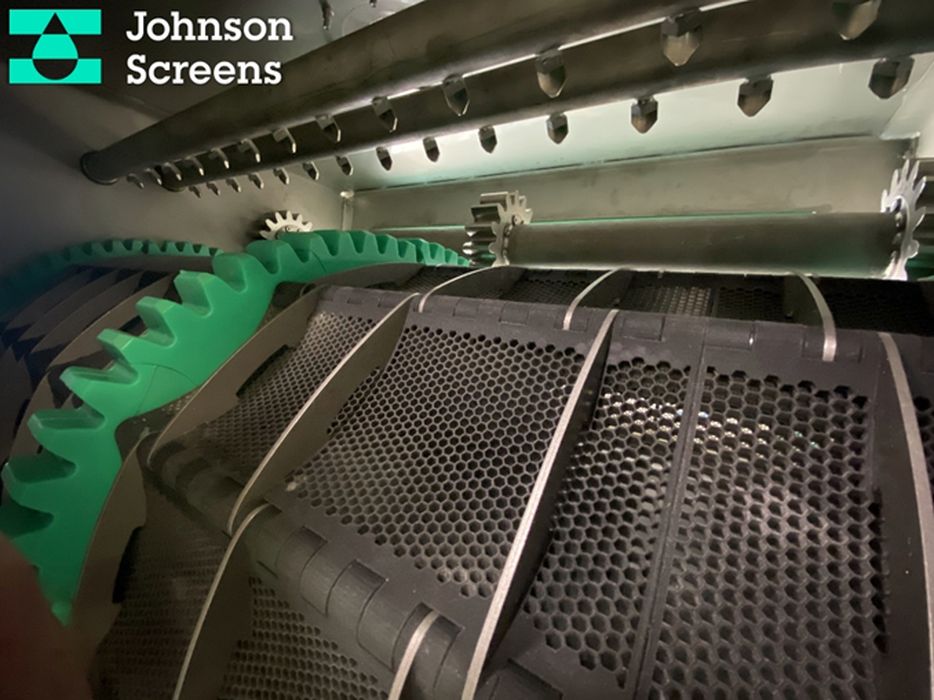
Charles R. Goulding and Andressa Bonafe admire Johnson Screens’ willingness to rethink fabrication and experiment with additive manufacturing.
With nearly 120 years of operation, Johnson Screens, a brand of Aqseptence Group, is present in 100 countries and 6 continents. The provider of screening and auxiliary solutions supports a wide range of industries, including environmental, energy, chemicals, food and beverage, and mining. Though often invisible, Johnson Screens’ highly-engineered and precisely-fabricated products are all around us, from water well screens to architectural finishes.
Johnson Screens’ core Vee-Wire® product offers liquid/solid and gas/solid separation. The stainless-steel filter has found successful applications in filtering, media retention, sizing, dewatering, classifying, among many others. Traditionally, Vee-Wire® screens have been made by a continuous welding method in which the company’s’ patented V-shaped wire is engineered into various sizes and shapes, including cylinders, flat and curved panels, cones, etc. This production method has allowed for design flexibility while meeting high standards of ruggedness, durability, and resistance to abrasion.
3D Printing and Screen Manufacturing
Aiming to optimize production, Johnson Screens has recently incorporated 3D printing technology in its long-standing fabrication processes. The company has taken advantage of additive manufacturing as a means to achieve a variety of designs while minimizing the amount of material required. Finding adequate material, however, was a challenging task due to the restrictions of working with water and other liquids, which require resilient, non-absorbent properties. After considering alternatives and deciding to work with polypropylene, Johnson Screens performed a series of tests that ultimately revealed the superiority of 3D-printed components.
Fully aware of the challenges of serving highly-demanding, non-stop industries, such as wastewater treatment, Johnson Screens decided to partner with HP and leverage its unique portfolio of products. This partnership allows for quick and continuous fabrication of additive-derived components, which have so far zero recorded failures in testing and limited commercial use.
Johnson Screens’ openness to rethink fabrication processes and incorporate additive manufacturing should serve as inspiration to other companies that aim to take innovation a step further. The tax credit opportunity described below can help them do so.
The Research & Development Tax Credit
The now permanent Research and Development (R&D) Tax Credit is available for companies developing new or improved products, processes and/or software.
3D printing can help boost a company’s R&D Tax Credits. Wages for technical employees creating, testing and revising 3D printed prototypes can be included as a percentage of eligible time spent for the R&D Tax Credit. Similarly, when used as a method of improving a process, time spent integrating 3D printing hardware and software counts as an eligible activity. Lastly, when used for modeling and preproduction, the costs of filaments consumed during the development process may also be recovered.
Whether it is used for creating and testing prototypes or for final production, 3D printing is a great indicator that R&D Credit-eligible activities are taking place. Companies implementing this technology at any point should consider taking advantage of R&D Tax Credits.
Conclusion
With over a century of experience in screen manufacturing, Johnson Screens has begun to rethink fabrication processes to include 3D printing technology. This type of commitment to innovation should serve as inspiration to other companies who can take advantage of R&D tax credits to support their innovative efforts.