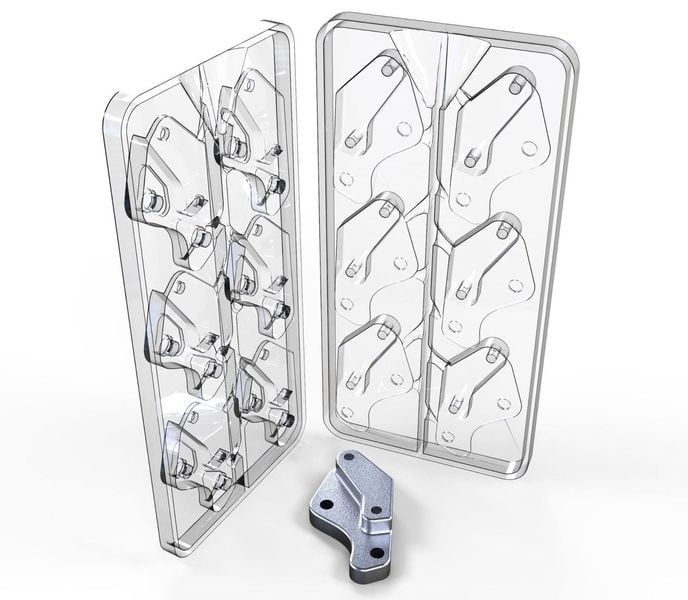
Janne Kyttanen’s 3D printed popsicle process is a lot more powerful than I realized.
The long-time 3D print designer and entrepreneur is a co-founder of 3DTI, a very unusual 3D print company. That’s not unusual for Kyttanen, who has been in our pages many times, mostly for his radical concepts that inspired many early trends in 3D print design.
3DTI began as (and still is) a popsicle company. They devised an unusual manufacturing process involving 3D printing to produce custom-designed Pixsweet popsicles, called “Lost Air Casting”. Here’s a video showing how this process works:
It is ingenious, yet straightforward: a design is used to generate a mold, which is then 3D printed. The mold then helps form the corresponding 3D shape in a polymer film, much like you’d do with a vacuum former. Finally the popsicle liquid is squirted into this custom mold.
And voila, you have popsicles of any geometry you can devise.
It’s a great concept, but now it turns out there’s a simpler variation that could provide for far easier metal production. But how does it work?
Metal Lost Air Casting
Most of the process is the same: a polymer film mold is produced. However, you’d think the polymer would instantaneously vaporize upon exposure to hot, liquid metal. That’s what would happen, but there’s now an extra step in the process to avoid that unfortunate result.
The polymer film is coated with ceramics! Kyttanen explains:
“In a nutshell, you first create a 3D printed mold in 2, 3 or 4 directions, you then use that mold for creating a thermoformed 100-200 micron thick polystyrene air pocket. You then dip the air pocket in a ceramic shell slurry and voila.”
The ceramic is well-able to withstand the temperatures of metal casting, so this approach can clearly work. In fact, the image at top shows an example of how the Lost Air Casting method was used to produce a metal part — or several.
Kyttanen says the Lost Air Casting process can operate quite rapidly. He says:
“We can process any liquid, paste, gel or powder type substance in super high velocity. With velocities, I mean 1 second per product or 0.1 second per product, depending what we are making and what the speed requirements are.”
That injection might be a bit more tricky when handling high-temperature liquid metals, but the point remains: the Lost Air Casting process should be quite rapid and scalable to high volumes.
Of course, since this is casting there will be some constraints on the geometry of the made parts, since it’s really conventional casting at that point. Nevertheless, there is a significant advantage to Lost Air Casting.
That advantage is that the mold is incredibly lightweight: it’s a film with a thin layer of ceramic overtop. This is quite different from the massively heavy ceramic or sand molds typically used in metal casting. Kyttanen wants to rid the world of the need to move these massive molds with forklifts.
It’s not clear how large parts can be made with this process, but it seems scalable to me, so long as the ceramic layer is sufficiently thick to handle the weight of the casting. But that’s just details, as the process has been proven: Kyttanen says they’ve already produced many metal parts with the Lost Air Casting process.
It appears that Kyttanen is looking for those interested in trying out this new metal production process. If you’re up for an interesting experiment, please contact 3DTI.