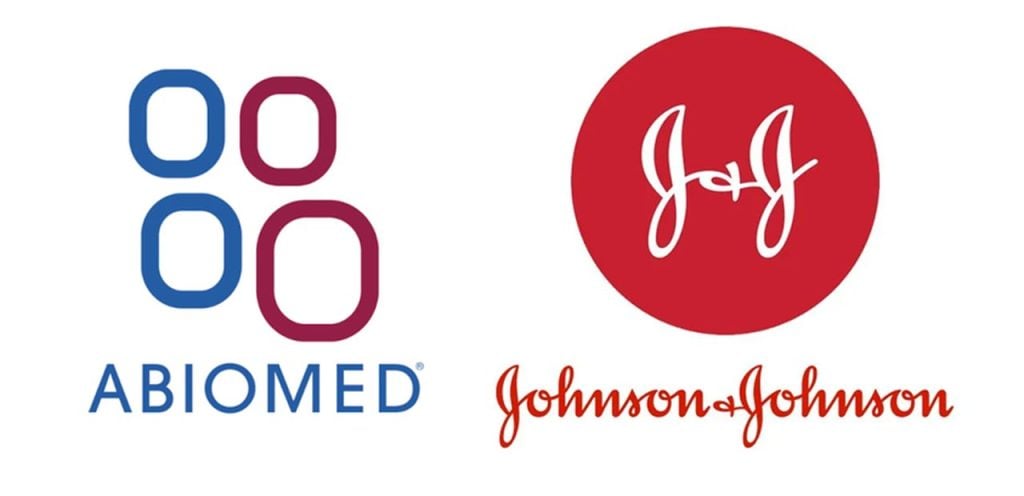
Charles R. Goulding and Preeti Sulibhavi suggest increased use of 3D printing Johnson & Johnson.
Johnson & Johnson recently announced the acquisition of Abiomed for US$16.6B. Abiomed is a leading, first-to-market provider of cardiovascular medical technology with a first-in-kind portfolio for the treatment of coronary artery disease, heart failure and a pipeline of life-saving technologies including the Impella CP heart pump. The acquisition broadens the company’s position as a cardiovascular innovator.
J&J is the world’s largest health care company with 142,000 employees and annual revenue of US$93.78B for 2021. We have previously written about the 3D printing implications of the Johnson & Johnson split. We discussed J&J exiting its consumer product business segment.
Abiomed’s tiny heart pump, allows patients undergoing cardiovascular procedures to have higher flows while maintaining access to the arteriotomy.
The ability to maintain access to the arteriotomy is particularly vital to the care of patients supported by the Impella device in an intensive care unit (ICU) long-term, such as those in cardiogenic shock. In addition, the Impella CP third-generation heart pump offers fewer steps when flushing the system as part of standard maintenance.
3D Printing and the Medtech Industry
The medtech industry is replete with examples of 3D printing’s ability to improve the design, structure, and flexibility of medical device products. For example, we have recently written about how human digital twinning impacts medical 3D printing.
The various components of the Impella heart pump can potentially be 3D printed as well (see diagram above). Abiomed’s heart pump is still in the clinical trial phase, which are expected to be completed between 2023 through 2026.
J&J’s 3D printing ecosystem includes its 3D Printing Center of Excellence. A significant (Medtech was about 27% in 2020) portion of Johnson & Johnson’s business comes from the medical devices and equipment it produces for the world’s healthcare organizations, and one of its greatest challenges comes when providing artificial body parts which are designed to replace the real thing in living bodies. J&J has found that 3D printing is one important solution.
“To make products now, we have large factories that require a significant investment,” said Joseph Sendra, Global Vice President for Manufacturing, Engineering and Technology at Johnson & Johnson. “With 3D printing, we can potentially move manufacturing to a very small footprint, doing the same thing closer to the customer. That means products do not need to be shipped as far, and there’s a faster turnaround.”
J&J is using 3D printing technologically across many of its diverse business segments. Beyond medtech, J&J’s Neutrogena brand, which is part of the consumer business that is being spun-off, is exploring the use of 3D printing to create personalized 3D skincare masks.
Beyond fabrication of medical devices, 3D printing has gotten so advanced that scientists have found ways to use 3D printing to patch existing heart tissue while patients remain on heart transplant waiting lists or even to remove the need for the transplant itself.
Scientists at Tel Aviv University in Israel have designed a groundbreaking approach that enables them to create an artificial heart using bioink and 3D printing. Their first step was to take a biopsy of fatty tissue from the patient. Then, they separated cellular material from noncellular material.
The researchers subsequently reprogrammed the cells of the fatty tissue to become pluripotent stem cells, which can develop into the range of cell types necessary to grow a heart.
The noncellular material consists of structural components, such as glycoproteins and collagen; the scientists modified these to turn them into a “bioink.” Bioink is used in bioprinting, essentially the 3D printing of tissue constructs.
The researchers then mixed this bioink with the stem cells. The cells differentiated into cardiac or endothelial cells (which line blood vessels), which the scientists could use to create cardiac patches, including blood vessels.
The Research & Development Tax Credit
The now permanent Research and Development (R&D) Tax Credit is available for companies developing new or improved products, processes and/or software.
3D printing can help boost a company’s R&D Tax Credits. Wages for technical employees creating, testing and revising 3D printed prototypes can be included as a percentage of eligible time spent for the R&D Tax Credit. Similarly, when used as a method of improving a process, time spent integrating 3D printing hardware and software counts as an eligible activity. Lastly, when used for modeling and preproduction, the costs of filaments consumed during the development process may also be recovered.
Whether it is used for creating and testing prototypes or for final production, 3D printing is a great indicator that R&D Credit eligible activities are taking place. Companies implementing this technology at any point should consider taking advantage of R&D Tax Credits.
The “Heart” of it All
At its core, the acquisition of Abiomed by J&J, is a stepping stone for the health product giant to improve its med-tech business segment. Both J&J and Abiomed can benefit from this acquisition J&J’s established protocols and procedures for 3D printing in its divisions may well be applicable to Abiomed as well.