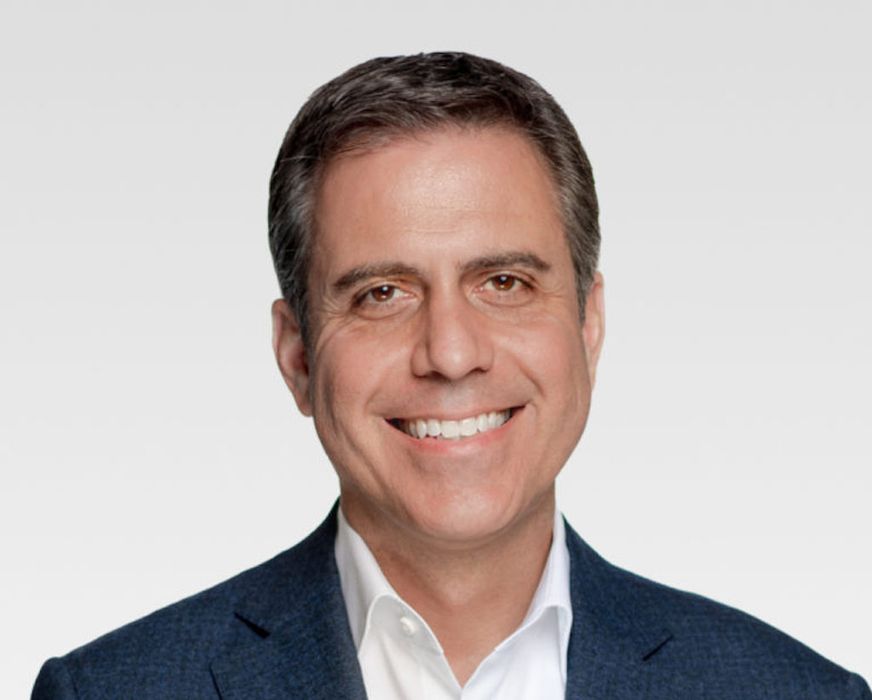
The Fast Radius co-founder offers advice on tackling manufacturing challenges through the adoption of Industry 4.0 technologies.
Manufacturing is having a moment, and sophisticated technologies like additive manufacturing are predicted to grow over the next decade. With innovation accelerating in machines, materials and processes, it can be challenging for companies to figure out where to begin when modernizing their manufacturing infrastructure.
Fast Radius is one company that’s helping manufacturers embrace new technologies by providing access to its cloud manufacturing platform. Engineering.com sat down with Lou Rassey, Fast Radius co-founder and CEO, to discuss factors driving the future competitiveness of manufacturing in the U.S.
Engineering.com: Could you start off by introducing yourself and how you came to your current role?
Lou Rassey: I am one of the co-founders and CEO of Fast Radius. I’m a third-generation manufacturing guy from Detroit originally. My grandfather started a machine shop when he was very young. My dad is still running it today. I grew up around that business and really it inspired in me an appreciation for the beauty and importance of manufacturing as an industry.
That led me to be a mechanical engineer by trade. I started my career with Chrysler and the automobile industry as an engineer for designing power trains and body systems, and then designed and launched a factory down in Brazil for a couple of years—a joint venture between Chrysler and BMW. Then went on to graduate school in engineering and business in MIT, where I was a part of a Leaders for Manufacturing fellowship program, continuing my lifelong passion for innovation in the industrial world.
I went on to McKinsey, where I was for almost 12 years. I helped to build what is now the Industry 4.0 practice at McKinsey. A part of the work that I led there was a global effort looking at the future of manufacturing, where it’s going and what it means for how companies and countries are going to compete in this century and in the digital age. I had the privilege of working with public and private sector leaders on these topics and really it inspired me and a couple of my co-founders to branch out. We started a company, and we have been building and scaling Fast Radius now for over five years.
Where do you see gaps in the marketplace right now? What do you think engineers and manufacturers are struggling with?
There are widespread and common challenges in today’s supply chains and in the manufacturing industry. The infrastructure to make and move things is very rigid, wasteful and outdated. I think over the last few decades, supply chains have been built to allow low-cost, high-volume production with very long and complex supply lines that served us well for a good stretch of time. But as we look at the needs today for more flexible manufacturing—more local manufacturing—and the ability to embrace new technologies like industrial-grade additive manufacturing, the manufacturing infrastructure that the world has built over the last couple of decades is not meeting the needs of our time, and is not embracing Industry 4.0 technologies broadly.
What is the state of 3D printing right now as a true production technology?
I think additive manufacturing has proven itself to be a technology that can be used in demanding applications at value. We see applications with parts in automobiles, medical devices, airplanes and consumer products, whether it is Adidas shoes or Rawlings baseball gloves. Additive manufacturing over the last few years has really proven itself to be a technology that can be used in volume production—and there’s cause for excitement about what that means. It means the materials are meeting production standards, means the repeatability and reliability of the equipment. It means that the economics are making sense for volume production. But it’s still in the very early days of adoption. I think we’re seeing companies starting to embrace it, and that’s giving confidence for others to embrace it.
Now, the industry still has a ways to go. Costs need to come down for materials and equipment for the market to embrace the technologies more aggressively—but we’re seeing progress from the materials makers and the equipment providers year-on-year and expect that to continue. And as those costs improve, it will make an even stronger business case for more and more applications.
How do you believe U.S.-based manufacturers can get started with 3D printing?
First, find an opportunity where it can create value in your business. It could be customized manufacturing for products that are unique to specific customers. We see that a lot in medical applications, such as dental and orthotic applications.
The business case for additive manufacturing is most powerful when you are making geometries that are difficult or impossible to make with other technologies like injection molding, where you can consolidate 5-10 parts into a single component, removing assembly and design complexity. Or it could be low-volume production where you don’t have to have the expense of making an injection mold, but you can produce an additively manufactured part directly that gets you to market faster and reduces CapEx requirements. Or it could be for critical spares that are needed to be produced with a higher velocity fulfillment for critical spare parts. Or entirely new-to-market products that are uniquely enabled by 3D printing.
For all of those reasons, additive can create real tangible business value. The first step for manufacturers is to understand and identify an opportunity where the technology could be embraced, and I think the second is to know that you don’t have to do it alone. There’s a misperception that you have to go out and buy these machines yourself and set up a new industrial additive factory. For some companies where they have a clear business case, that’s a good thing that they can do. But for many, they just don’t know where to get started. What materials, what technologies, how to build an industrial-grade factory. There are partners out there that can help provide access to these tools, and start driving impact quickly to get the flywheel going for your business.
How much should a company expect to spend to get into this? Are we talking $50,000? Half a million?
It can start with early experimentation where you are getting additively manufactured parts made using partners that can help educate you on what’s possible. It could be $1000 for a sample part that you can then test and evaluate. You can scale up there once you find the business case and the part application that is making sense.
I think what’s so powerful about digital manufacturing broadly, including additive manufacturing, is that you don’t have to invest in the CapEx yourself to get started. There are ways of getting started with very minimal capital requirements, and really just starting the learning journey and the experimentation.
What goes into making parts that pass certification specifically for highly regulated industries like automotive, aerospace, healthcare?
The quality and performance standards for additive manufacturing have to meet the same bar as traditional technologies like molding or machining. Now, there are unique elements for additive manufacturing that are a part of the quality system that companies will audit and evaluate as they’re adopting the technologies.
We’re not cutting any corners by embracing additive manufacturing over alternative technologies. Additive manufacturing can meet and in some cases exceed the performance of other technologies for reliability, repeatability and scalability. But the unique elements for additive manufacturing include the need for process capabilities that some companies just are unfamiliar with. Many manufacturers have to learn for the first time and go through those process capability studies to understand what is possible, and to do the validation of the machines and materials. That is one of the key steps to getting comfortable with a technology at scale.
How is embracing additive manufacturing a way to onshore and combat global supply chain strains?
Additive manufacturing can help to create a much more sustainable and lower carbon footprint supply chain. It really cuts across the lifecycle of designing, making and moving products.
At the design stage, additive manufacturing allows engineers to produce more efficient designs with lower weight and less material, allowing them to reduce the carbon impact of products that are being brought to the world.
Read more at ENGINEERING.com