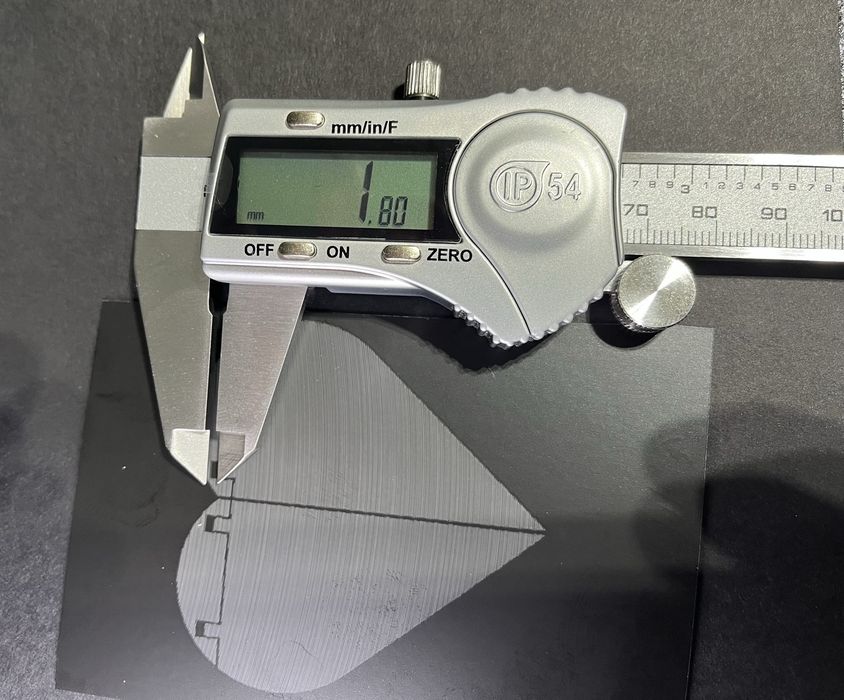
We’ve learned more about Tecnica’s upcoming powder-sintering 3D printer that is very different from existing SLS technology.
Existing SLS systems normally use a fixed laser and a tilting galvanometric mirror to direct the laser beam across the print surface. This works, but is complicated by the beam “dot” becoming misshapen as the angle of reflection increases. This also changes the energy per area, resulting in inconsistent print quality.
Examining the HDLS Optical System
Tecnica’s solution, called “HDLS” (High Definition Selective Laser Sintering), involves a rotating mirror combined with a very complex stationary mirror. This video shows how it works:
The mirror’s geometry is designed to ensure the laser dot is perfectly consistent over the entire print surface, solving the problems found with galvanometric solutions. This means that not only part quality is assured, but also part dimensions. HDLS also can run faster and with more power than typical SLS systems.
Tecnica founder Charles Bibas told us they are able to achieve IT Grade 13 on HDLS prints.
Understanding IT Grade 13 Accuracy
Note: “IT Grade” is a standard for linear dimension tolerances. IT Grade 13, for example, would mean a tolerance of less than 0.54mm on a 100mm dimension.
Bibas pointed out to us that no one else in the industry even publishes this type of specification, which tells you something about the accuracy of 3D printing equipment in general.
You’ll note the mirror configuration does not include any lenses, which are often used in typical LPBF systems to correct for the dot distortion. This means that the laser energy travels in “pure” state all the way to the material, providing more energy.
Tecnica’s Cost-Efficient Mirror Manufacturing Process
The question that’s been circling is the nature of this complex stationary mirror: how expensive could it be to make? I’m reminded of an old construction maxim: “curves cost money”. If expensive, then HDLS equipment could be priced out of the market.
It turns out Tecnica now has an answer to this question, as they’ve now patented a process to manufacture these complex mirrors that is very cost efficient. Bibas said:
“I can reveal that the mirrors are made with a turning machine and not in free form (expensive to manufacture). This means that the cost is manageable and comparable to less expensive than a Galvanometer based system.”
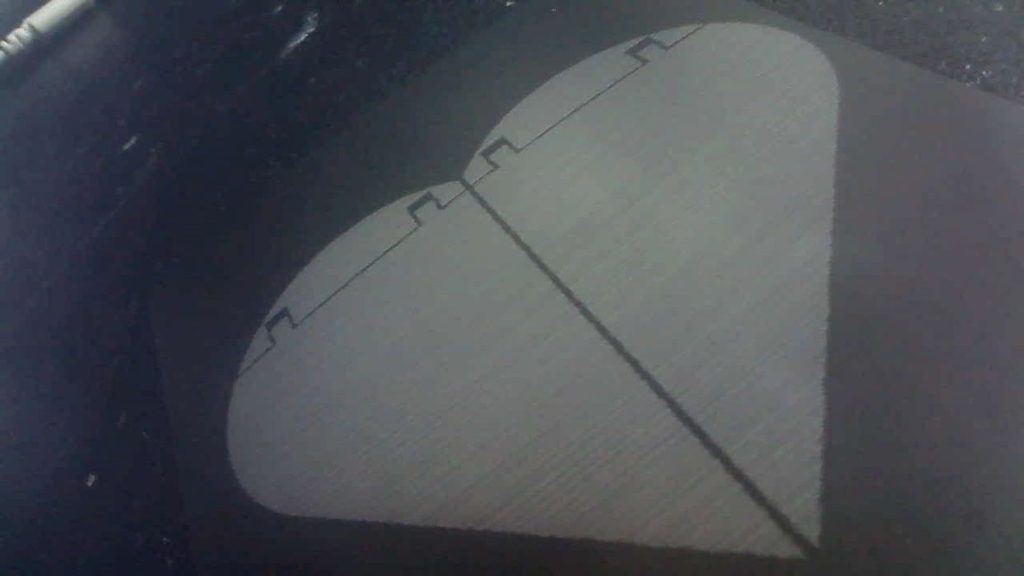
The HDLS process does work, as you can see in the images presented here from Tecnica.
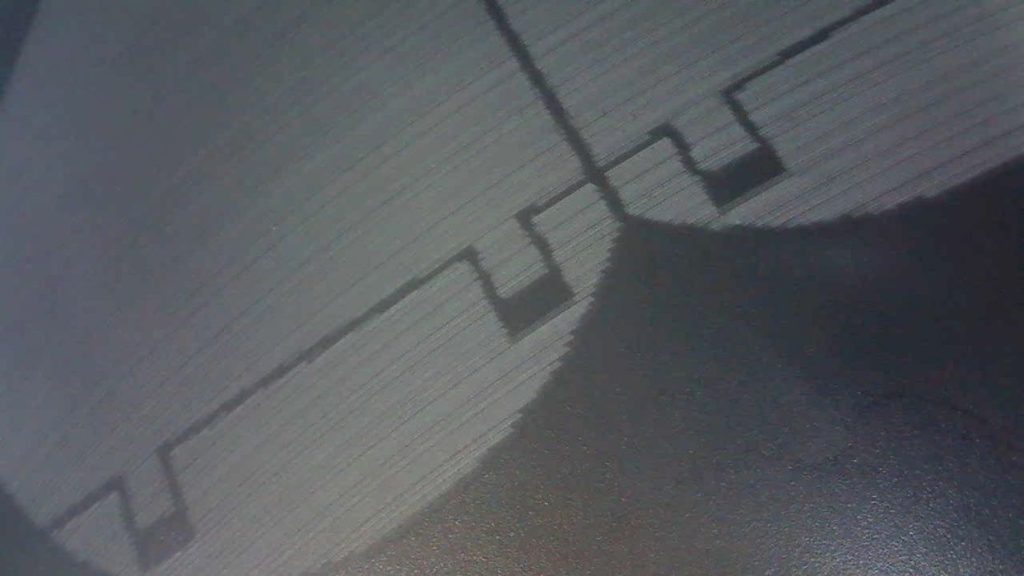
Evidently the nature of HDLS means HDLS printing is quite tolerant of machine geometry and less dependent on the optics. This suggests the equipment will be relatively easy to maintain.
The CASA II & CASA II Pro 3D Printers
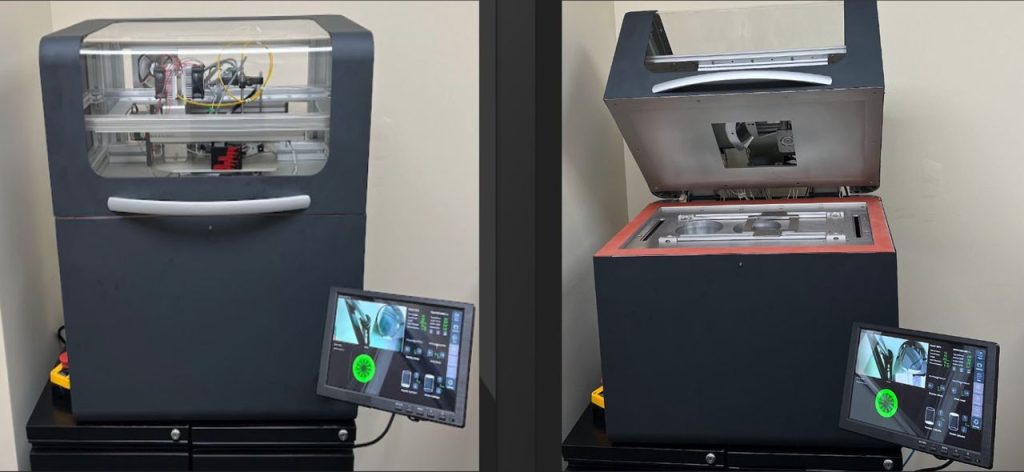
Tecnica plans to market two HDLS machines, the CASA II and CASA II Pro, for smaller applications. Later, they might follow on with a much larger device for industrial use. Apparently the CASA II is “ready for production” already.
So far, the company is self-funded, and they’ve come quite a way without the need for external investors. It’s not clear when, precisely, they will be launching these machines, but I’m hoping it’s soon as they could revolutionize SLS 3D printing.
Via Tecnica