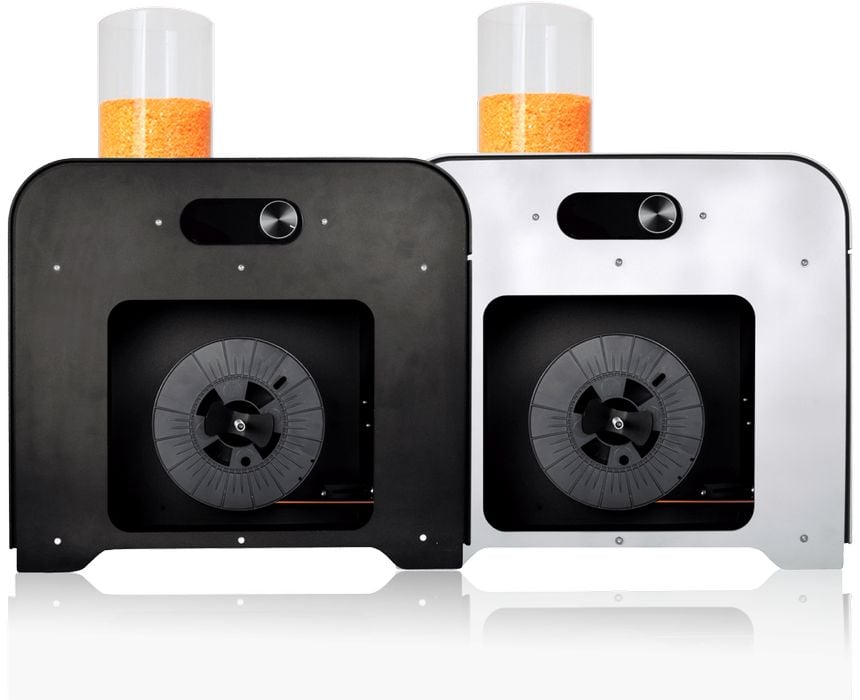
I had a look at 3DEVO’s product line and found they’ve been slowly making it even more powerful.
3DEVO is perhaps the only successful manufacturer of a desktop filament production device. In other words, you can feed in raw plastic pellets into their system, and it will produce usable 3D printer filament.
It sounds straightforward, but the process is absolutely not easy at all. I’ve seen quite a few “filament machine” startups over the past ten years and virtually all of them have failed miserably for one reason or another.
Meanwhile, Dutch company, which launched way back in 2005, has been quietly improving their system. While early machines from others were simple extrusion systems that literally spilled fresh, hot filament on the floor, 3DEVO has taken into account all aspects of filament making.
Some of the features of the 3DEVO system include:
- Ability to precisely shred scrap material
- Drying the input material before use to increase quality
- Precision control over thermals and motion
- Effective take-up spool
3DEVO representatives told us they continue to improve the machine, adding even more features to make it user-friendly. Some of the best ease-of-use features include:
- Ability to change filament diameters from 0.5-3.0mm
- Four separate heating zones
- Regular firmware updates
- Ability to mix materials on input
- Hardened extruder screw for composite materials
- Extrusion temperatures up to 450C to handle most engineering materials
- Lifecycle operations display
- Material pre-set programs for consistent results
- Perfect roundness due to vertical extrusion orientation
- Optical sensors for diameter tolerance of near 0.05mm
- Dual air-cooling system
3DEVO has introduced a new automated belt feature that they tell us will result in fewer operational issues. That’s typical for this company: gradual improvement.
There’s a lot more, but as you can see 3DEVO has been adding features over many years to achieve this level of refinement.
But perhaps the most important of the company’s achievements is to find a viable market niche.
This style of equipment is not useful for true production, as it is not really scalable. It’s for small batches only.
But who needs small batches? DIY 3D printers have a general interest in making their own filament — to save money and participate in recycling environment. However, the cost of the 3DEVO system is approaching €15,000 (US$16,300), so it’s entirely out of the price range for that market.
Instead, 3DEVO’s market is education. The idea is that research labs in Universities, and private businesses, may wish to experiment with new and unusual filament types of their own design. The 3DEVO Composer and Precision systems are ideal for this purpose, and are most times within the price range for that market.
3DEVO tells us there are plenty of experiments underway working on recycling solutions of various types, and they would know as they provide consulting to their customers.
This one achievement is what permits 3DEVO to move forward in a financially viable manner.
The 3DEVO filament making system is not for everyone, but for those that do require that functionality, it’s most likely the best option on the market today.
Via 3DEVO