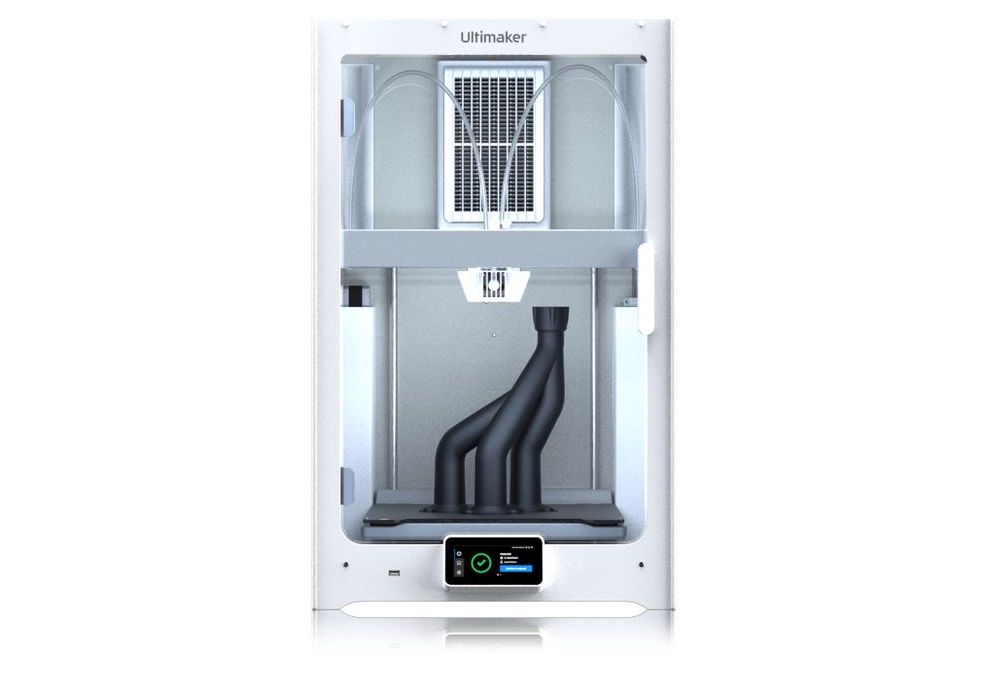
UltiMaker announced a new 3D printer, the UltiMaker S7.
After quite a long wait, UltiMaker has a new flagship 3D printer, the UltiMaker S7. The last key 3D printer announced by the company was the S5, launched in 2018. In the interim the company has been busy building their, 3D print ecosystem, increasing the filament handling capabilities and the small matter of merging with MakerBot, as well as dealing with the pandemic.
But now it seems they’re back on track with the new S7. UltiMaker explains:
“We took everything our customers love about the award-winning UltiMaker S5… And made it even better. The S7 is packed full of our latest technology, making it easier than ever to 3D print high-quality parts.”
The S5 has been a hugely successful product for the company, and they are building on that success with the new S7.
A quick look at the specifications reveals that the S7 is actually physically very similar to the S5: both have a build volume of exactly 330 x 240 x 300 mm, and the external dimensions of the machines are identical. There is a slight difference in weight, however, as the S7 weighs 8.5kg more than the S5: the differences are internal.
Five Big Changes on the UltiMaker S7
There are five improvements on the S7 over the S5, and let’s take a look at each.
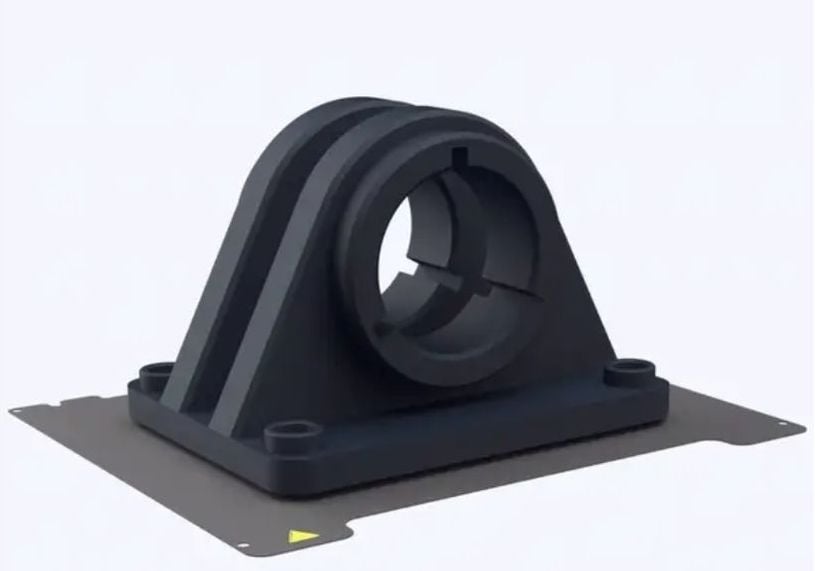
Perhaps the biggest change is the addition of a magnetically attached flexible build plate. This approach to print surfaces has become a de facto standard among most devices on the market, but UltiMaker’s recent equipment has used glass surfaces. It seems they’ve finally recognized that operators do want this type of print surface, and they’ve added it to the S7. This should make print removal quite a bit easier, as you can simply twist the plate to pop off parts.
Another angle not mentioned by UltiMaker is the future possibility of marketing more types of print plates that are tuned for different engineering materials. You could have a plate designed for PC, or PA materials, for example. I suspect they may do this in the future, and coordinate this with their many materials partners.
Along with the new print plate, UltiMaker has fitted the S7 with a completely new bed sensor. This is the sensor that is used during calibration and leveling, and is a critical element of successful prints. It seems to me that they really had to make this change to match the new print plate, which is metal instead of glass.
The third big change on the S7 is the addition of a new filtration system that is capable of removing most ultra fine particles. These nano particles are generated when most filaments are heated to softening temperatures. Both UFPs and VOCs are typically emitted. The new filtration system is said to remove “95% of ultrafine particles”. It’s not 100%, but remember that most 3D printers have zero filtration.
This is an important feature, more than many might suspect. UltiMaker will open up a large market of office and school prospects that require safety measures like filtration. They would have been buying alternative equipment, but now can consider UltiMaker.
There is a redesigned print head that apparently detects flooding, which I’m sure the machine maintenance manager will appreciate.
UltiMaker has relocated the internal camera so that it provides a better top-down view of the print action, likely based on feedback from S5 operators.
One of the most important features is that the S7 is downward compatible with the S5. This means that any print jobs prepared for the S5 will immediately work on the S7 without change. This will be incredibly valuable to those businesses with large libraries of pre-sliced jobs, as they won’t have to re-slice everything when upgrading to the S7.
Imagine if you had thousands of jobs to re-slice. In such a situation you might even consider alternative equipment because if you’re re-slicing everything anyway, why not change? The downward compatibility is a critical feature for the S7, and likely for any future equipment as well.
This compatibility challenge also implies that UltiMaker will not be changing from their 2.85mm filament format for a long time, if ever.
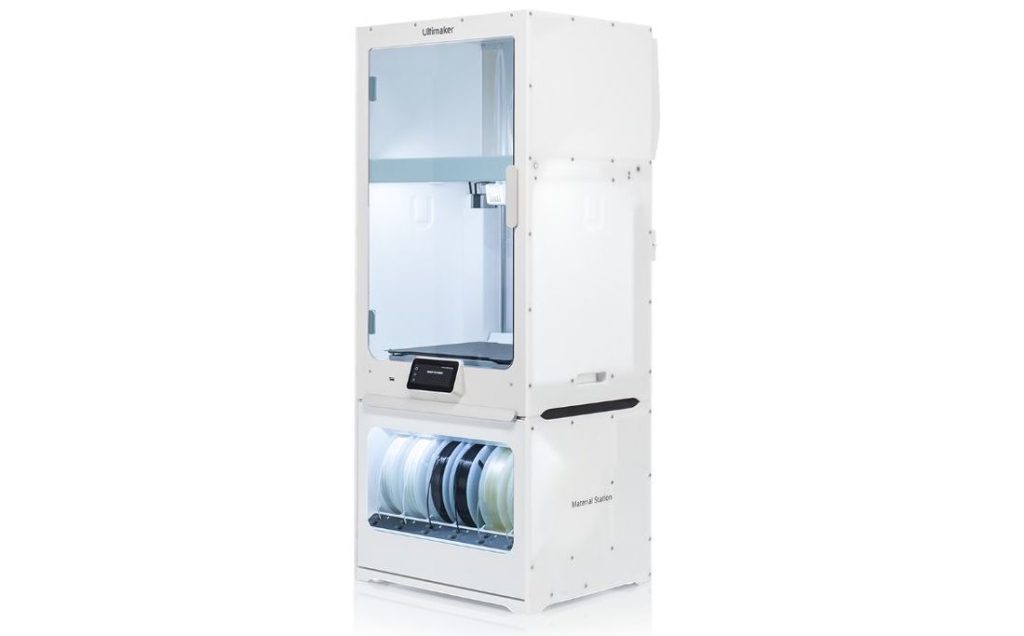
Finally, the S7 is fully compatible with UltiMaker’s popular “Material Station”, which involves placing the S7 on top of the Material Station. This device can manage up to six different filaments, and can automatically load them on demand. It also serves as a “dry box” for hygroscopic engineering materials to ensure top quality prints every time.
The UltiMaker S7 appears to be a solid upgrade to the already solid S5. It’s fully compatible in many ways, and should be a hit with existing UltiMaker customers.
Via UltiMaker