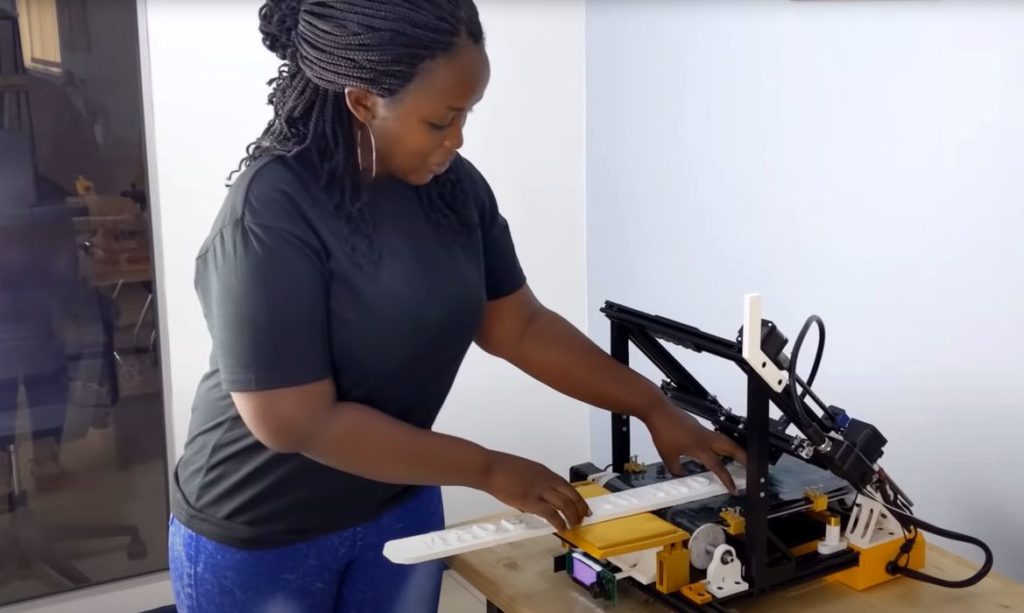
Belt 3D printers are becoming more popular, but they can be expensive. Can you build one instead?
That was the question facing Swaleh Owais, a Canadian engineer and 3D printing enthusiast.
Belt 3D printers are becoming highly desirable because of their ability to 1) 3D print very long objects, far larger than the printer itself, and 2) print a continuous stream of objects in unattended mode.
There are a number of belt 3D printer options on the market today, with the lowest cost model being offered by Creality, the CR-30, at around US$1000. That’s quite a bit more than commonly available basic desktop 3D printers, which can run US$200-500.
An alternative might be to find an open source design for a belt 3D printer and get to it. However, while such plans exist they involve many parts to be bought and printed, and comprehensive assembly activities. It’s entirely possible to build one in this way, but the effort and expertise required are beyond many people’s skill levels.
Owais had another idea: why not take an inexpensive 3D printer and convert it into a belt 3D printer with some (relatively) straightforward modifications? Is this actually possible?
Indeed it is. Owais documented his journey in a recently published video where he transformed a stock Artillery Hornet desktop FFF 3D printer into a belt 3D printer. This device costs a very low US$179, far lower than the cost of a belt 3D printer.
The process involved 3D printing a number of parts, presumably done before taking apart the machine and rebuilding it. These would provide mounts for the belt that would travel over top of the heated print surface, tip the extruder 45 degrees, and rearrange other features to accommodate belt 3D printing.
The new belt 3D printer required flashing its firmware to a new version produced by Owais, which basically respecified the maximum Z-axis limit. The machine also requires use of a software slicing tool that understands belt 3D printers. He recommends using the custom BlackBelt Cura, which I’ve also used.
Perhaps the most interesting aspect of this build is the nature of the belt itself. The belt is a critical component that must be not only flexible, but it must also be durable, adhesive to the print material, and withstand heat.
In my long-ago experience with the ancient MakerBot CupCake automated build platform, the belt was the point of failure: after several prints the belt material would bulge, fouling the leveling and causing me to abandon the hardware completely.
Here Owais undertook a detailed study of different materials for the belt, but ended up with a solution that in retrospect seems obvious: buy a purpose-built 3D printer belt. His supplier was none other than PowerBelt, the makers of the upcoming TinyBelt 3D printer. This belt material hits all the necessary specifications, and enabled Owais to produce a working belt 3D printer for a rock bottom price.
Well, the price plus some effort to put it all together.
If you’re interested in trying this approach to obtaining a belt 3D printer, you’ll certainly want to watch this video and use the approach Owais has pioneered.
Via YouTube