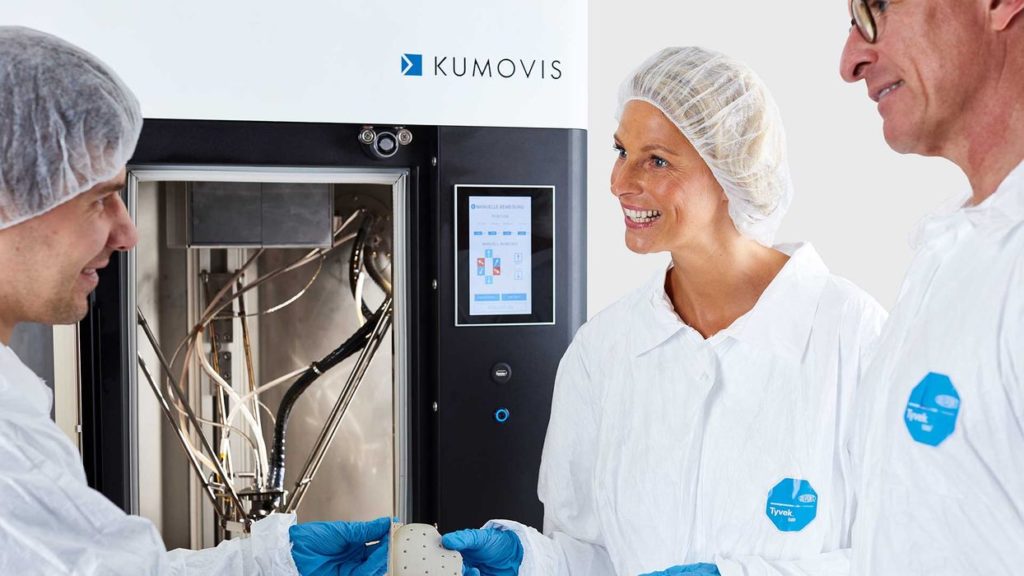
Kumovis announced a new workflow for the production of certified medical products.
The Munich-based med-tech startup offers a 3D printer specialized for the healthcare sector, able to 3D print in a variety of end-use production materials, including PEEK, PPSU, PEI, or PEKK.
But having a 3D printer is not the complete answer for medical product manufacturers. There is a notable lifecycle required to produce devices that can be certified by regulators for use in the healthcare industry. Developing this lifecycle might be considered a barrier for those companies and startups considering the production of medical devices.
That barrier could change with the introduction of Kumovis’ new end-to-end workflow for medical 3D printing.
I reached out to Kumovis to find out more details of this workflow.
Fabbaloo: Is this an entirely new workflow, as in Kumovis has not previously provided one?
Kumovis: Two years ago, Kumovis brought to the market a 3D printing system specifically developed for medical applications. Based on our technology and our solution-oriented approach to work with customers, we are now offering the complete workflow for certain applications, i.e. implant manufacturing for cranioplasty.
It’s the first time Kumovis offers the complete package for particular applications, incl. 3D printing and post-processing hardware, monitoring software, and regulatory data such as machine qualification as well as biological and mechanical validation. We help manufacturers serve the FDA market and pave the regulatory pathway to smoothly release 3D printed implants to the market.
It is nevertheless not an entirely new workflow in general at Kumovis as we have been working with partners on different applications using (parts of) the workflow for years. It’s one new end-to-end workflow for cranial implant manufacturing now, but many solutions using the workflow to come.
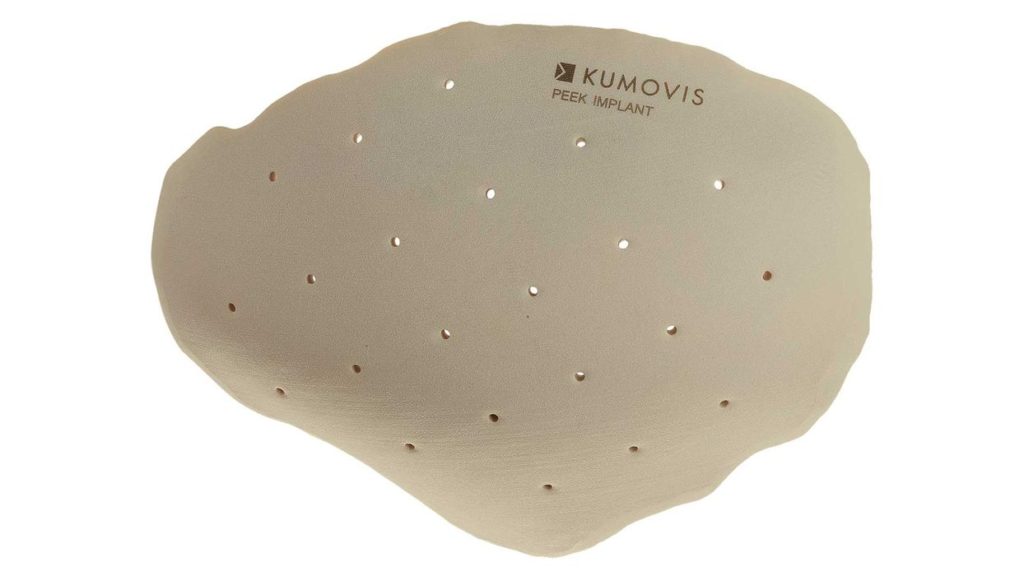
Fabbaloo: What capabilities are made possible with the workflow?
Kumovis: Stakeholders in medical 3D printing request clarity on regulatory frameworks, processes, and quality management. Kumovis has developed this workflow to meet these challenges. Medtech companies and hospitals that apply this new framework will benefit from high patient satisfaction, gained efficiencies and cost savings, despite regulatory challenges. One of our first applications is individualized cranial implants.
Fabbaloo: At a high level what are the steps of the workflow?
Kumovis: The most relevant steps of the workflow are: Software-guided data pre-processing, the 3D printing process itself, guided post-processing strategy as well as certain data to meet regulatory requirements. This includes build orientation, support generation as well as 3D printing parameters for medical-grade polymers and operating procedures for post-processing. And what is more, specific regulatory data such as mechanical and biological validation.
Fabbaloo: Does the workflow integrate with other software tools? Or is it an end-to-end solution itself?
Kumovis: Our workflow integrates with existing implant design software. Thus, we combine established software with Kumovis-specific solutions. If a customer is already used to certain design software, it is usually possible to integrate with this design tool. However, we do have our best-practice approaches to provide customers with an optimized and holistic workflow.
You might have noticed a theme running through these answers: make life easier for medical product manufacturers. The best way to ensure something happens is to remove all possible friction, and that seems to be the design goal of Kumovis’ new workflow.
Via Kumovis