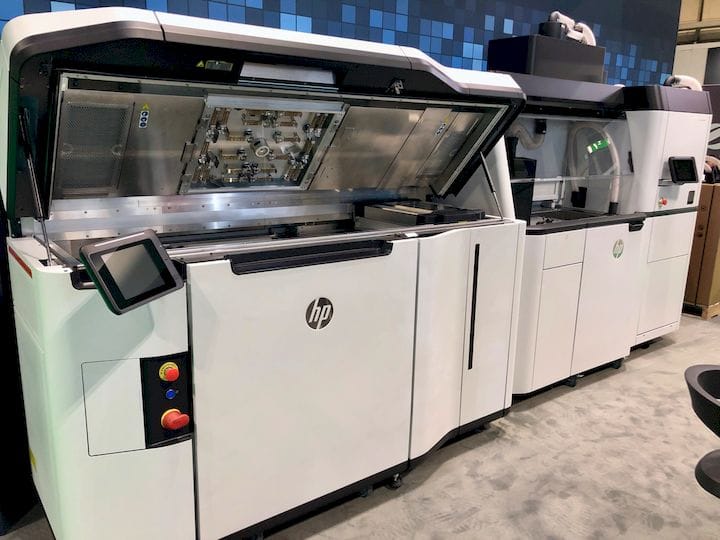
The business case for using additive manufacturing has always been challenging for many industries, but now things are becoming much clearer.
In the early days of 3D printing prototyping was the primary — and often only — use for the technology. This was largely due to the rudimentary, non-engineering materials available to the technology at the time, but there was another barrier to crack.
That barrier was “thinking”. As a “fragile” technology, most manufacturers dismissed additive approaches out of hand. Most of the time they were correct, but this dismissal was so prevalent in the industry that it became the standard response to all situations.
This made it incredibly challenging later for 3D printer manufacturers who eventually did produce equipment capable of using proper engineering material to make actual end-use parts. Many years were spent persuading manufacturers to consider the use of AM in their operations, and initially this was done experimentally on small or non-critical parts.
Over the course of many years these small beginnings gradually grew into proper production, and today we see many companies — but not the majority — making serious use of AM in their production.
Today I read an interesting case study by HP that illustrated this transformation.
Their client, L’Oréal, has been using HP equipment to help their production — but in a rather different fashion. Instead of producing the end-use products, they are using AM to produce custom “pucks” that are used to fill products. It’s a type of jig, as I understand it.
The key here is that L’Oréal has many types of products, and they are constantly changing as the company strives to keep up with consumer trends. It’s a difficult business to be in, as their market changes constantly. Because of that their product lines are always switching up.
This means the company must also remake their production lines accordingly, and thus the need for the customized pucks. By producing them essentially on-demand, they can very rapidly change their production and incorporate new ideas for streamlining the work. HP said L’Oréal was able to reduct assembly costs by around 33%, and production time by an amazing 66%.
That’s all good, but what’s really happening here?
Sharp-eyed readers will recall that 3D printing technology is most desirable for:
- Parts that are produced in relatively low volume
- Parts that frequently change design, even per unit
- Parts able to support high production cost
That’s the magic formula for applying 3D printing to an application. If it meets most those characteristics, it will probably work.
But here’s the thing: when applying this formula, most people think about the end product or parts for the end products. Why not? After all, that’s what the manufacturer is doing, right?
Wrong. In the L’Oréal scenario, the production line itself was considered to be an application. The parts that make the parts are, you guessed it, also parts.
L’Oréal made an important breakthrough here by shifting their view of parts to a wider zone, and were thus able to detect this new application for their operation.
I believe there are many more “hidden” applications for AM in many organizations that could be quite feasible. However, we may not discover them because we’re just not thinking about the problem in the broadest possible way.
Via HP