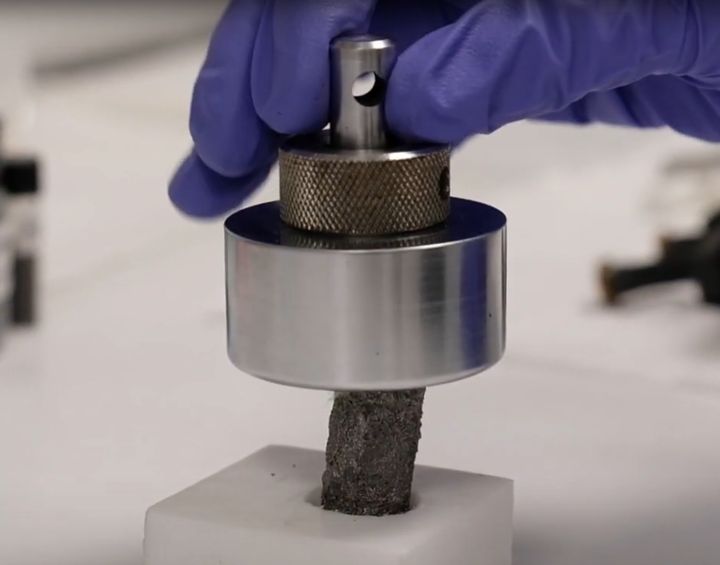
Researchers at Nanyang Technological University in Singapore have developed a new type of adhesive that could lead to a different form of 3D printing.
Magnetocuring
The new process, called “magnetocuring”, overcomes several problems associated with existing export adhesives. Typical adhesives we see today involve mixing two chemicals, or exposure to heat, light or air.
There are several problems with these adhesives that become apparent when they’re used in a variety of industrial and environmental situations.
For example, adhesives applied to the soles of shoes are difficult to heat up for curing because the shoe materials insulate against heat penetration. This implies the shoe must be heated for longer durations, leading to less efficient production.
Use of adhesives outdoors in unusual weather can also cause problems with adhesive curing.
The new research involves the development of a new type of adhesive that includes a specific mix of manganese, zinc and iron nanoparticles. By exposing the adhesive to a magnetic field, these nanoparticles quickly heat up and create sufficient warmth to cure the adhesive.
This eliminates the need for curing ovens, as a manufacturing line would simply have to expose the production units to the alternating magnetic field as they pass by. Not only is this far faster, but it also requires far less energy (by 120X !) than would be required by ovens. It also applies heat only in positions where it is required, thus reducing damage to other parts.
There’s some interesting possibilities, as Professor Raju V. Ramanujan explains:
“The speed and temperature of curing can be adjusted, so manufacturers of existing products could redesign or improve their existing manufacturing methods. For example, instead of applying glue and curing it part by part in a conventional assembly line, the new process could be to pre-apply glue on all the parts and then cure them as they move along the conveyor chain. Without ovens, it would lead to much less downtime and more efficient production.”
MagnetoPrinting?
I think there could be another possibility for this technology: 3D printing.
Imagine a configuration like this:
A paste extruder pushes a thin stream through a nozzle to selectively deposit material on a layer pattern. A magnetic field is present during extrusion, causing freshly extruded material to quickly cure.
This approach would use a lot less energy than FFF devices that must heat their hot ends as high as 450C. It might also provide a greater degree of inter-layer bonding.
However, there would certainly be challenges.
Adhesives on their own are not particularly strong materials. It’s likely the chemistry would have to be changed to provide strength, perhaps with the addition of fibers.
Flow considerations are significant. This approach would not work if the adhesive could not easily be pushed through an extruder, nor if it prematurely cured in the extrusion system, creating perhaps the worst jam imaginable.
There’s no way the NTU adhesive could be directly used for 3D printing, but their approach definitely suggests an alternative form of 3D printing using magnetic fields.
This should be investigated further, if it isn’t already being done.
Via NTU