the expensive LPBF metal 3D print world. In many cases the manufacturer cannot afford that technology, but here Mantle hopes to fill that gap with the P-200.
The idea is the Mantle system can produce tools with the right quality in only four steps in 2-4 weeks, as compared to twelve steps and twelve weeks typically for conventional tooling methods. The Mantle process is also faster than some alternative 3D printing sequences that involve as many as ten steps and even more weeks to complete.
To help that movement, Mantle has certified two very hard tool steels, H13 and P2X, for use in the P-200. These should be ideal for tools that must withstand repeated use, but at the same can be produced at the touch of a button by line personnel.
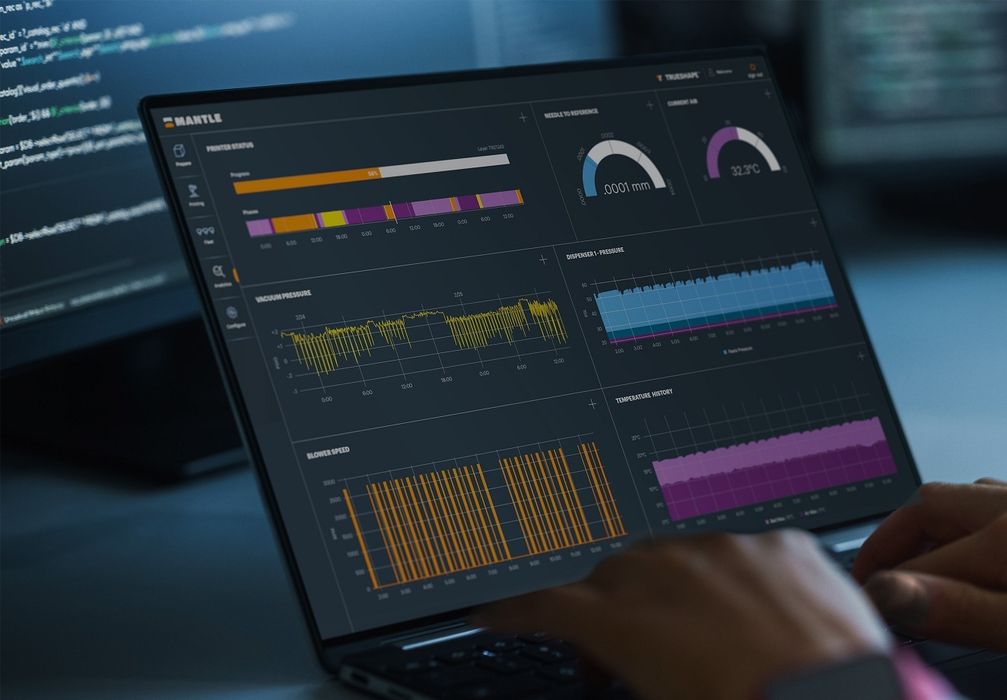
It seems that Mantle has addressed the client needs not only through hardware, but also through software. The Mantle software computes not only the 3D print sequence, but also the CNC milling required for the object. This treats the tool creation as a single process, which results in a near-perfect part in the right kind of material.
The Mantle software provides remote management, as well as using information provided from “over 20” different sensors in the P-200.
I’m quite interested to see how the tooling industry receives this new technology, as it is a very large market. It seems to have the right attributes to be a winner, and the next few years will determine Mantle’s success.
Via Mantle