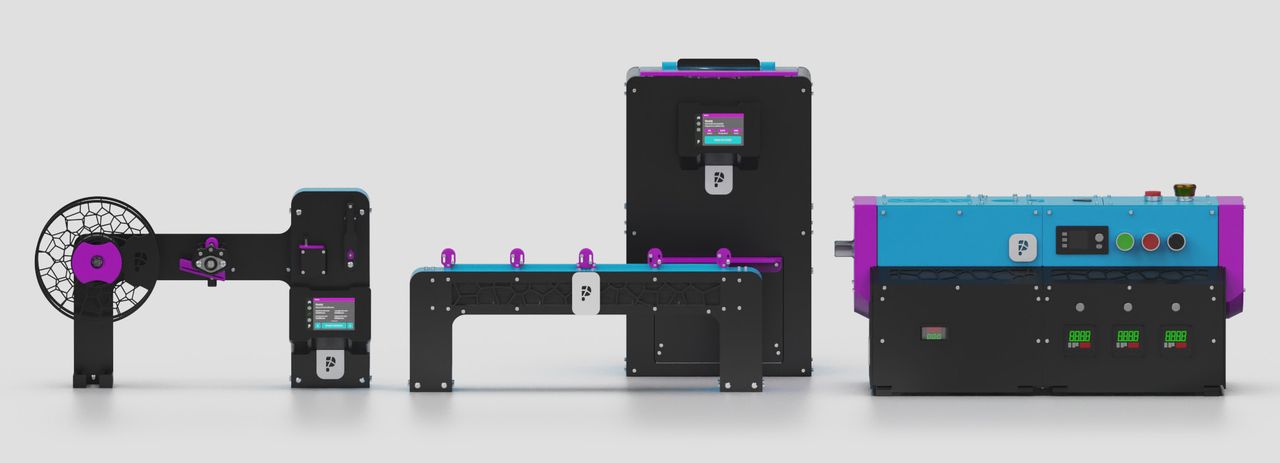
Polystruder adds to their suite of filament production equipment.
The California-based company was launched only a couple of years ago, triggered by the need to deal with the accumulation of unwanted 3D prints. This is an issue that every 3D printer operator must deal with, and it’s good to see there could be another solution.
The idea is to take the waste prints and somehow recycle them into usable 3D printer filament, and that’s what Polystruder’s product set is intended to do.
Currently their product vision includes:
Polystruder GR Pro: An intelligent plastics shredder. It uses an AI-based algorithm to automatically adjust the grinding speed for the material detected, and reduces print scraps to pellet-sized form.
Polystruder XR Pro: an extrusion system that produces filament from scraps, which uses three independent heating zones and three zone cooling fans. The machine is standard to 250C, but optionally can be 450C for engineering materials. It can produce up to 1.5kg of filament per hour.
Polystruder CR Pro: A separate filament cooling unit that uses an advanced cooling system to ensure filament produced maintains its shape and diameter.
Polystruder SR Pro: An “automatic” spooling system for filament that has “0.001mm sensitivity”.
As you can see, Polystruder has broken down the stages of filament production into appropriate standalone devices that can be chained together to produce a proper manufacturing line: chop, heat & extrude, cool and condition; spool.
As of this writing, only the shredder is available for pre-order (US$1,999), while the other units are “Coming Soon”. It may be a while before you can deploy a full end-to-end Polystruder setup.
I am very curious to see how well this system works, as there have been countless attempts to succeed at small-scale filament production and recycling. Most of those attempts, however, involved trying to put all the functions into a single box, which apparently is not Polystruder’s approach. They may have a formula that works.
Given the price of the shredder and expected price points for the remaining units, it’s unlikely the Polystruder system would be affordable by individuals. Instead, the system would be targeted at small to medium sized 3D print workshops that produce sufficient quantities of waste prints.
Such targets might include university labs, libraries with 3D printers, makerspaces and fabrication labs. All of these would no doubt be aligned with the notion of recycling and onsite production of filament.
But in the end, it has to make sense. If the cost of producing a 1kg spool of recycled filament with the Polystruder system ends up to be US$100, then it would be less expensive to simply buy a non-recycled spool online.
When we know the price lives of the remaining Polystruder units, it might be possible to work up a financial model that could indicate the break even point: there would be an amount of recycling that brings the price down to affordable levels. More recycling means more ways to defray the costs of acquiring the Polystruder equipment.
I’m keeping an eye on Polystruder to see how their system works out.
Via Polystruder