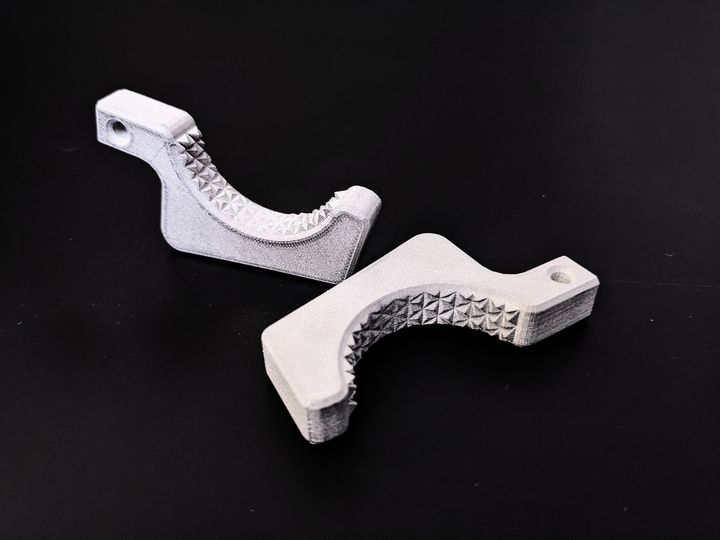
MakerBot announced a new way to 3D print metal on their equipment.
The company has been around a long time — since 2009 — and in all that time has made 3D printers capable of only 3D printing in polymers. First ABS, then PLA, and more recently a series of experimental materials using a more advanced nozzle system on their popular METHOD system.
MakerBot Experimental Extruders
The Experimental Extruder has been quite a feature for the METHOD, as it allows the use of higher-temperature and abrasive composite materials. For many 3D printer operators, those engineering materials are a requirement for their applications.
MakerBot has since embarked on a partner program for materials. In this program materials makers work with MakerBot to certify use of their materials on the METHOD, and at the same time dial-in the optimal print parameters. These are then provided to METHOD operators for painless and quick 3D printing.
MakerBot Ultrafuse
As of now there are dozens of materials in MakerBot’s certified list, including many popular engineering materials. However, there’s now a new one that is different from all of the others: BASF Ultrafuse 316L Stainless Steel.
This is a composite filament that’s made from a combination of polymer and 316L stainless steel powder. It prints in a similar manner to any other filament — although it is abrasive to the nozzle due to the presence of steel particles that pass through. However, the magic happens after printing.
The resulting part is a fragile mix of polymer and steel powder. It’s then possible to put the part through a post-printing process to first remove the polymer binder, and then secondly sinter the metal powder together into a solid object. The result is a near-pure metal part, although slightly smaller due to the loss of the polymer during debinding. MakerBot explains:
“Once the part is printed with BASF Forward AM Ultrafuse 316L, it can then move on to the next press of debinding and sintering, which turns the part printed with the composite material into solid stainless steel. This process allows users to create stainless steel parts without investing in pricey debinding and sintering equipment. Final parts can achieve up to 96% of the density of pure 316L metal material. Users can produce lightweight, hollow metal parts with high tensile strength compared to polymers that would be difficult to produce in other ways.”
In other words, you can 3D print a metal object on your MakerBot METHOD!
This process requires debinding and sintering equipment, which most METHOD operators likely don’t happen to have in their workshop. MakerBot is aware of that and has figured out a very easy-to-use solution.
They’ve partnered with MatterHackers to provide expertise and services for the Ultrafuse material. This includes special a build plate adhesion solution, design guidelines and most importantly, post-print debinding and sintering services. You can buy “processing tickets” from MatterHackers; these allow you to send your “green” parts to them to put through the post-processing sequence.
You could, of course, do this on your own, but there’s a catch: the debinding and sintering processes themselves need to be precisely applied to obtain optimal results. You’d have to perform a number of experiments to figure this out yourself, or more simply go ahead with MatterHacker processing tickets.
Either way, you end up with metal 3D prints that would otherwise cost far more than using conventional metal 3D printing services.
Via MakerBot