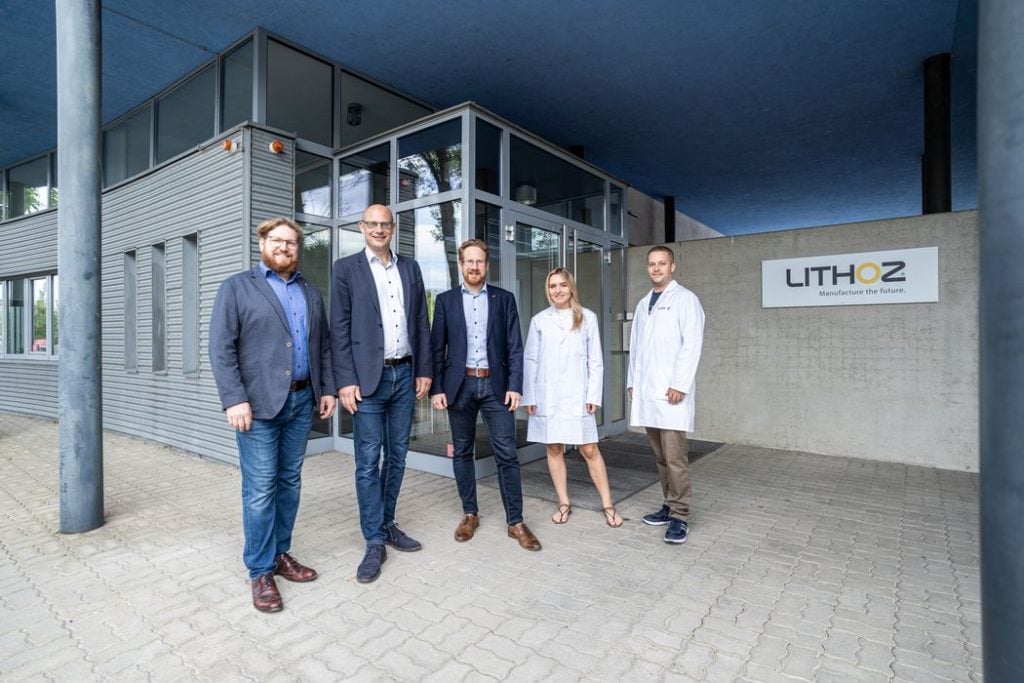
Lithoz announced an expansion, but what does this really mean?
The Vienna-based company is one of the very few that produce 3D printers capable of making ceramics. Specifically, their equipment makes small, high-resolution ceramic objects.
Currently they market the CeraFab line of 3D printers, which is comprised of four different units. There are options for entry-level lab work with the L30, as well as modular systems that can scale up for production. One machine offers a unique multi-material capability, and another is targeted at the healthcare industry.
Ceramics are an interesting material for 3D printing, as they offer engineering properties vastly different than typical polymers or metals used in most 3D printing systems.
Ceramic material can be quite hard and rigid, and is electrically non-conductive. It is also extremely heat resistant, more than can be found with most metals.
This makes ceramics an incredibly useful material for specific applications. Electric applications could be a big user of this material, leveraging the insulative effects of ceramics.
But CeraFab faced the same problem that many other 3D printer manufacturers have gone through: it’s a new material to industry, and few know how to leverage it.
To be clear, ceramics have been used for decades, perhaps centuries, in industry. It’s a well-known material. However, it’s always been used for products made using traditional making techniques.
To properly leverage the new capabilities of 3D printing, users would have to design parts with geometries not easily accomplished with traditional techniques.
That’s a very hard thing to do for many industries that have been doing essentially the same processes for many years. Part designers would have to think outside the box to come up with new solutions that would not only leverage the 3D print capabilities, but also provide some type of competitive advantage over existing parts.
When early polymer and metal 3D printers were rolled into sites, it was initially expected that the users would simply know how to do all this. That was not the case. Decades of experience and training with older methods usually results in replication of existing designs, which are typically more expensive to produce using 3D printing. Thus there isn’t a business case to proceed if doing it that way.
This challenge faced those selling polymer 3D printers, metal 3D printers and silicone 3D printers. Most certainly Lithoz faces the same barriers to adoption, and perhaps that’s one reason why there aren’t that many ceramic 3D printer options these days.
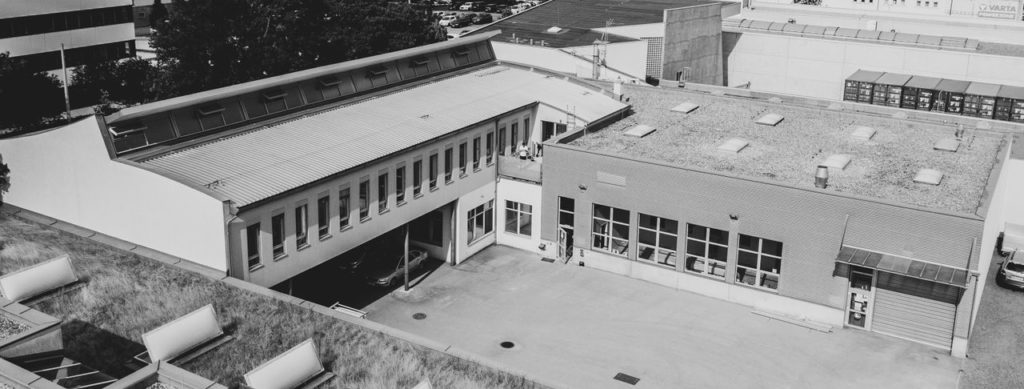
However, today we have a new clue about this scenario. Lithoz announced the opening of a fourth location after their first office in Vienna, a second in New York and a third in Shanghai. The new office is also located in Vienna, but in a separate location from headquarters.
Here’s the interesting part. Lithoz explained:
“Lithoz’s new site offers more than 2200 m2 of additional space for the production of machines and materials. Cutting-edge manufacturing solutions embedded in a GMP compliant infrastructure will allow Lithoz to meet even the highest standards of their industrial and medical customers, while a quality management system according to ISO 13485 and FDA (21 CFR part 820) ensures top product quality from development through to production and final delivery to the customer.”
Evidently this new office will be used to produce parts using the CeraFab equipment for clients. That tells me a few things.
First, there is increasing demand for ceramic 3D prints. So much that Lithoz has invested in opening and equipping a large (2200sm / 24000sf) secondary manufacturing facility. That’s good news for Lithoz and indeed for any other party making ceramic gear.
This likely means that there are increasing numbers of companies that have been “activated” into ceramic 3D printing, and are able to design unique and revolutionary parts using the technology.
It may be that Lithoz has passed one of the major barriers to 3D print growth.
Via Lithoz