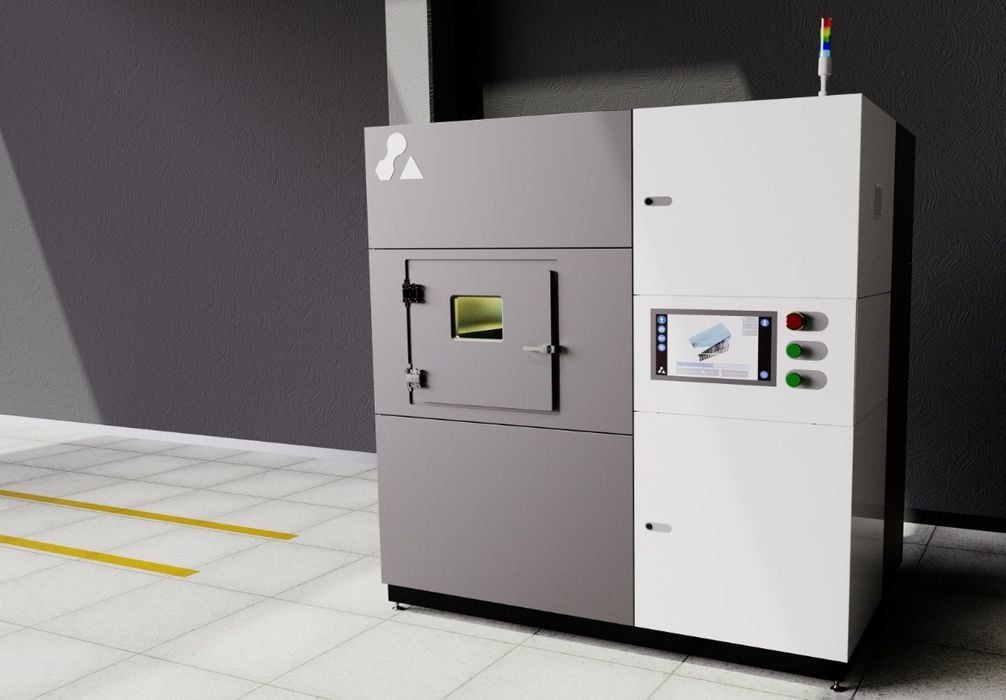
Aurora Labs unveiled a new metal 3D printer, the AL250.
The Australian company has been somewhat quiet over the past few years, but evidently they’ve been at work developing the new AL250 3D printer. The AL250 is the successor to their original device, the RMP-1.
As a refresher, Aurora Labs developed an unusual approach to the traditional LPBF process in order to meet their goal of 3D printing one tonne of metal in 24 hours.
Their secret sauce is a parallel recoating system in which multiple layers are put down during each recoating sweep. The layers are staggered slightly, allowing multiple lasers to begin work on the layers as soon as they appear. This parallel approach isn’t used by any other LPBF manufacturer, and it is potentially highly scalable.
The new AL250 has a number of refinements over its predecessor, the RMP-1.
The main difference seems to be in temperatures. The recoating system now includes a “dosing system” that pre-heats the powder for more consistent spreading and densifying. This in turn should increase part quality substantially.
The AL250’s build plate is now also heated to 200C, which enables the use of more types of metal powders.
Another key difference with the new machine is that the recoating system is now bidirectional. This will offer a substantial speed up, as there will be no waiting for the recoater arm to reposition on the “correct” side before recoating. Left, print, right, print, and so on.
Bidirectional recoating has been used by a few other LPBF manufacturers, but it’s surprising to see Aurora Labs do so. Their recoating system is already quite complex, and making it able to operate bidirectionally is quite a feat.
Aurora Labs said the AL250 includes a 250 x 250 x 300 mm build chamber, and 1500W lasers with a spot diameter of only 0.075mm.