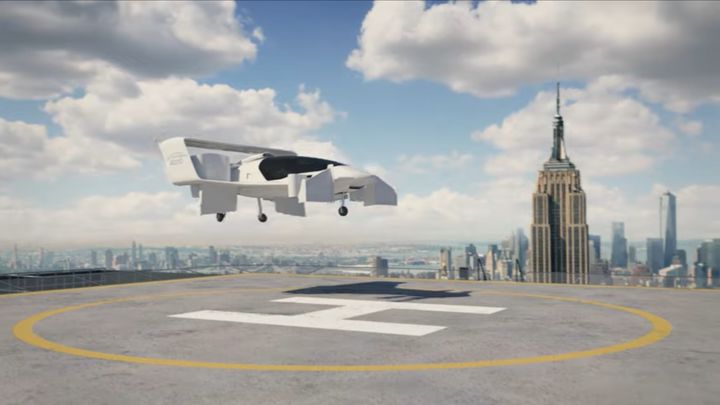
A startup company has leveraged 3D printing technology to produce a revolutionary new approach to aircraft propulsion.
You might say I’m a bit of an aerospace tech buff, and you’d be correct. I like to follow developments in the industry and there have been plenty in the past few years.
One that I’ve recently encountered is a revolutionary new propulsion system from a Washington state-based startup company called Jetoptera.
No doubt you haven’t heard of them yet, as they have a long way to go to finalize their product. It’s an entirely new way to push aircraft through the sky using a technique they call “fluidic propulsion”.
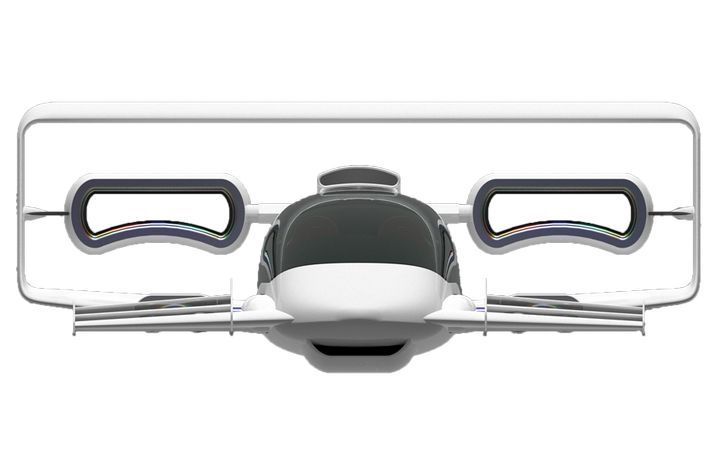
It’s not a jet, and there are no propellors visible in the Jetoptera aircraft. The boxy wing design wraps around the fuselage in a way that doesn’t seem to make any sense.
But in reality, it does make sense. The fluidic propulsion system is essentially a scaled up version of the well-known Dyson bladeless fan. A compressor pushes air through the “thruster”, which is specially shaped to funnel the airflow in the most efficient manner.
The concept was developed by aerospace engineer Andrei Evulet, who first experimented with the concept in his own driveway. Evulet 3D printed
200 concept models to understand the optimal flow designs, and then set upon scaling up the system to build a VTOL (vertical take off and landing) craft.
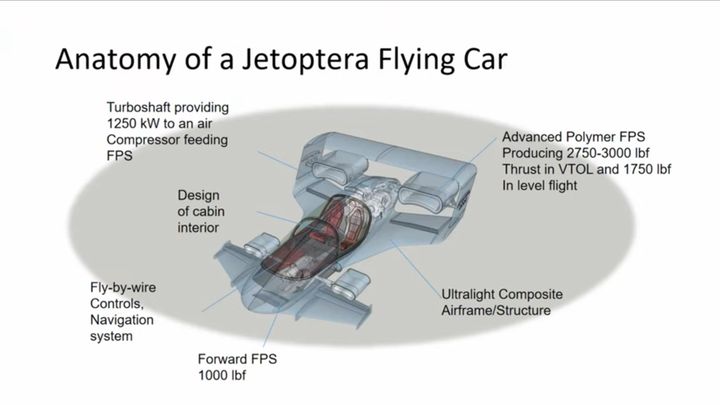
His motivation was triggered by seeing the actually severe limitations of today’s air travel: we are constrained to use large commercial aircraft through hubs, even though we most likely want to go somewhere else. We need to use airports because today’s aircraft technology requires massive runways.
The VTOL concept allows inexpensive point-to-point travel, and it doesn’t even require airports. You can literally land anywhere.
And by “anywhere”, I really mean anywhere! If you consider helicopters, today’s go-to vehicle for point-to-point travel, they are actually quite restricted in where they can travel due to their rotating blades. They cannot go near wires, between trees, etc., for fear of catching on to something and destroying the vehicle.
The Jetoptera concept doesn’t use blades, and as long as the vehicle can physically fit into a space, it can go there. This will be vastly more useful than helicopters.
And it could finally, at long last, enable the true development of actual flying cars.
There are a ton of other advantages to fluidic propulsion:
- Much faster horizontal speeds over helicopters
- Ten percent more efficient propulsion than current methods
- Half the fuel/energy consumption
- 30% less weight
- Significantly less complexity — NO moving parts!
- Ability to easily switch from jet fuel to batteries when energy density is sufficient
Evulet describes his journey and the concept in his recent TEDx talk:
Today the company produces a variety of fluidic propulsion vehicles (some are drones), and hopes to build flying cars in the near future using the technology. Of course, they use additive manufacturing techniques to create many of the aircraft components.
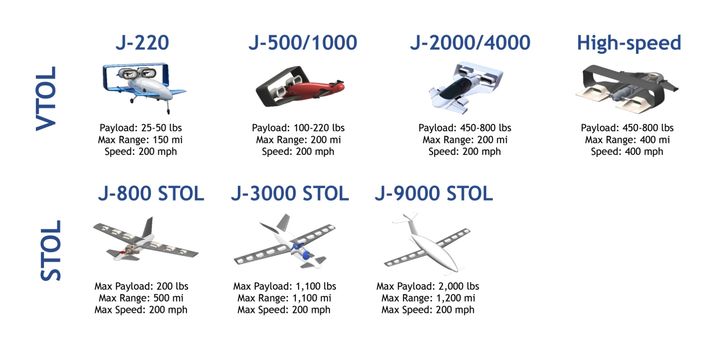
It’s a grand story and one that should lead to flying electric cars at some point in the future. This is how I envisioned the 21st century unfolding, but it’s just happening a bit slower than I imagined.
Stepping back a bit, we can see that this entire venture was enabled by the presence of 3D print technology. The prototypes were made with 3D printing, and the production vehicles will be made with 3D printing technology.
3D printing is clearly shaping the 21st century, providing a platform to develop products and services that could not have been imagined in years past.
Well, except for that flying car I’m still waiting for.
Via Jetoptera