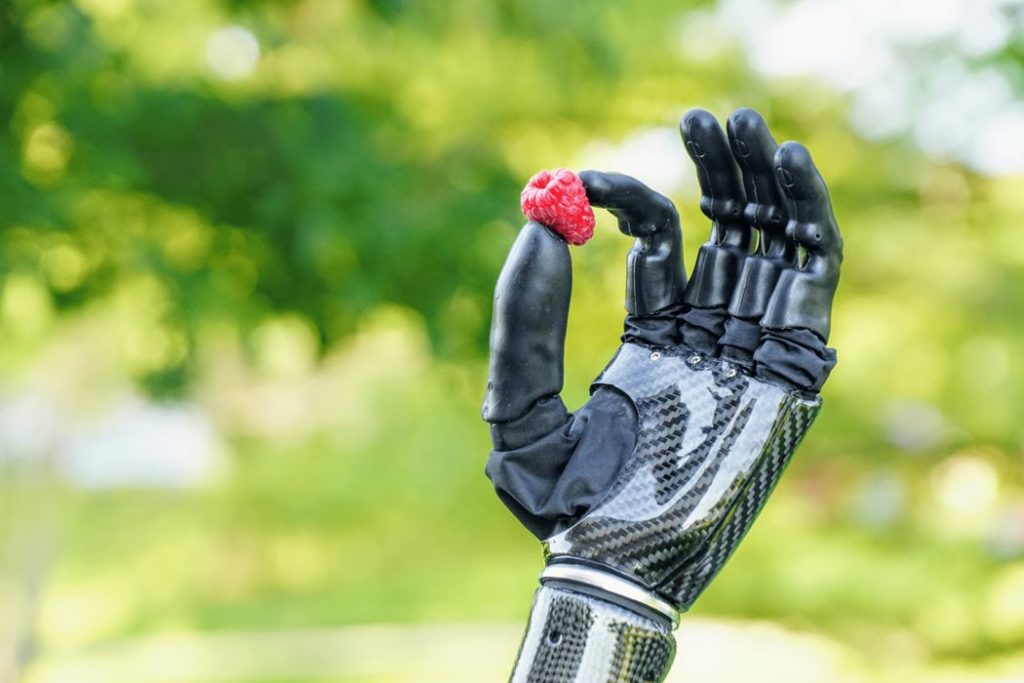
A start-up company, Psyonic, recently released the Ability Hand, a 3D-printed limb with touch-sensing capabilities.
In the United States, nearly 2 million people live with a limb difference. With the aid of prosthetics, many patients can extend their range of motion and improve their everyday quality of life. Unfortunately, modern prosthetic technology can be prohibitively expensive, especially for a custom device that is designed specifically for the patient. With the widespread adoption of 3D printing, many physicians and patients are excited by the prospect of 3D-printed prosthetics to improve access to custom, affordable devices.
To meet this demand, many companies are developing 3D-printed limbs for a diversity of indications. An Illinois-based start-up called Psyonic is looking to stand out with its touch-sensing capabilities and tough, durable device. In September 2021, the company released its first prosthetic, the Affinity Hand, a multi-articulated limb available in the United States and covered under Medicare.
The Ability Hand is made from silicone and rubber to minimize costs and increase functionality. Unlike traditional prosthetics made from plastic, wood or metal, a limb made of silicone and rubber is more resilient to everyday wear and tear. If a patient were to fall or hit their limb against an object, it is no longer susceptible to snapping from such random events—a significant inconvenience for current prosthetic users.
An Affordable, Touch-Sensing Prosthetic
The Ability Hand is a multi-articulated prosthetic designed to be more user-friendly. The goal of the design was to allow patients to receive touch-based feedback to improve the functionality and longevity of the limb. Currently, most prosthetics do not deliver tactile feedback, making it complicated to maneuver a device without damaging items. Instead, the Ability Hand uses six different pressure sensors in each finger to send vibrations to the user that mimic the sense of touch. The vibrations indicate when someone has touched an item and with how much force. This lets users gently grip something like food or firmly grip breakable objects like a ceramic mug. The overall process more closely mimics biological hand movement and improves the functionality of the limb relative to traditional prosthetics.
Aadeel Akhtar, founder of Psyonic, explained: “When approaching a problem like this, usually people go either super cheap and not functional, or very expensive and highly functional. We wanted something that is the best of both worlds.”
The Ability Hand’s fingers are made of rubber and silicone to further improve the limb’s grip capabilities. All five fingers can flex and extend, the thumb rotates, and the hand includes a full range of motion. The prosthetic can also respond quickly to the user, as the fingers can close in 0.2 seconds, reducing latency or delays that impact functionality. The entire limb is powered by brushless DC motors, commonly used in drone technology.
“We wanted a fully 3D-printed limb to start,” said Akhtar. “We talked with more than one hundred clinicians and patients and learned that even the most expensive limbs were breaking from random use. Plastic components would frequently snap if a patient fell.”
In designing its 3D-printed prosthetic, the Psyonic team wanted to ensure that the final product would be able to withstand daily use and the random accidents that can occur in everyday life. Currently, the device is 3D printed and features carbon fiber to strengthen each prosthetic component. The company 3D prints molds to generate the parts of the hand using low-cost silicone and rubber. Most of the 3D printing process remains proprietary, but the final device is water resistant up to the wrist and is custom built to a patient’s specifications. To ensure that a patient can readily use their device and its associated app, the limb features USB-C fast charging to allow the prosthetic to be fully charged in one hour.
The prosthetic is operated by the user through one of two methods. First, the patient or a physician can manipulate the hand and modify its grip using a mobile app, communicating with the device via Bluetooth. Second, patients can undergo targeted muscle reinnervation (TMR) surgery to rewire the nerves above the elbow that would typically connect to the wrist and instead connect them to existing muscles. These rewired muscles can then control the prosthetic, including opening and closing the hand, making a fist, or using any of the 32 grips made possible with the device. The company is continuing to add grip configurations into the software.
The Ability Hand was also designed to support further research and development.
“We have an API for researchers to evaluate torque, velocity, and position control over all the motors and sensors using either a wired or Bluetooth connection,” said Akhtar.
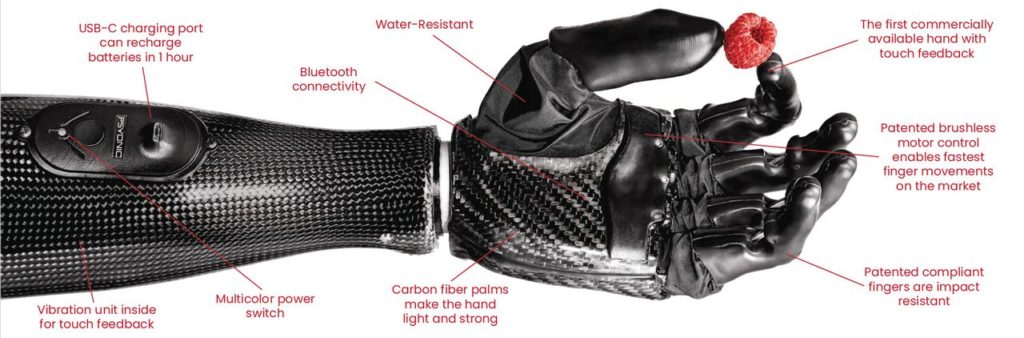
An app is available for both clinicians and patients to control the prosthetic grips and get real-time feedback from the device. The goal is to accelerate research in artificial limb development and support the further advancement of the technology.
The Story of Psyonic
Psyonic was founded by Akhtar to realize his lifelong goal of expanding access to 3D-printed prosthetics. Akhtar’s initial inspiration came when he was seven years old, visiting Pakistan with his family. During their trip, Akhtar met someone with a limb difference for the first time—a young girl. Unfortunately, the girl and her family could not afford a prosthetic, and Akhtar decided that he would commit to one day developing an affordable artificial limb.
The research that led to the creation of the Ability Hand began during Akhtar’s Ph.D. work. As part of his graduate studies, Akhtar and another student, Mary Nguyen, partnered with the Range of Motion Project to test the prototype of the Ability Hand in Quito, Ecuador. Using the device, a patient there, Juan Suquillo, could pinch his thumb and forefinger together for the first time in 35 years. Witnessing this powerful experience encouraged Akhtar to dedicate his life to developing and expanding this technology.
Read more at ENGINEERING.com